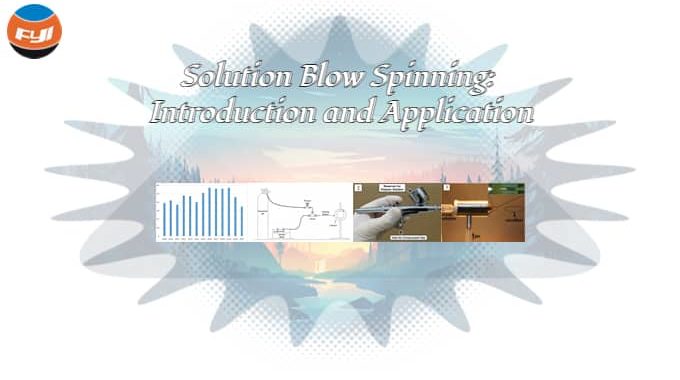
Solution Blow Spinning: Introduction and Application
Contents
Introduction
Nanofiber materials have the advantages of large specific surface area, high porosity, low density, good mechanical flexibility and so on, which show broad application prospects in many fields. There are various methods for preparing nanofiber materials, including electrospinning, solution blow spinning (SBS), the centrifugal spinning, the melt-blown Spinning, etc. SBS combines the advantages of electrospinning and melt-blown spinning, the process is simple and safe, spinning efficiency is high, suitable for a wider range of solution system, can choose more diverse raw materials, can control the structure and diameter of nanofibers. Since its development in 2009, SBS has received extensive attention from many fields and has become an efficient and versatile method for fabricating nanofiber materials with controllable microstructure and morphology.
In recent years, the number of papers on the topic of SBS has remained high (see Table 1). Tianjin Polytechnic University, Suzhou University, Beijing Institute of Fashion Technology, Jiangnan University, Donghua University, Dalian Polytechnic University and other universities are committed to using SBS to spinning nanofibers, so as to study the practicality of nanomaterials in various fields.The research enthusiasm of universities on SBS shows that blow spinning technology has great potential in the preparation of nanomaterials. With the deepening of research, spinning technology is becoming increasingly mature.This paper introduces the basic principle of solution blow spinning and its applicable raw materials, focusing on the influence of process parameters on solution blow spinning, and expounds the practical application of solution blow spinning nanofibers.
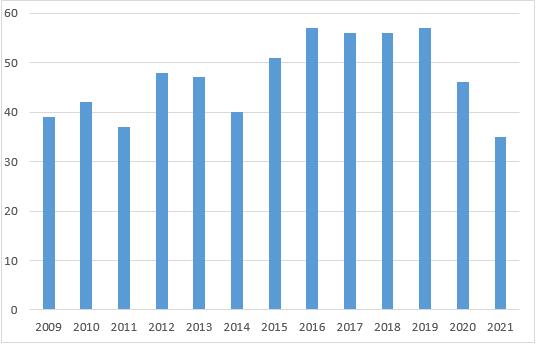
Solution blow spinning process
Blown spinning classification
Blown spinning is divided into solution method and melt method.
The solution method is to dissolve the polymer in volatile solvent to make spinning solution, spinning out of the spinneret hole at the same time by the high speed hot gas around the spray, so that the solution stream is stretched, and the solvent evaporation and curing, trapping on the net to form short fibers or non-woven fabric or collection of long filament bundles. This spinning method is called Solution blow spinning (SBS).
Melt method is used to melt polymer slices with spinning screw extruder and quantitatively extrude them. When melt is extruded out of the spinnblow hole, it is sprayed by the surrounding high-speed thermal flow and made into fibers, also known as melt-blown Spinning.
Principle of solution blow spinning
Medeiros et al. [1] first proposed the technology of preparing nanofibers by solution blow spinning, which combined the characteristics of melt blowing technology and dry spinning technology. The basic principle of this technology is that the small flow of solution is subjected to ultra-fine stretching under the action of high-speed airflow, and at the same time the solvent is evaporated and solidified into nanofibers. The schematic diagram of the principle is shown in the picture[2-3].The core components of solution blow spinning equipment include injection pump, nozzle, compressed air, collector. During the spinning process, the spinning solution is transported to the spinneret hole of the spinneret head at a steady flow rate under the pressure of the syringe pump. At the same time, high pressure air flow around the blow hole to form stable ring, drive the solution trickle speeding stretching, uniform stability of solution formed trickle solution in the process of rapid evaporation of solvent and under the action of a housing complex aura are intertwined, curly eventually formed in the shade on this network structure stable, random three-dimensional crimp nanofiber felt.
