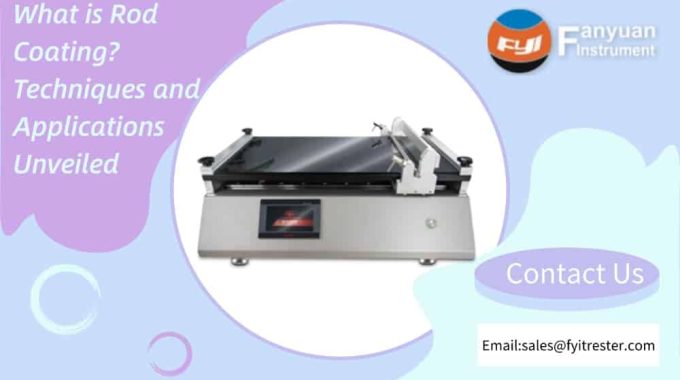
What is Rod Coating? Techniques and Applications Unveiled
Rod coating is a simple wet processing technique used to deposit a thin layer of solution onto a substrate. It involves a rod being placed above a substrate and dragged over a pool of fluid, resulting in the fluid being spread into a thin film or coating. Rod coating is commonly used in the development of applications such as automotive paints, photovoltaic cells and lithium ion batteries. This coating method is also referred to as drawdown coating and rod coating, or wire rod coating and Mayer rod coating, depending on the type of rod used.
Contents
Types of coating rod
There are two main coating rods which are extruded wire rods and spiral film applicator and they are the same in application and can be used interchangeably.
Extruded wire rod
Extruded wire rod is the simplest type, which is a straight rod suspended at a known distance above a substrate and passed through ink to leave a wet film. Using cold extrusion technology, continuous spiral grooves of different sizes are extruded on a smooth steel rod, and the thickness of the wet film coating is controlled by the different sizes of the spiral grooves. The rod does not come into contact with the substrate in the width of the coating area.
Wound wire rods
A wound wire rod is a type of applicator used to apply coatings onto substrates with controlled coating thickness. They are composed of metal, with metal or plastic rods wrapped around them in a spiral or helical pattern, leaving gaps or controlled gaps between the metal rings. Then use a wound wire rod to apply the coating material onto the substrate, leaving a thin and uniform coating. There are various sizes and configurations of wound wire rods with different wire diameters and ring spacing, which can achieve different coating thicknesses. The wire diameter and loop spacing determine the gap or clearance between the wire loops, which in turn determines the thickness of the coating applied. Usually, larger wire diameters and wider ring spacing result in thicker coatings, while smaller wire diameters and narrower ring spacing result in thinner coatings.
Wound wire rods (also known as Mayer rods) come in two types: open wound (less common) and close wound (more common).
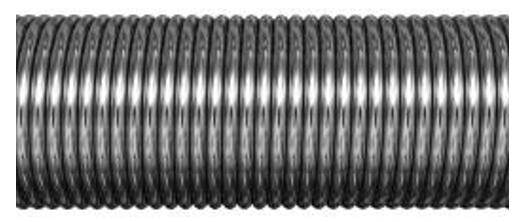

In a close wound wire rod, the wire is wound as densely as possible, completely covering the rod. This configuration typically produces a thinner wet film and is suitable for less viscous fluids that can easily be self-level. Open wound wire rods have wires spaced further apart, exposing some of the rods. The pitch of the winding becomes a critical variable, altering the wet film thickness. Open wound rods are generally better suited for more viscous fluids because the fluid needs to self level less once the rod has been drawn through it.
The advantage of extruded wire rod is that there is no possibility of wire breakage and they are easier to clean, while the advantage of wire rod is that they follow the Mayer rod testing principle more strictly. Due to the different principles of forming grooves between wire rod and smooth rod, the actual coating amount used may vary during the experimental process.
The well-known coating rod
The most representative brands are RDS wire rod produced by RDS in the United States, and OSP extruded wire rod produced by OSG in Japan.
The overall appearance of the RDS wire rod is very delicate. Taking the wound wire rod type as an example, the minimum wound wire diameter is only 0.08mm, which is similar to a human hair. RDS wire rods come in three different specifications based on the diameter of the main rod, namely 1/4 inch, 3/8 inch, and 1/2 inch. At the same time, in addition to the wire winding process, RDS provides 1/4 inch diameter extrusion (die casting) process coating rods.
In terms of application, RDS wire rod is widely used. As a standard coating rod for ultra-thin coating preparation, coating rod is widely used in many segmented industries. Especially widely used in industries such as coatings, paints, varnish, pigment pastes, plastic films, packaging printing, color steel plates, hardware, as well as research institutions.
The Japanese OSP measurement rod is a brand new manual coating machine for extruded wire rods. OSP measurement rod uses precision molds and cold extrusion processing technology to create concave and convex wavy curves on the surface of steel rods, achieving the same coating effect as traditional wire rod manual applicators. Due to the absence of wound wire on its surface, there is no worry of wire loosening or breakage. The curve lubrication on its surface is smooth and very easy to clean. What is commendable is that OSP measurement rods have broken through the limits of traditional wire rod manual coating machine, with a minimum wet film thickness of only 1.5μm, solving the problem of ultra-thin film coating in one fell swoop. The surface of the measuring rod is also coated with hard chromium with a hardness of up to 1300HV, which can greatly improve its wear resistance and service life.
Related machine–coating machine
An Automatic coating machine is a device used for coating thin films in laboratories, replacing manual coating and automating coating to improve the accuracy and efficiency of coating. The working principle of the laboratory automatic coating machine is to evenly coat the sample on the substrate by controlling the coating head and coating parameters, forming the desired thin film.
Our coating machine — TM1000 motorized coating machine is a basic spiral film applicator (wire rod) coating machine that adopts a new spiral film applicator installation method and has speed control and coating length adjustment functions. It is suitable for coating samples of coatings, inks, paints, slurries, lithium batteries, pressure-sensitive adhesives, polymer materials, etc. It can be scraped and applied on glass, cardboard, and fabrics.
