
What Performance Indicators Cotton Fibers Have?
Cotton is the most important natural textile fiber, as well as cellulosic textile fiber, in the world, used to produce apparel, home furnishings, and industrial products. Worldwide about 40% of the fiber consumed was cotton. But how much do you know about the testing indicators of cotton fibers in the production process?
Contents
Fiber length
Fiber length is largely influenced by variety, but the cotton plant’s exposure to extreme temperatures, water stress, or nutrient deficiencies may result in shorter fibers. Excessive cleaning or drying at the gin may also result in shorter fibers. Fiber length affects yarn strength, yarn evenness, and the efficiency of the spinning process. The fineness of the yarn that can be successfully produced from given fibers also is influenced by fiber length.
Therefore, it is necessary to detect the length of cotton fibers during the production process.
Main Indicators of Fiber Length
The main indicators for measuring cotton fiber length are as follows:
(1) Span length: The minimum length attained by a specified percentage of the fibers in a test beard, corresponding to a determined percentage of the optical density of the beard.
The first section of the length investigated, which is normally situated at a distance of 3,8 mm from the line of gripping of the comb, is taken as the reference base of 100 % optical density.
(2) Length uniformity: The ratio between two span lengths, the smaller value being expressed as a percentage of the higher value.
(3) Modal length: In the distribution of cotton fiber length, the fiber length that accounts for the most mass or quantity of fibers.
(4) Quality length: In the distribution of cotton fiber length, the weighted average length of each group of fibers above the modal length.
(5) Short fiber content: The percentage of short fiber mass (quantity) below a certain length range in cotton fibers to the total fiber mass (quantity)
(6) Average length of mass: The average length obtained by weighting the mass of each group of fibers in the cotton fiber length distribution.
Main Methods for Measuring Fiber Length
There are two main methods for measuring fiber length:
(1) Photoelectric method:Fibers are placed on combs in such a way that they are caught at random points along their lengths to form a beard. The beard is scanned photoelectrically from base to tip, the amount of light passing through the beard being used as a measure of the number of fibers that extend various distances from the combs.
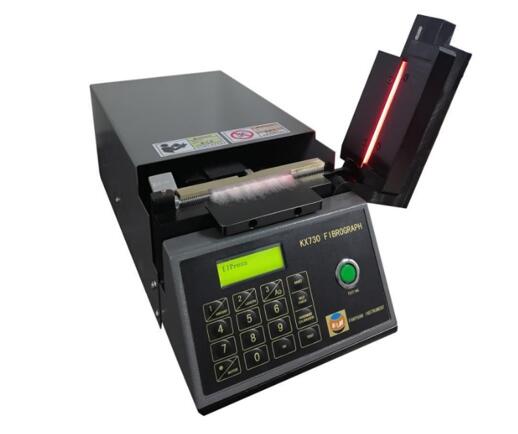
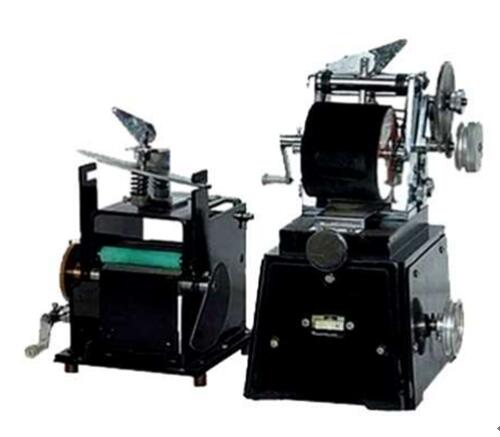
(2) Roller analyzer method: Organize the samples into neat cotton bundles at one end, and then use roller to control the length of fibers for equal distance grouping and weighing, determine the distribution of cotton fiber length, and calculate various length indicators.
Fiber fineness of cotton fibers
Fiber fineness affects processing performance and the quality of the end product in several ways. in the opening, cleaning, and carding processes, low-micronaire or fine-fiber cotton require slower processing speeds to prevent damage.
Main Indicators of Cotton Fiber Fineness
(1) Linear density: The mass per unit length of fibers or yarns.
(2) Micronaire value: A comprehensive indicator reflecting the fineness and maturity of cotton fibers. Micronaire value s are divided into three levels: A, B, and C.
