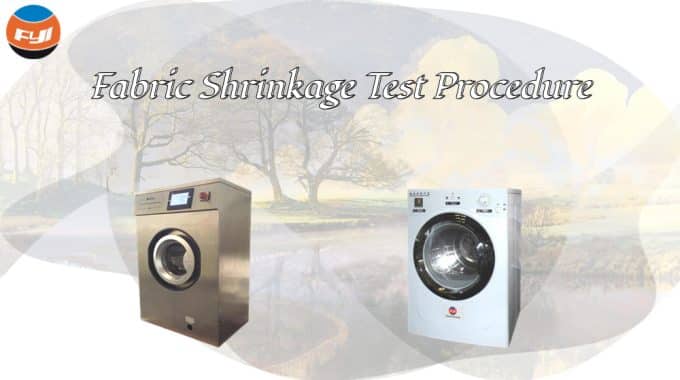
Fabric Shrinkage Test Procedure
Fabric dimensional stability refers to the shortening or elongation of fabric length during wearing, washing, storage, etc. Among them, shrinkage is one of the most concerning phenomena. The shrinkage of the fabric not only affects the appearance of the fabric, but may also cause a decrease in performance. Only in this way can it be possible to sew clothes that fit well and are not deformed.
Contents
Definition
Shrinkage is a phenomenon in which the length or width of textiles changes after washing, dehydration, drying and other processes in a certain state. The shrinkage of fabric refers to the percentage of fabric shrinkage after washing or soaking in water.
The smallest shrinkage rate is for synthetic fibers and blended fabrics, followed by woolen fabrics, linen fabrics, and cotton fabrics in the middle. Silk fabrics have a greater shrinkage, and the largest shrinkage rates are viscose fiber, artificial cotton, and artificial wool fabrics.
Fabric shrinkage test process (depends on ISO 5077)
Principle
The specimens are conditioned and sized in a specified standard atmosphere before undergoing appropriate washing and drying procedures. After the drying process, rehumidify and measure the dimensions again to calculate the dimensional changes.
