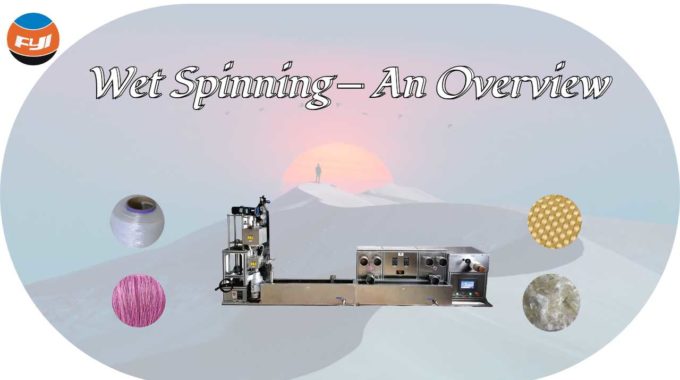
Wet Spinning – An Overview
Last updated: March 21, 2025
We update the content regularly to ensure the accuracy and usefulness of the information. If you have any suggestions or questions, please feel free to contact us!
Contents
What is wet spinning?
Wet spinning is a kind of solution spinning and belongs to the spinning method of chemical fiber. Depending on the different property of the polymer fiber. There are two main spinning methods of chemical fibers: melt spinning and solution spinning. In addition, there are special or unconventional methods of spinning, such as electrospinning, solution blow spinning. Among them, according to the different solidification mode, solution spinning method is divided into wet spinning and dry spinning.
In the production of chemical fibers, most of them are produced by melt spinning, followed by wet spinning. And only a few are produced by dry or other unconventional spinning methods.
Dry jet wet spinning
A variant of wet spinning is dry jet wet spinning, which is called dry-wet spinning for short. It is a chemical fiber spinning method which combines the characteristics of dry spinning and wet spinning. This is a new spinning method developed in the 1960s.
After the spinning solution (sometimes called a “spinning dope”) is pressed out of the spinneret. It passes through a space (3 ~ 100 mm, generally less than 20 ~ 30 mm) and then enters the coagulation bath. The gas in space can be air or some other inert gas.
When using dry jet wet spinning, the trickle flow of the spinning solution can undergo significant spinneret stretching in the air. And the length of the stretch zone is far longer than the length of the swell zone of the flow. The axial deformation of the liquid flow occurs over such a long distance, and the velocity gradient is not large. In fact, there is no great deformation in the swelling region. In contrast, in wet spinning, spinneret stretching takes place over a very short distance, the velocity gradient is large, the swelling zone of the liquid flow is severely deformed. And the spinneret stretching causes the filament to break. Therefore, using dry jet wet spinning can improve the stretching ratio and spinning speed of the nozzle.
The spinning speed of dry jet wet spinning can reach 600 ~ 1200 m/min, which is much higher than that of wet spinning. And the spinneret with larger aperture (φ=0.15 ~ 0.3 mm) can be used. However, the concentration and viscosity of the spinning solution can be as high as that of dry spinning. What’s more, the structure formation process of the fiber can be controlled effectively by dry jet wet spinning. In dry spinning, the solidification speed of liquid flow is often very slow due to the limit of solvent evaporation speed. In dry-wet spinning, the flow of liquid (fiber) being drawn enters the coagulating bath. And the solidification rate and fiber structure can be changed over a wide range by adjusting the composition and temperature of the coagulating bath.
Although dry jet wet spinning has the advantages of both dry spinning and wet spinning, the liquid flow tends to flow slowly along the spinneret surface. This phenomenon is related to the elastic viscosity of polymer solution, surface tension, the geometry of spinneret hole and the deformation speed of the liquid flow. Dry jet wet spinning has been used in the production of polyacrylonitrile fiber, aromatic polyamide fiber, polybenzimidazole fiber, etc.
Principle and process
Principle of wet spinning
By dissolving some special polymers, the solution with certain composition, certain viscosity and good spinnability was obtained. Then dissolve the fiber-forming polymer in appropriate solvent, which is called spinning solution. Spinning solution can also be obtained directly from homogeneous solution polymerization. The polymer swelling occurs before dissolution, that is, the solvent penetrates into the polymer first, increasing the distance between macromolecules, and then dissolves to form a uniform solution.
The whole process takes a long time, and the swelling speed has an important effect on the dissolution rate. Before spinning, the polymer solution must be prepared by mixing, filtering and deaeration. So as to make the properties of the spinning solution uniform, remove the embedded gel blocks and impurities, and remove the bubbles in the solution. In the production of viscose fiber, the preparation before spinning also includes the mature process, so that viscose has the necessary spinnability.
Wet spinning process
The spinning solution is sent to the wet spinning machine by a circulating pipe, measured by a metering pump. And then it enters the spinneret through a candle-shaped filter and connecting pipe. Spinnerets are generally made of an alloy of gold and platinum or tantalum. Several holes are regularly distributed in the spinneret, and the aperture is 0.05 ~ 0.08 mm.
