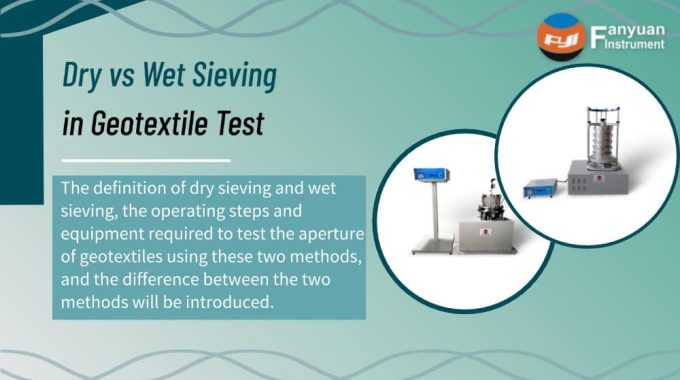
Dry vs Wet Sieving in Geotextile Test
Sieving refers to the process of separating a mixture of different particle sizes into several different particle size levels through a perforated sieve surface. After weighing them separately, the particle size distribution expressed as a mass percentage can be obtained. According to the different moisture content of the powder, it is mainly divided into two categories: dry sieving and wet sieving. The following will introduce the definition of dry sieving and wet sieving, the operating steps and equipment required to test the aperture of geotextiles using these two methods, and the difference between the two methods.
Dry sieving
What is dry sieving
Place the dry powder material in the screening equipment, and use mechanical vibration and other methods to make the powder pass through the screen. After the screening is completed, the weight of the screen residue and the weight of the material on the bottom of the screen are counted. The sum of the two is then subtracted from the weight of the powder initially placed in the screen to calculate the loss during the screening process.
Dry sieving method steps
1. Sample preparation: Lay the geotextile sample flat and forcelessly on the supporting grid, and press it with a clamp to ensure that the sample is horizontal and not affected by tension.
2. Granular material selection: According to the test requirements, select standard granular materials of a certain mass and diameter. These granular materials should have a uniform particle size distribution and a certain hardness to ensure the accuracy and stability of the screening process.
3. Screening test: Sprinkle the standard granular material evenly on the geotextile sample, and then start the vibration system. At the specified vibration frequency and amplitude, the granular material passes through the sieve holes of the geotextile sample, while the larger particles are retained on the sample.
4. Collection and weighing: The particles that pass through the sample flow out of the collection tank, collect them and weigh them. At the same time, record the particle mass before and after the screening test, and calculate the screening rate.
5. Data analysis: Replace standard granular materials of different diameters for multiple tests, and draw a curve of the diameter of the standard granular material and the screening rate, which is the pore size distribution curve of the sample. According to the curve, the effective pore size of the geotextile can be calculated and its filtration performance and particle retention capacity can be evaluated.
Dry sieving apparatus
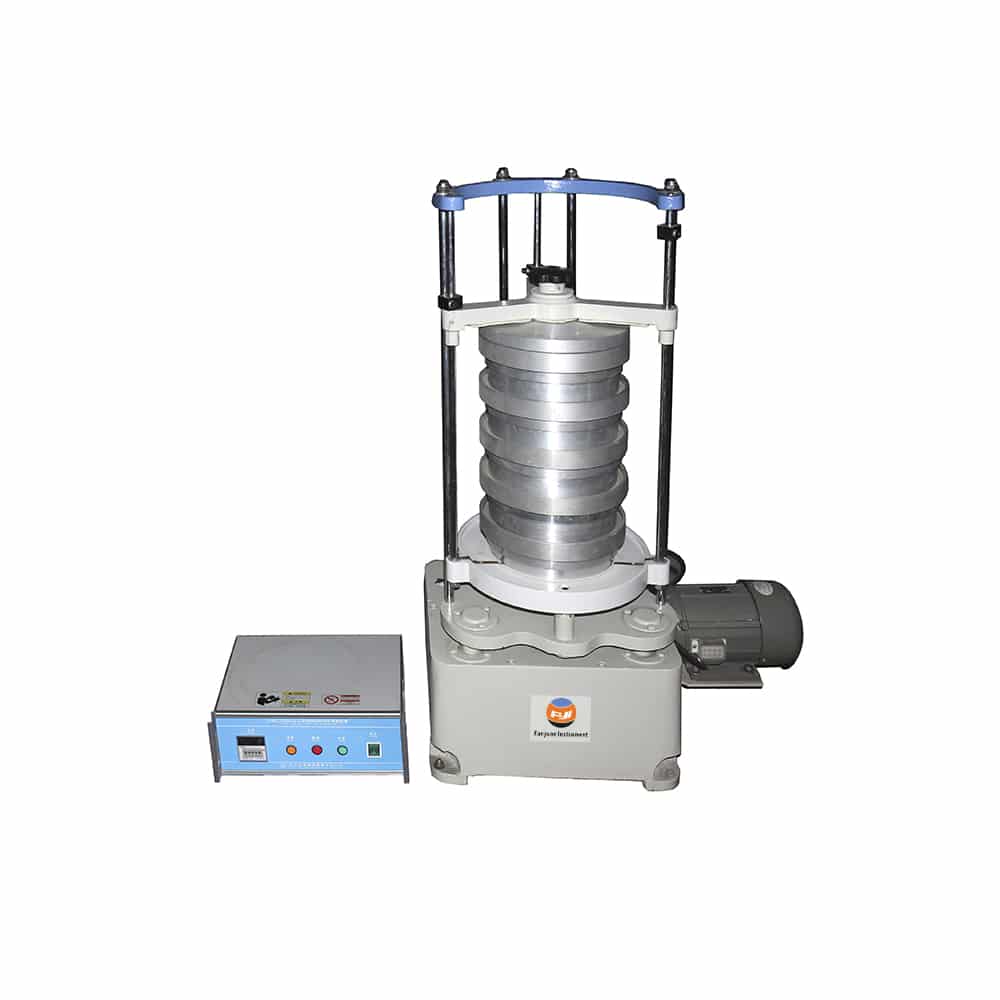
The apparent/equivalent opening size of a geotextile is ascertained using a dry sieve test apparatus. Geotextile and composite geotextile effective apertures can be determined using the effective aperture determination device (dry sieve technique). When it comes to material in the laboratory and laboratory of sieve analysis, the dry sieve method, the pertinent requirements, and its performance meet the national standards applicable to the geological, metallurgical, chemical, coal, defense, scientific research, grinding wheel, cement, and construction departments.
Wet sieving
What is wet sieving
If the powder has a high moisture content, is easy to stick together, and does not react with water, Wet sieving is often better than Dry sieving. Unlike Dry sieving, Wet sieving requires liquid to promote the separation between particles. During the process, the particles are in a semi-suspended state, reducing stacking and backlog, so the screening accuracy will be higher than Dry sieving. In addition, Wet sieving can better adapt to ambient temperature and atmospheric humidity and improve operating conditions.