Equipment and reagents
Fabric shrinkage tester: Washing shrinkage tester is used for accelerated washing equipment of knitted and woven fabrics. It evaluates the shrinkage rate according to international test methods. It also has 5 washing modes unique to Nike and Adidas brands. The MCU program controller has built-in ten sets of washing programs required by ISO, as well as operator program capabilities; the non-contact capacitive water level meter measures the water level accurately and reliably.
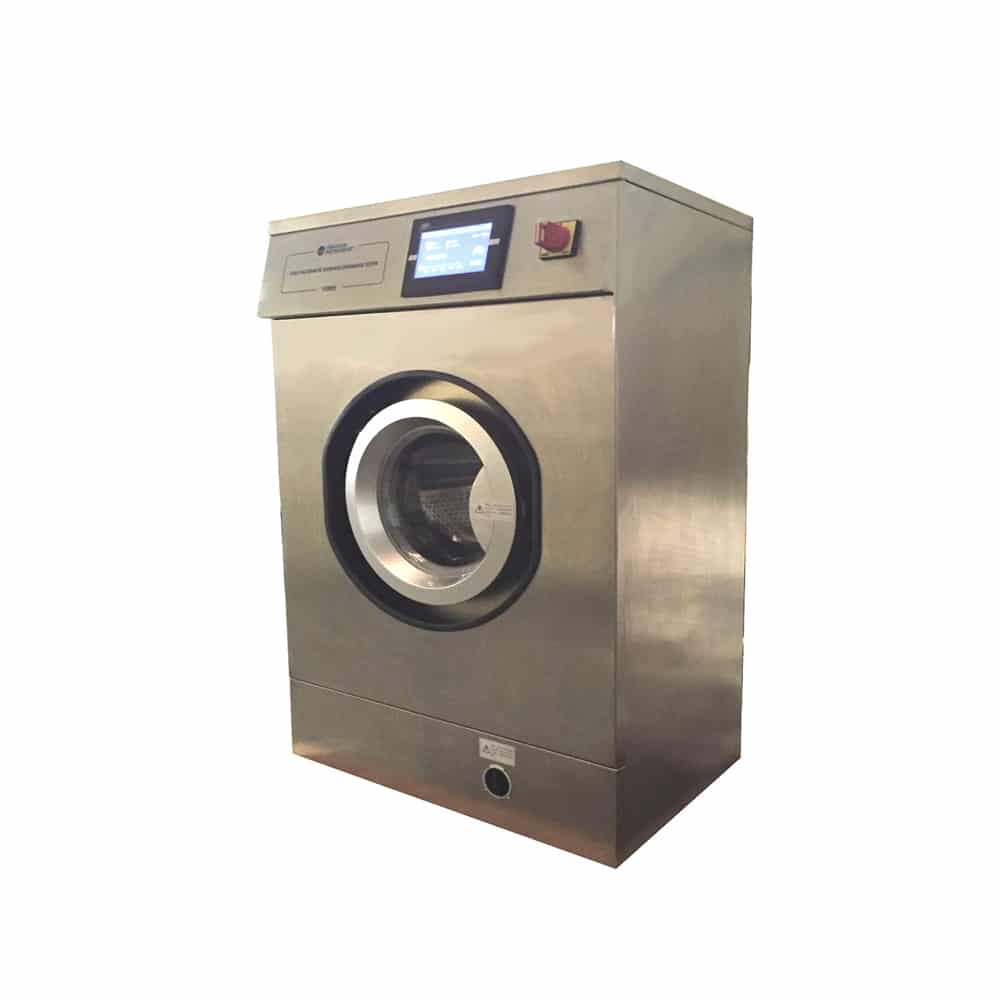
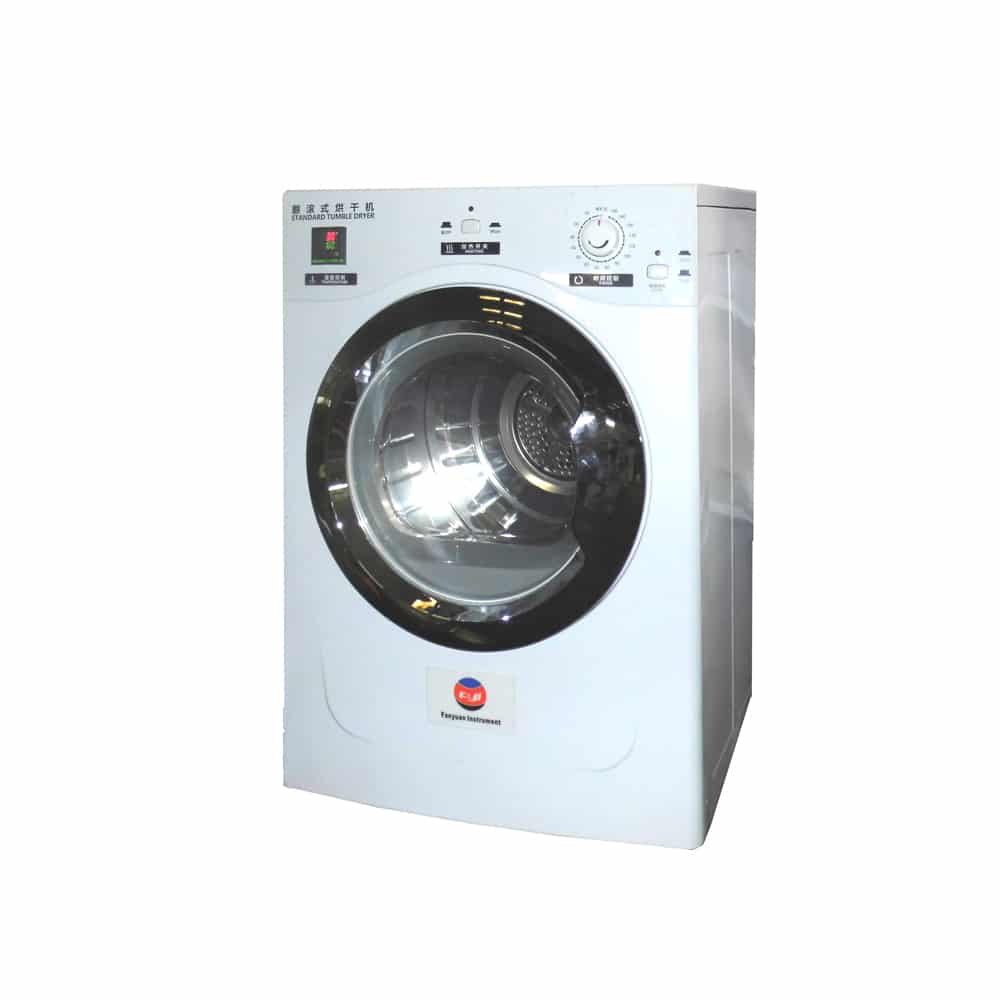
Precision Tumble Dryer: It is used to drying after washing. And then to check the fabric quality. A standard domestic tumble dryer recommended by many fabric specifiers ,120 minute timer, 5kg load, reversing action, 2 heat settings and 10 minute cooling time. Precision Tumble Dryer with Digital Controller, A standard domestic tumble dryer which has been modified with the addition of an accurate electronic controller to control exhaust temperature to +/-1 degree C and cycle time within one second. Capacity 5kg, reversing action, 10 minute cooling time.