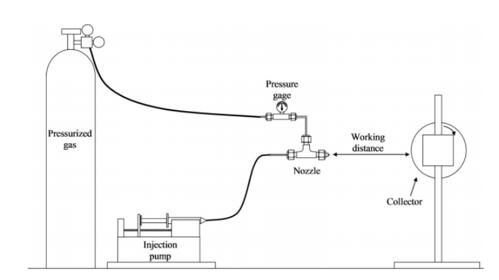
Process factors of solution blow spinning
1.Polymer solution: polymer solution viscosity, polymer solution advance rate
Li Lei et al. [4] used solution blow spinning to prepare alumina fiber, and found that the influence of polymer solution viscosity on fiber morphology and diameter was different from that in general cases. When the viscosity was too small, the fiber diameter was coarser, possibly because there was too much solvent and it did not evaporate completely when it reached the receiver.The nanofiber is compact and its properties are improved. When Kasiri et al. [5] used low concentration (8%) polystyrene polymer solution for blow spinning, the blow was unstable and beaded microstructures were formed on the collector. As the concentration reached 10%, the viscosity of the solution increased, and the fiber was smoother and larger in diameter. The research results of Rotta et al. [6] showed that the average diameter of fibers increased with the acceleration of injection speed.
2.Nozzle design
Han [7], such as through the orthogonal experiment and numerical simulation study has found that nozzle diameter, the diameter of the needle, needle extended length to gradually reduce the influence of linear velocity, flow center to nozzle diameter of 4 mm needle, needle diameter is 0.8 mm, protruding length of 5 mm was for the best geometric parameters, the preparation of the nanometer fiber surface is smooth, uniform morphology.
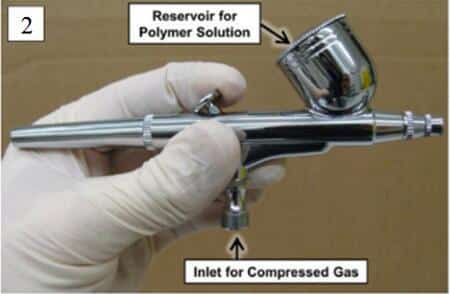
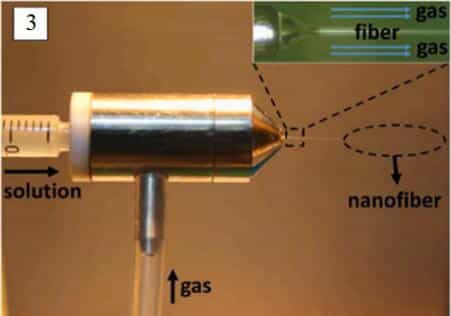
3.The air flow field
Kasiri et al. [5] observed the fiber morphology of solution blow-spun polystyrene material (PS) under high-speed air flow with different air pressures, and found that the average diameter and diameter distribution of the prepared fibers increased slightly when the air pressure increased at a lower value. When the air pressure was higher, the optimal fiber orientation was narrower and more fibers could be collected by the collector.
4.Receiving distance
Studies have shown that the solvent evaporation rate in the process of solution blow spinning will affect the final morphological characteristics of the fibers, and the distance between the nozzle and the receiver will affect the solvent evaporation rate, which largely determines whether the fibers will eventually form films or intertwine with each other [10].
Solution blow spinning raw materials
Many materials can be used to produce nanofiber materials by SBS technology. Polymers are the most commonly used materials for fabricating fibers via SBS. SBS has no special requirement on the dielectric constant of the spinning solution, so it is suitable for a wider range of spinning [11].
In the laboratory of Jia Chao et al. [11], they used SBS to study the spinnability of many polymer materials, polyacrylonitrile (PAN), polyvinylpyrrolidone (PVP), poly(methyl methacrylate)(PMMA), polyamide (PA), polylactic acid (PLA), polyimide (PI), poly(ethylene oxide) (PEO), poly(imide dioxime) (PIDO), SiO2 fibers, TiO2 fibers, ZrO2 fibers, BaTiO3 fibers, SnO2 fibers, SiO2− Al2O3 composite fibers,ZrO2−Al2O3 composite fibers, YSZ fibers, carbon fibers, metal fibers, polymer-based composite fibers,PAN-based carbon fibers,AgNF fibers,PLA-SiO2 composite fibers, PLA-TiO2 composite fibers, PLA-CeO2 composite fibers.