Wet sieving method steps
Preliminary preparation
Before Wet sieving, you need to make adequate preparations. First, select representative geotextile samples to ensure that their size and state meet the test requirements. Second, prepare the required screens and screening equipment, as well as auxiliary tools for washing and drying. Finally, set parameters such as screening time and water flow rate according to the test standards.
Wet sieve treatment
1. Place the geotextile sample on the sieve and make sure it is flat and wrinkle-free.
2. Rinse the geotextile with an appropriate water flow rate while shaking the sieve to force the particles through the sieve holes.
3. During the rinsing process, pay attention to observe and record the particles passing through the sieve holes for subsequent analysis.
4. After rinsing, dry the particles remaining on the sieve for accurate weighing.
Results Analysis
1. Draw a particle distribution curve based on the data recorded during the flushing process to obtain the effective pore size range of the geotextile.
2. Compare the effective pore sizes of different samples or different batches of geotextiles to evaluate their performance differences and consistency.
3. Combined with the actual needs of the project, determine whether the effective pore size of the geotextile meets the use requirements.
Wet sieving apparatus
Using the wet-sieving technique, the DW1330W Wet Sieve Test Apparatus is used to measure the characteristic opening size of a single layer of a geotextile or product linked to geotextiles. Water is used to wash through an amount of graded granular material that has been spread out on the geotextile’s surface. The graded granular material that passes through the geotextile and functions as soil is evaluated after the geotextile serves as a sieve. The size of the graded granular material transmitted (d90) is matched by the characteristic opening size (O90) of the geotextile.

Difference between wet sieving and dry sieving
Differences in sieve structure
• Dry sieving: Mainly used for screening dry materials, the screen design is relatively simple, and the main focus is on the size and shape of the screen holes to ensure that the materials can pass smoothly.
• Wet sieving: Used to process water-containing or sticky materials, the screen design is more sophisticated to prevent the materials from clogging the screen holes. In addition, the sieves for Wet sieving usually need to have good corrosion resistance to cope with corrosion problems that may occur in humid environments.
Differences in use environment
• Dry sieving: Usually carried out in a dry environment, the moisture-proof and waterproof performance of the sieve is not high.
• Wet sieving: Because the material contains moisture, the sieve needs to be able to work normally in a humid or even underwater environment, so the sieve is required to have good sealing and waterproof performance.
Screening effect comparison
• Dry sieving: When processing dry materials, the screening efficiency is high and the screen holes are not easy to clog.
• Wet sieving: When processing water-containing or sticky materials, the screening efficiency may be affected to a certain extent, and more attention needs to be paid to the clogging of the screen holes.
Application scenarios
• Dry sieving: commonly used for coarse screening, suitable for grading dry materials.
• Wet sieving: used for fine screening, especially when it is necessary to determine the soil content in sand and gravel samples.
Operating environment
• Dry sieving: the operating environment is relatively simple, but a separate dust collection device may be required.
• Wet sieving: the operating environment is better and no separate dust collection device is required.