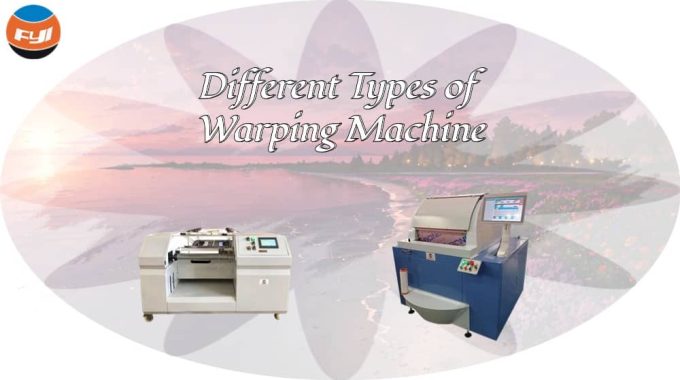
Different Types of Warping Machine
The warping machine is a machine that neatly winds the cheese yarn into warp beams at a constant speed and under the same tension according to the number and length of warp yarns required by the process for use by the warp knitting machine.
The warping process can be divided into beam warping, sectional warping and ball warping according to different yarn types and process requirements.
Contents
Beam warping machine
Definition
Also known as batch warping machine, a certain number of warp yarns are wound in parallel on the warping beam, and then several warping beams are combined, sized, dried and wound into a weaving beam. This method is to divide the total number of warps required for the fabric into several batches that are as equal as possible, and wind them onto several warp beams according to the length specified by the process.
Features
The characteristics of beam warping machine are fast warping speed, high production efficiency, and suitable for mass production; the disadvantage is that there is a lot of yarn waste. For warping of multi-color or different twist direction warp yarns, the arrangement of the color warps is difficult. Therefore, it can only be used for warping self-made fabrics or single-color fabrics. Most of the warp beams need to go through a sizing process to form a weaving beam, so they are suitable for warping single-color yarn fabrics.
Sectional warping machine
Definition
According to the color cycle and creel capacity, divide the total number of warps required for the fabric into several equal number of strips. The warp strips are wound onto the warping drum in parallel one by one according to the specified width and length, and finally all the warp strips are rewinded onto the weaving beam.
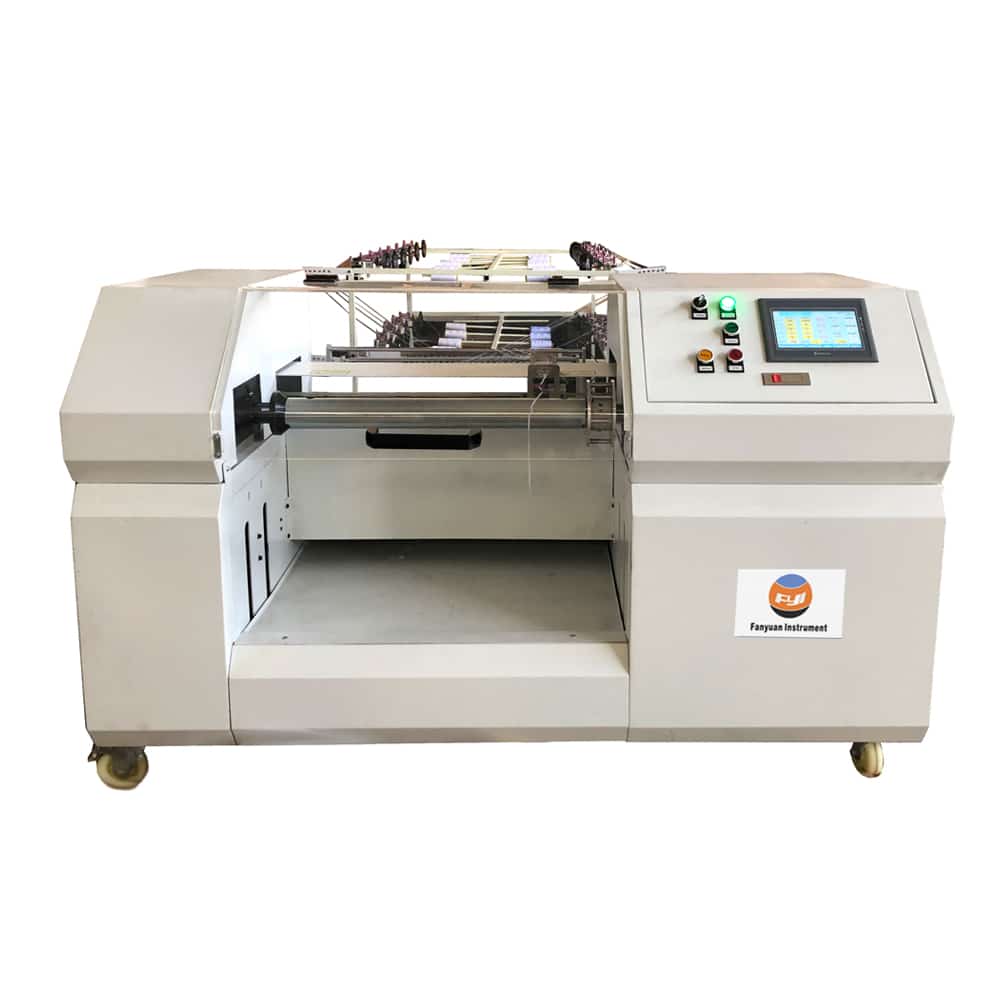
Sectional warping is to divide all the warp yarns of the fabric into several small parts, and each small part is wound on a large drum in the shape of a strip. After the length reaches the required length, it is cut and consolidated, and the second and third strips are rolled in sequence… until all the strips of the process design are completed. After all the strips are rolled, they are unwound from the large drum and wound onto the weaving beam.
Process flow
Warping: creel → rear reed → splitting reed → fixed width reed → reverse shaft
Features
- Twice winding and forming (winding one by one, rewinding), the production efficiency is low, and the tension between each strip is not uniform enough;
- The pattern arrangement is very convenient, and products that do not require sizing can directly obtain the weaving beam, which shortens the process;
- Suitable for small batch production of silk, wool and yarn-dyed products.
Ball warping machine
Definition
First, a certain number of warp yarns are bundled and wound into a mesh ball-shaped yarn mass, which is then dyed and then wound into a warp beam on a warp drawing machine. The warp yarns warped in this way are evenly dyed and are suitable for high-grade colored fabrics such as denim.