In addition to synthetic polymers, natural polymers, such as cellulose, zein, and gelatin, have also been successfully blown and spun into fibrous materials. For some non-spinnable natural polymers, mixing them with spinnable synthetic polymers is an effective strategy to obtain spinnable SBS solutions.
Glebert et al. [12] studied synthetic polymers and composites,including Poly (acrylonitrile), Poly (vinylidene fluoride), Poly (vinylpyrrolidone), Poly (methyl methacrylate), Poly (vinyl chloride),Sulfonated poly (ether ether ketone) and Sulfonated poly (ether sulfone), Polyimide, Poly (lactic acid), Poly (lactic acid-co-glycolic acid), Poly (ethylene oxide), Cellulose, Lignin, Nylon, Polyurethane, Poly (vinyl acetate), Poly (vinyl alcohol), and Poly(ethyl-co-vinyl acetate), Poly (styrene), Poly (caprolactone).
Application of solution blow spinning nanofibers
Thermal insulation material
Lightweight thermal insulation materials with low thermal conductivity are urgently needed in aerospace, thermal power, battery thermal protection and other fields. Ceramic fibrous spongy materials are ideal for thermal insulation because of their low density and thermal conductivity. However, producing such insulation materials efficiently and cheaply remains a challenge [11].
Biomedical
Nanofibers have unique application advantages in biomedicine, and related products have entered the market. As a new nanofiber processing technology, solution blow spinning can directly deposit the fiber on the specified target, even on the surface of biological tissues, which further expands the application of nanofibers in the biomedical field [13].
Flexible Electronic Devices
Metal materials have good electrical conductivity, but bulk metals have poor flexibility and are difficult to be used in flexible electronic devices. Processing metals into fibers significantly increases their flexibility while retaining their inherent electrical conductivity. Metal fibers have excellent flexibility and electrical conductivity, which can meet the application requirements of flexible electronic devices [11].
Environmental protection
The nanomaterials prepared by SBS technology can be used for air filtration and pollutant adsorption. KHALID et al. [14] coated the window screen with nanofibers on a large scale to protect the room from suspended matter pollution, and prepared a transparent air filter with light transmittance of more than 80%, and the efficiency level of PM2.5 removal could reach more than 99%. KOLBASOV et al. [15] successfully prepared PA6-based nanofiber membrane containing bio-based polymer by solution blow spinning method (bio-based polymer was made of lignin, oats, chitosan, sodium alginate and soybean protein as raw materials), and studied the adsorption effect of this membrane on heavy metal pollutant lead (Pb).
Solution blow spinning machine
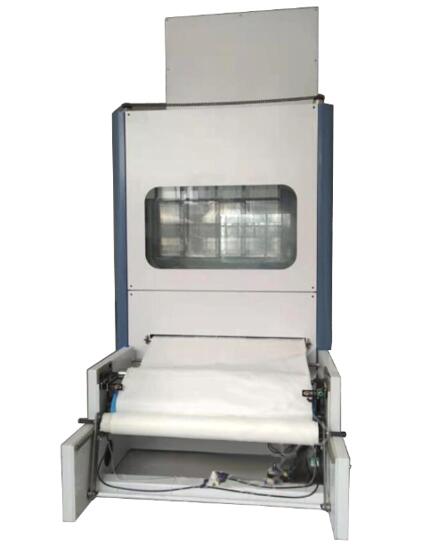
Range of application
SBS1000 spray spinning machine is a teaching spinning machine, using gas cylinders, intermittent, 4~12 holes. SBS2000 blow spinning machine adopts compressor gas supply, continuous type, cloth width of 300~600mm, mainly used in textile and related materials in the field of nano manufacturing, can be used to prepare nano fiber.
Technical feature
- Micronanofibers were prepared by ultrafine stretching of spinning solution and volatilization of solvent by high-speed air flow, which has higher spinning efficiency than electrospinning.
- Spinning solution thin flow is three-dimensional curled and entangled by the turbulent shear action of high-speed airflow field inside the spinning box. The process is short, the process is simple, the conditions are easy to control, and it can be large-scale production.
- The average diameter of nanofibers of the prepared nonwovens ranges from 0.01-3μm, which is smaller than that of conventional polypropylene melt-blown nonwovens, and has excellent performance.
Taking unlimited polymer solution as the processing object, it can overcome the requirements of the existing melt blowout technology on the thermoplasticity and high melt fluidity of raw materials, and has universal applicability.
