
Introduction to Creep Testing Machine
Creep testing machine evaluates material deformation under constant stress. Measures tensile strength (kN/m, ISO 10319), creep rupture time, & strain. Used in aerospace, energy, geosynthetics (e.g., DW1290: safe, durable, customizable temp control).
Contents
Definition of creep
The phenomenon that materials slowly undergo plastic deformation under long-term constant temperature and constant stress.
Terminology of creep test
- Tensile strength: The maximum load per unit width of a specific material when subjected to an external tensile load, measured in accordance with ISO 10319. Tensile strength is expressed in kilonewtons per meter (kN/m).
- Pretension force: A tensile force applied to a specimen equal to 1% of the tensile strength (3.1) but not more than 10% of the tensile creep load, so that the gauge length and strain are determined under repeatable conditions.
- Tensile creep strain: The change in tensile strain of a specimen with time under a constant tensile load.
- Tensile creep rupture: Tensile failure of a specimen under a constant tensile load less than the tensile strength. In some materials, tensile creep rupture is preceded by an increase in the strain rate.
- Tensile creep load: A constant tensile static load applied to a specimen per unit width. Tensile creep loads are usually expressed as a percentage of the tensile strength of the specimen. The tensile creep load includes the pretension force and, if applicable, any load applied by the loading device. The tensile creep load is expressed in kilonewtons per meter (kN/m).
- Loading time: The time required to apply a full tensile creep load. Loading time is expressed in seconds.
- Creep time: The time from the end of the loading time to the tensile creep rupture of the specimen.
- Tensile creep rupture time: The time from the end of the loading time to the tensile creep rupture of the specimen. Tensile creep rupture time is expressed in hours.
Working principle of creep testing machine
The working principle of the creep testing machine is to simulate the material stress in the actual working environment by applying a constant external force or deformation to the sample, and controlling environmental factors such as temperature and humidity, and measure the deformation or stress value of the sample over time. In the creep test, the sample is usually placed in a high temperature environment to accelerate the creep process. During the test, the deformation data of the material is recorded in real time through high-precision sensors and data acquisition systems, providing a reliable basis for material performance evaluation.
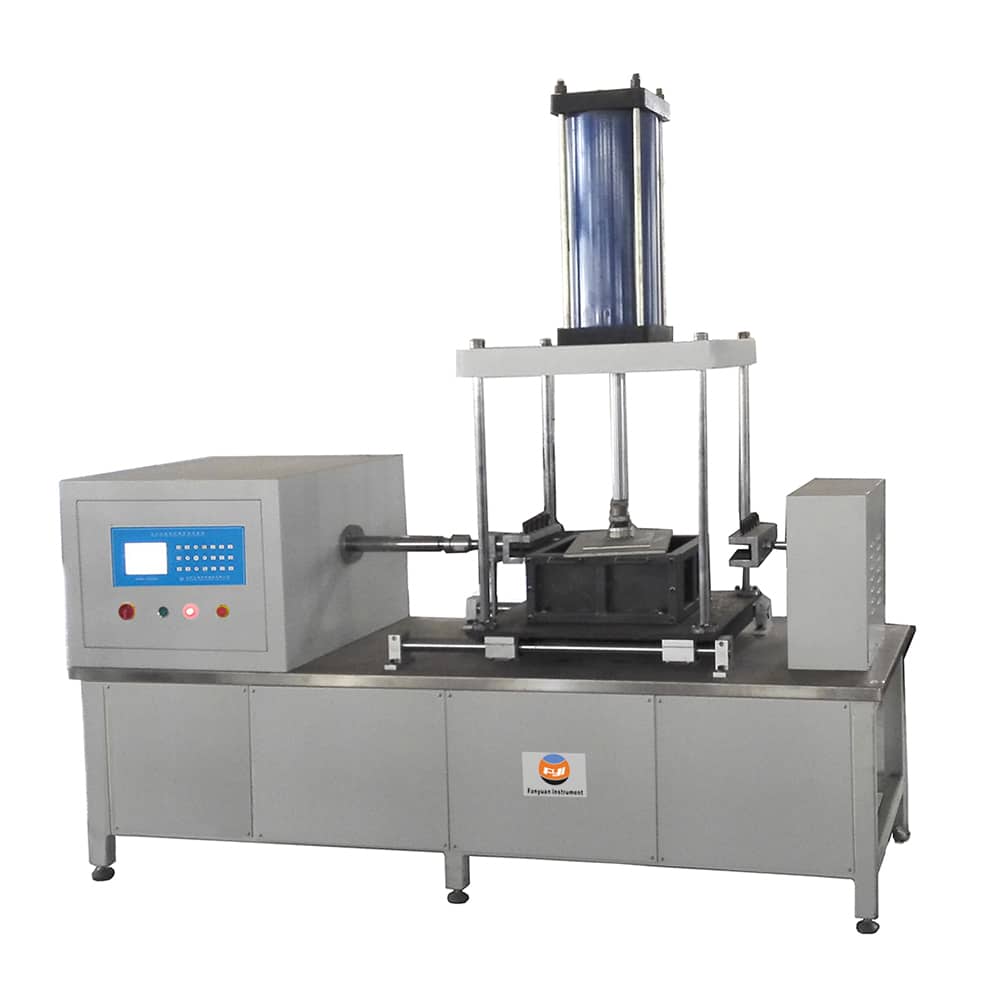
The structure of creep testing machine
1. Loading system: a component used to apply a constant load, usually including a heavy hammer, oil pressure or air pressure system.
2. Measurement system: used to monitor and record the displacement and deformation of the material in real time, usually using a displacement sensor or a tension sensor.
3. Control system: responsible for operating and controlling the test process, including the setting and automatic adjustment of parameters such as temperature, pressure, and load.
4. Data acquisition system: used for recording and processing data to facilitate subsequent analysis and research.
Experimental steps of creep testing machine