Detergents: Detergents based on ISO 6330.
Measuring platform: A flat measuring platform large enough to accommodate the entire specimen.
Measuring tape or steel tape or fiberglass tape: scaled in mm, should be longer than the longest dimension measured.
Tools that can accurately mark reference points, such as:
a) Colorfast ink, if necessary, use a template with measuring grid;
b) It can produce thin threads of contrasting colors and sew them into the fabric for marking;
c) Hot wire, used to make small holes and mark thermoplastic materials;
d) Staples, (applicable to specimens that are not stirred during testing, such as soaked in water).
Humidification environment
Follow the atmospheric conditions for humidity control and experiments specified in ISO 139. The standard atmosphere should be a temperature of 20.0°C and a relative humidity of 65.0%.
Sample
Sampling: Cut samples. The size of each sample should be at least 500 mm × 500 mm. Each side should be parallel to the length and width of the fabric. If the fabric width is less than 650 mm, full-width samples can be used for testing after negotiation between both parties.
Humidity control: place the sample in a humidity-controlled environment for at least 4 hours or until a constant weight is reached. Note: When the weight is weighed at intervals of 1 hour and the change in mass is no more than 0.25%, it is considered that constant weight has been achieved.
Marking: Place the sample on the measuring table and make at least three pairs of marks in the length and width directions of the sample. The distance between each pair of marks should be at least 350 mm, the distance between the marks should be no less than 50 mm from the edge of the specimen, and the marks should be evenly distributed on the specimen (see the figure below).
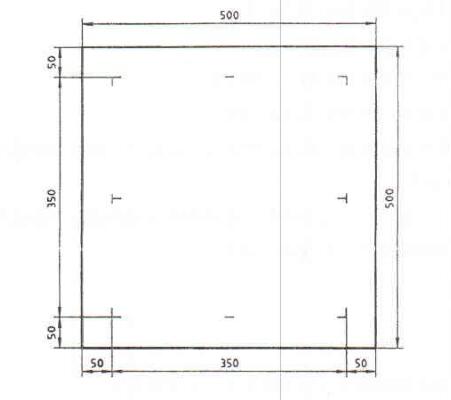
Measurement method: Place the sample flat on a flat measuring table and gently smooth out wrinkles to avoid distorting the sample. Place the measuring tape on the sample to measure the distance between the two marked points and record to the nearest 1 mm.
Procedure
- After conditioning and measuring the sample, determine the original length and width of the sample.
- Wash and dry the specimen according to one of the procedures specified in ISO 6330.
- After washing and drying, adjust the humidity of the sample according to the procedures specified in ISO 3759, measure the size and calculate its dimensional change rate.
Expression of results
Calculate the percentage change in size according to the following formula:
(Xt-X0)/X0*100%
In the formula: X0 is the initial size, mm;
Xt is the size after processing, mm.
Record the percentage of dimensional change separately. Use the “+” sign to indicate elongation and the “-” sign to indicate contraction.
Experiment report
The test report should include the following:
a) Explain that the preparation, marking and measurement of the specimen were carried out in accordance with this standard, and list other additional measurement items made;
b) The washing and drying procedures used, pressing or other finishing methods used;
c) The number of specimens;
d) For fabric samples, report the average dimensional change rate in the length direction (warp or longitudinal direction) and the average dimensional change rate in the width direction (weft direction or transverse direction).
Factors causing fabric shrinkage
- Different raw materials of fabrics have different shrinkage rates. Generally speaking, for fibers with high hygroscopicity, the fiber expands, the diameter increases, the length shortens, and the shrinkage rate is large after being immersed in water. For example, the water absorption rate of some viscose fibers is as high as 13%, while synthetic fiber fabrics have poor hygroscopicity and their shrinkage rate is small.
- Different fabric densities have different shrinkage rates. If the longitudinal and latitudinal densities are similar, the longitudinal and latitudinal shrinkage rates are also similar. Fabrics with a high warp density will have a large shrinkage in the warp direction; conversely, fabrics with a weft density greater than the warp density will have a large shrinkage in the weft direction.
- Fabrics with different yarn counts have different shrinkage rates. Fabrics with a thicker yarn count will have a greater shrinkage rate, while fabrics with a finer yarn count will have a smaller shrinkage rate.
- Fabric production processes are different and shrinkage rates are also different. Generally speaking, during the weaving, dyeing and finishing process of fabrics, the fibers have to be stretched many times, and the processing time is long. The shrinkage of fabrics with greater tension will be greater, and vice versa.
Comments are closed.
A must-read for both experts and novices alike, this article caters to a wide range of readers.
A sincere appreciation for the author’s dedication to delivering accurate and reliable information shines through every word.
I’m impressed by how the author effortlessly guides the reader through complex concepts without overwhelming them.