Main Methods for Measuring Fiber Fineness
There are three main methods for measuring fiber fineness:
(1) Cut middles method: According to the definition of cotton fiber linear density, cut a certain length of fiber, weigh its mass, count its’ quantity, and calculate the average cotton fiber linear density.
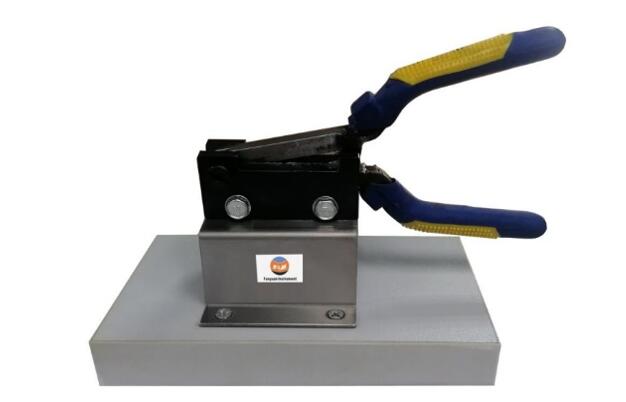
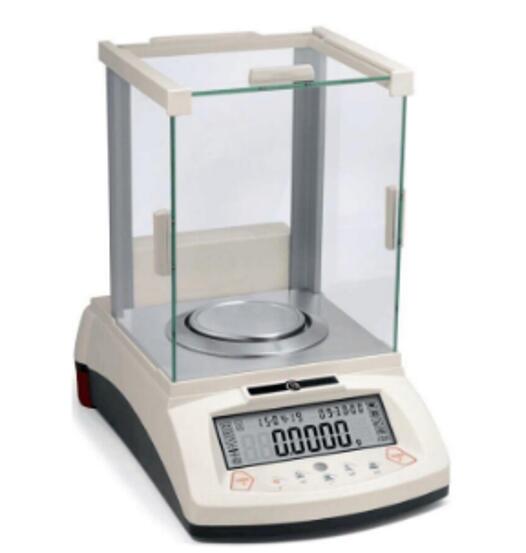
(2) Method of Air-flow: Air is passed through a test specimen consisting of a plug of fibers. The permeability is indicated on a scale for recording variations in either the rate of flow through, or the pressure difference across, the plug. The mass and volume of the test specimen are either a constant for a given type of instrument or varied appropriately in relation to each other. The scale indicating variations in permeability can be calibrated in arbitrary units of micronaire value or marked in the appropriate absolute units of rate of flow or of pressure difference and a table or graph provided for conversion of the observed readings into micronaire values.

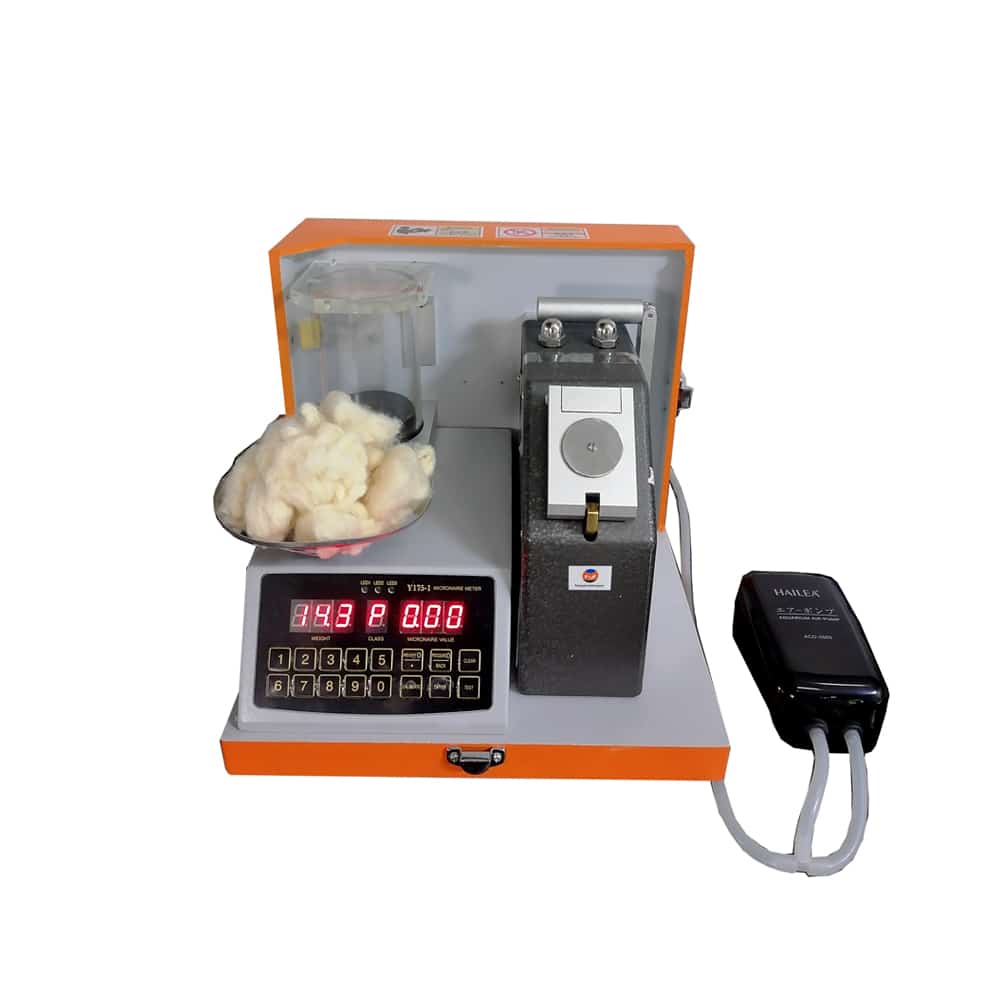
(3) Projection Microscope Method: Projection on a screen of the magnified images of the profiles of wool fiber pieces, and measurement of their width by means of a graduated scale. The operating technique assures a random sampling of the fibers to be measured.
Fiber strength
Fiber strength is largely determined by variety. However, it may be affected by plant nutrient deficiencies and weather. Fiber strength and yarn strength are highly correlated. Also, cotton with high fiber strength is more likely to withstand breakage during the manufacturing process.
Main Indicators of Measuring Cotton Fiber Strength
The main indicators for measuring fiber strength are as follows:
(1) Breaking force: The maximum force applied to a material carried to rupture, usually expressed as N or cN.
(2) Breaking strength: The breaking force per unit linear density, usually expressed as cN/dtex.
(3) Breaking extension: The extension length at stretching to break.
(4) Elongation at break: The ratio of the breaking extension of a material to the length of the material prior to stretching, expressed as a percent.
Main Methods for Measuring Fiber Strength
There are two main methods for measuring fiber strength:
(1) Flat bundle method: A bundle of cotton fibers is combed parallel with the aid of specialized clamps to minimize loose fibers that are in the bundle, secured in clamps, cut to a known length, broken in a tensile testing machine, and weighed. Tensile strength or breaking tenacity is calculated from the ratio of breaking load to bundle mass (weight).
Our Instruments: KX101, YG011
(2) Method for individual fibers: An individual fiber is extended at a constant rate until rupture occurs. The breaking force and elongation at break are recorded. If the breaking tenacity is to be calculated, the linear density of the individual fibers or the mean linear density of the laboratory sample is also required.
Trash content of cotton fibers
Trash content refers to the percentage of trash mass in the raw cotton sample to the sample mass. A high percent area of trash results in greater textile mill processing waste and lower yarn quality. Small trash particles, or “pepper trash,” are highly undesirable, because they are more difficult for the mill to remove from the cotton lint than are larger trash particles.
Main Method for Measuring Trash Content of Cotton fiber
The method commonly used for measuring the trash content is:
Trash in Raw Cotton Analytical Machine Method: A known mass of raw cotton, partially processed cotton, or waste is fed into the machine. The machine, operating on mechanical-pneumatic principles, separates the foreign matter from the cotton and discharges the non-lint particles and lint into separate chambers. The amounts of lint and non-lint recovered are calculated as a percentage of the original specimen mass.
Rate of moisture regain
Rate of Moisture Regain is an indicator of moisture absorption of textile materials. It is expressed as the percentage of moisture content in textile materials by weight to dry materials.
Main Method for Measuring Rate of Moisture Regain
The commonly used for measuring the trash content is:
Oven Drying Method: Weigh a certain amount of test sample and place it in an oven at a certain temperature for drying, allowing the moisture in the test sample to evaporate until the test sample reaches a constant amount. The difference between the original mass and the oven-dry mass is calculated in percent, either as moisture content or moisture regain.