Structure
The ball warping machine consists of two parts: creel and warping head. Place conical or cylindrical bobbins on the creel. The yarn is drawn out from the package and passes through the tension device, then passes through the guide rod on the warping machine, passes through the telescopic reed, bypasses the yarn guide roller, and is wound on the warp beam. The warping machine is also equipped with devices such as upper warp beam, lower warp beam, length measurement and full beam automatic stop.
Creels are divided into four types: V-shaped, half-moon, rectangular and rectangular-V-shaped.
According to the way of yarn unwinding, it is divided into two types: axial type and tangential type;
According to the way of changing the bobbin, it is divided into two types: intermittent type and continuous type;
According to whether there is a prepared package, it is divided into two types: single type and double type. The single type is an intermittent type, and the duplex type is divided into continuous type and intermittent type. Only working bobbins are installed on the single creel. When the yarn on the entire batch of bobbins has been unwound, the machine will stop and take out the empty bobbins, and then start the machine again after replacing them with full bobbins. The tension of each warp yarn in a single creel is relatively close, it occupies a small area and is easy to operate. However, there is a lot of yarn returned after changing the bobbin, so it is suitable for the production of cotton, wool and silk fabrics with high quality requirements. The compound continuous creel is equipped with two sets of package brackets, into which the working package and the preparation package are respectively inserted. The yarn tail of the working package is connected to the yarn end of the preparation package. This kind of creel does not need to stop when changing the can, which can improve the productivity of the warping machine. However, the creel occupies a large area and the tension of each warp yarn is greatly different.
In order to improve the efficiency of the warping machine, a rotary creel with collective can change and a trolley combined creel can be used. The rotary creel consists of a preparation creel and a working creel. When the yarn on the working creel is about to be unwound, the preparation creel is rotated to the working side and connected to the head to become the working creel. The trolley combination creel is composed of several movable trolleys and frames. When the yarn on the creel of a group of trolleys is unwound, the empty trolley leaves automatically and the full trolley enters the working position.
The creel is also equipped with automatic yarn clamping, super-tension breaking and tension adjustment devices. The high-speed warping machine uses a thyristor DC speed-regulating motor and a hydraulic variable-speed oil motor to directly drive the warp beam, and has automatic end-stop, automatic pressurization, automatic upper and lower shafts and high-power hydraulic braking devices.