The trickle flow of raw liquid pressed out from the spinneret hole enters the coagulation bath, the solvent in the trickle flow of raw liquid diffuses into the coagulation bath, and the coagulant penetrates into the thin stream. So that the trickle flow of raw liquid reaches a critical concentration, and precipitates in the coagulation bath to form fibers . Diffusion and coagulation in wet spinning are physical and chemical processes, but some chemical fibers also undergo chemical changes during the process. For example, viscose fiber, sodium cellulose xanthate is decomposed into cellulose regenerated fiber.
Alginate fiber
Alginate fiber is a special fiber obtained by wet spinning. The application range of alginate fiber is extremely wide. It has outstanding biocompatibility, breathable hygroscopicity, antibacterial and skin-friendly properties. At present, people take sanitary napkins, facial masks, nursing products, underwear and clothing, medical dressings, flame retardant wallpaper and fireproof equipment as key target markets. It fully embodies the excellent characteristics of antibacterial and skin-friendly, nourishing and healing, and natural flame retardant.
Alginate fiber has been researched in China since the 1990s. The production and experimental equipment are limited to laboratories, and the amount of social application is also small. It is only used for medical dressings. After 2000, with people’s search for green and environmentally friendly materials, alginate fiber, as a new type of biodegradable regenerated fiber, has good biocompatibility, degradable absorbability and other functions, and is rich in resources. The application of alginate fiber is gradually widespread. And people want to develop new varieties not only for medical use, but also in daily life. Such as: beauty and skin care products, feminine hygiene products, baby hygiene products, textile and clothing.
With the increase of people’s demand for alginate fiber, wet spinning machine is gradually enlarged from 5L, 50L, 200L, 500L, 1000L, and the output is from dozens of kilograms a year to hundreds of tons a year.
Wet spinning machine
Hefei Fanyuan Instrument Co., Ltd. have accumulated many years of equipment manufacturing experience in wet spinning. And we have provided and developed hundreds of production lines and experimental education lines for domestic and foreign universities, research institutes, and production plants.

With the increase of industrial output, it is obvious that the original small scale dissolution method and deaeration method cannot satisfy the large scale production. Our company always changes part of the processing equipment every time, with different methods for dissolution, with different methods for deaeration. These two steps in the whole spinning production line is important. Fortunately, we made breakthroughs every time. The dissolution time was shortened from 3-5 hours to about 30 minutes. And the deaeration time was shortened from 24 hours or longer to about 20 minutes. Which reduced the equipment investment and operation cost.
Our factory has been producing alginate spinning fiber equipment for many domestic and foreign enterprises. Start with small experimental equipment and continuously improve and test the wet spinning machine. So that we have mature experience in designing and manufacturing 100 tons, 200 tons and 400 tons per year now. Equipment production capacity and process characteristics can be customized according to customer needs.
Our company specializes in producing various wet spinning machine. Such as polymerization kettle, dissolving kettle, spinning machine, condenser, reaction kettle, electric heater and other fiber chemical equipment. In recent years, our company has continuously introduced and absorbed the advanced experience of the same industry, invested in the development of new products. In addition, We have a complete set of testing methods. Which can be designed and manufactured directly according to the requirements of users. Customers are welcome to consult related matters.
Our products include chitin fiber spinning machine, modacrylic fiber spinning machine, alginate fiber spinning machine, viscose fiber machine, hollow fiber equipment, and dry spinning machine. The process includes raw material dissolution- filtration – deaeration – metering pump – spinning – coagulation – stretching – stretching – washing – drying – oiling – heat treatment – winding. Our company is a one-step manufacturing plant for chemical equipment and spinning machine.
FAQS
Q1: How to choose between wet spinning and dry-jet wet spinning?
A: Determined by the characteristics of the raw materials:
It is recommended to use the standard wet spinning process for conventional fiber production
Dry-jet wet spinning is preferred for high-performance fibers
Q2: What are the key points of daily maintenance of the spinning machine?
A: Focus on:
Cleaning the spinneret weekly
Checking the accuracy of the metering pump monthly
Performing laboratory instrument calibration services every quarter
Q3: How to clean the spinneret head?
A: If your material is water-soluble, please use the water(same temperature with dissolution the material) to flush the spinneret, and then blow the spinneret with compressed air.
Q4: What is the total fibre weight produced in the machine per hour?
A: This is a lab machine, not for production use, i think few hundreds grams of fiber per hour. lab machine is only for process technology
Comments are closed.
Just saying thanks wouldn’t just be enough, for the fantastic fluency in your writing.
Your work is very good and I appreciate you and hopping for some more informative posts. Thank you for sharing great information to us.
So parcel to happen over your astounding site. Your blog acquires me a phenomenal exchange of charming
More than just informative, this article captivated me with its engaging storytelling and unique insights.