Technical specification
Model | Compatibility | Sample size(mm2) | Nozzle number |
L1.0 | Standalone, lab scale | 300*400 | 1-6 |
M1.0 | Benchtop, lab scale | 300*400 | 1-6 |
P10 | Pilot scale | 300*cont 600*cont | 1-32 |
Number of spinneret capillary tubes | 80~140 |
Angle between the spinneret capillary and the horizontal plane | 45° |
Temperature of dissolution kettle | 40℃ |
High pressure air flow temperature | 45℃ |
Spinning speed | 207ml/h(15% PAN was dissolved in N, N-dimethyl acetamide) 267 ml/h(20% PAN was dissolved in N, N-dimethyl acetamide) |
Traction wind pressure | 2.6~3.0MPa |
Suction air pressure | 4kpa |
References
- Medeiros E S,Glenn G M,Klamczynski A P,et al.Solu-tion blow spinning: a new method to produce micro- andnanofibers from polymer solutions [J].Journal of AppliedPolymer Science,2009,113(4):2322-2330.
- ZHUANG Xupin , YANG Xiaocan ,SHI Lei , et al.Solution blowing of submicron-scale cellulose fibers [J].Carbohydrate Polymers ,2012 ,90( 2): 982 – 987.
- JIA Kaifei,ZHUANG Xupin ,CHENG Bowen , et al.Solution blown alignedcarbon nanofiber yarn assupercapacitor electrode [J ]. Journal of MaterialsScience: Materials in Electronics , 2013 , 24 ( 12):4769-4773.
- 李磊,康卫民,程博闻﹐等.新型溶液喷射法制备氧化铝纤维及性能研究[.J门.功能材料,2014,45 ( 13): 13082-13086.
- Kasiri A,Dominguez J E,Gonzalez-Benito J. Morphologyoptimization of solution blow spun polystyrene to obtainsuperhydrophobic materials with high ability of oil ab-sorption[J. Polymer Testing,2020,91:106859.
- Rotta M,Motta M,Pessoa A L,et al.Solution blowspinning control of morphology and production rate ofcomplex superconducting YBag CusOr-. nanowires[J].Journal of Materials Science:Materials in Electronics,2019,3o(9):9045-9050.
- Han W,Xie s,Sun X,et al.Optimization of airflow fieldvia solution blowing for chitosan/ peo nanofiber formation[J.Fibers and Polymers,2017,18(8):1554-1560.
- TUTAK W,SARKAR S,LIN-GIBSON s,et al. The supportof bone marrow stromal cell differentiation by airbrushed nanofiberscaffolds[J. Biomaterials,2013,34 (10) : 2389-2398.
- WANG HL,LIAO S Y,BAIYP,et al. Highly flexible indiumtin oxide nanofiber transparent electrodes by blow spinning[J].ACS Applied Materials & Interfaces,2016,8 (48) : 32661一32666.
- 胡艳丽, 何诗琪, 李凤艳,等. 溶液喷射纺纳米纤维的工艺研究及应用进展[J]. 功能材料, 2022(053-001).
- Jia C , Li L , Song J , et al. Mass Production of Ultrafine Fibers by a Versatile Solution Blow Spinning Method[J]. 材料研究述评(英文), 2021(002-006).
- Gcd A , Ak B , Ldt C , et al. Solution blow spinning (SBS) and SBS-spun nanofibers: Materials, methods, and applications[J]. 2020.
- 桂早霞, 刘茜. 溶液喷射纺丝技术的基本原理及其纤维应用[J]. 纺织导报, 2021(000-006).
- KHALID B,BAI X P,WEI H H,et al. Direct blow-spinningof nanofibers on a window screen for highly efficient PM2.sremoval[J]. Nano Letters,2017,17 (2) : 1140-1148.
- KOLBASOV A,SINHA-RAY S,YARIN A L,et al. Heavymetal adsorption on solution-blown biopolymer nanofibermembranes[J]. Journal of Membrane Science,2017,530:250-263.
Leave a Reply
You must be logged in to post a comment.
I wish more writers of this sort of substance would take the time like you did to explore and compose so well.
Greetings! Very helpful advice on this article! It is the little changes that make the biggest changes. Thanks a lot for sharing!
I feel really happy to have seen your webpage and look forward to so many more entertaining times reading here.
I truly appreciate this fantastic content you’ve written for us. I am confident that the majority of people would benefit from this.
You post very good writings. Your blog is fantastic. Continue to share.
Your posts are always thought-provoking and insightful.
One aspect that stands out in this blog is the writer’s ability to present complex ideas in an accessible manner.