1. Sample preparation: Prepare the test sample according to the standard, and the size and shape must comply with the relevant test standards, such as ASTM, ISO, etc.
2. Clamp the sample: Fix the sample in the loading device of the testing machine to ensure that the sample does not slide or deform and fail when the load is applied.
3. Apply the load: Apply a constant load according to the experimental requirements, and turn on the heating system at the same time (if temperature control is required).
4. Real-time monitoring: Monitor the deformation of the sample in real time through the measurement system, and record the data at different time points.
5. Data analysis: After the test, analyze the collected data, draw the creep curve, and evaluate the creep characteristics of the material.
Application
Creep testing machines are mainly used to test the deformation behavior of materials under constant stress, especially the performance under high temperature, high pressure and high stress environment. Specific uses include:
- Tensile, compression endurance, creep and relaxation tests of metal and non-metal materials: Creep testing machines can simulate these working conditions and evaluate the performance changes of materials under these conditions
- Creep fatigue test: used to test the creep and fatigue properties of materials under high temperature, high pressure and high stress environment. Creep refers to the phenomenon that materials gradually deform over time under constant stress, while fatigue refers to the phenomenon that materials are damaged after a certain number of cycles under alternating stress. This test is of great significance for the design and selection of materials in practical applications, especially in important fields such as aerospace, electricity, and nuclear energy.
- Performance evaluation of plastics, polymer materials and composite materials: Creep testing machines are also widely used in long-term stress testing of these materials to evaluate their deformation behavior under high temperature or long-term stress, and predict service life and reliability.
Geotextile Tensile Creep Tester DW1290

Numerous variables, including the kind of reinforcing material, temperature, degree of damage, load intensity, and enclosure conditions, affect the creep characteristics of geosynthetic materials. The complexity of creep testing is determined by the difficulty of simulating the real scenario in indoor tests. At the same time, the creep process takes a long time to observe and requires ongoing investigation.
The main determinant of whether reinforced soil can be utilized in long-term projects is creep. The long-term performance of reinforced soil structures is impacted by creep characteristics. Changes in the stress state of reinforced soil structures can result from both creep and stress release, which can cause the structure to become unstable or deform excessively. Predicting the long-term creep of geosynthetic materials is therefore essential.
The following are the features of the geosynthetics creep tester:
- Safety design: the motor is installed inside the creep tester;
- Easy to operate: put in the sample, start the motor, and finally close the working room;
- Durable;
- Advanced functions such as temperature control and normal pressure can be customized according to customer requirements.