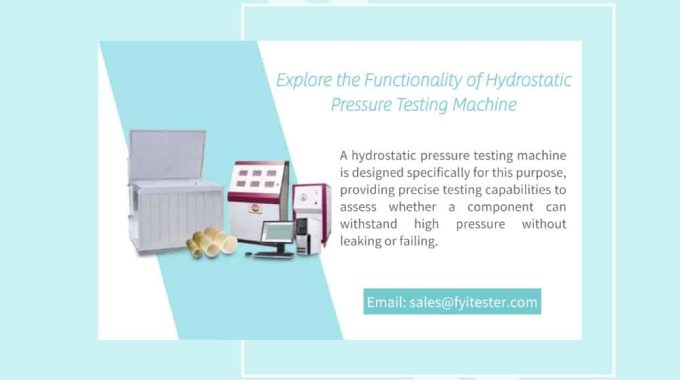
Explore the Functionality of Hydrostatic Pressure Testing Machine
Hydrostatic pressure testing is a critical process used in various industries, including manufacturing, construction, and plumbing, to ensure the integrity and safety of pressure vessels, pipelines, and tanks. A hydrostatic pressure testing machine is designed specifically for this purpose, providing precise testing capabilities to assess whether a component can withstand high pressure without leaking or failing. This article explores the functionality, features, and standards for hydrostatic pressure testing machines.
Contents
What is hydrostatic pressure testing?
Hydrostatic pressure testing involves filling a vessel or pipeline with a liquid, usually water, and then pressurizing it to a specified level above its normal operating pressure. This process helps identify any weak points or leaks that may not be visible under normal conditions. The test typically lasts for a set period, allowing for thorough inspection of the component’s integrity.
Functionality of hydrostatic pressure testing machines
Hydrostatic testing machines are essential tools used in a variety of industries to evaluate the integrity and safety of pressure vessels, piping, and other critical components. Their functionality revolves around several key processes to ensure these components can withstand the operating pressures without failure.
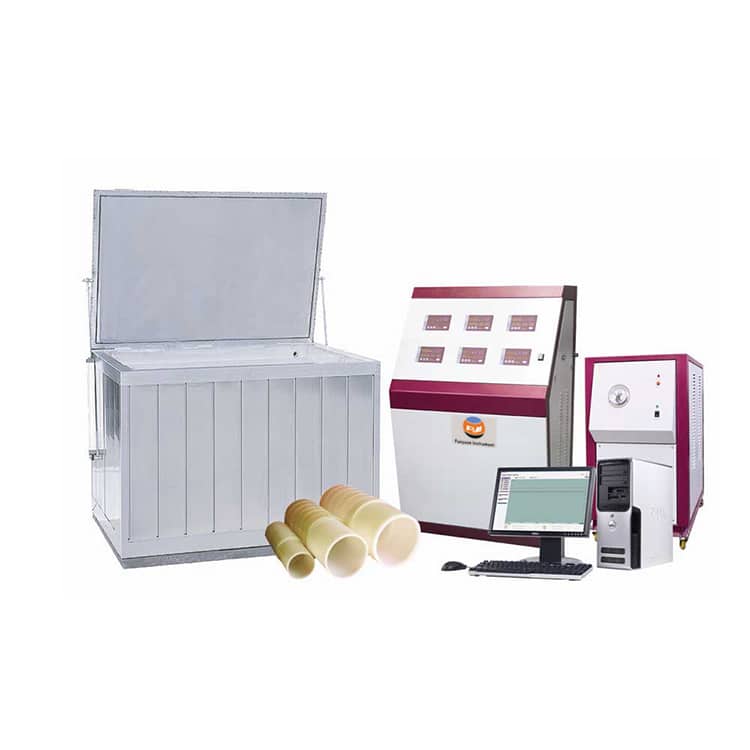
Filling specimen
The first step in the hydrostatic testing process is to fill the specimen with liquid, usually water. The machine ensures that the liquid fills every part of the assembly, creating a uniform environment for pressure testing.
Supercharge
Once the specimen is filled, the machine applies pressure to the liquid. This is done with a high-pressure pump, which generates pressures far in excess of the normal operating limits of the component. During this phase, the machine continuously monitors pressure levels to ensure they remain stable and within specified limits.
Monitoring and data collection
One of the standout features of modern hydrostatic testers is their real-time monitoring and data collection capabilities. Advanced models are equipped with sensors that can track a variety of parameters such as pressure, temperature, and even flow rate. This data is essential in assessing how the specimen will perform under pressure. The machines also include data logging capabilities that allow operators to record test results for future analysis and compliance reporting. This capability not only improves the accuracy of the test, but also provides valuable insights into the overall quality and reliability of the component being tested.
Post-test inspection
After the pressurization stage, the next step is to inspect the test specimen for leaks or structural failures. Depending on the machine and specific test requirements, this may involve visual inspection or more advanced techniques such as ultrasonic testing or dye penetrant methods. The machine can also help create a controlled environment for these inspections, ensuring that any potential failures are accurately detected. This inspection stage is critical because it directly informs the decision-making process regarding the safety and reliability of the component.
Pressure relief and safety mechanisms
Safety is paramount in hydrostatic testing, and the machine is equipped with several safety features to protect both the operator and the equipment itself. These include a pressure relief valve, which automatically releases excess pressure to prevent catastrophic failure, and an emergency shut-off system that can immediately stop the testing process in the event of an abnormal situation. Operators are trained to understand these safety mechanisms, ensuring they can react quickly in any situation.
Features of hydrostatic pressure testing machines
- Multi-purpose: it can be used for hydrostatic pressure test and burst test of pipes, and thermal stability test of thermoplastic pipes.
- Wide range of applicable pipe diameters: strong versatility,applicable to pipe diameters ranging from φ2 to φ1600.
- Wide range of pressure control: pressure control range can be from 0.2mpa to full scale.
- Fast pressure increase speed: less than 30min for pipe diameter 1600mm.
- Constant pressure and stability: can automatically determine pipe diameter and material characteristics, and automatically formulate pressure increase procedures and algorithms. Constant pressure and stability, high expansion rate, ensure 100% success of the experiment. Multi-level energy storage pressure control, stable pressure control, and can extend the service life of the solenoid valve.
- High test pressure accuracy: internationally renowned brand high-precision pressure transmitter is used to ensure high precision and high reliability of pressure test.
- Powerful functions: it has eight functions including leakage judgment, real-time monitoring of crack identification, power-off protection, power-off protection, automatic recovery, printing and storage of test results.
- Two-level monitoring: first half-hour monitoring or 24-hour monitoring; second-level comprehensive monitoring, constant temperature medium temperature monitoring.
- Use high-quality special solenoid valves, no clogging, maintenance-free; long life, more than 5 times the life of general solenoid valves.
- Automatic cleaning function of solenoid valves, easy maintenance of solenoid valves.
- With automatic release and pressure relief functions.
- The unit can be freely switched between MPa, Bar, PSI, in line with the operating habits of different countries.
- Pretreatment settings can be made, and the test will start automatically after the pretreatment is completed.
- The two time display modes of timing and countdown can be switched freely.
Standards
The hydrostatic pressure testing machine for pipes complies with various standards, as follows:
EN 921: Plastics piping systems — Thermoplastics pipes — Determination of resistance to internal pressure at constant temperature.
ISO 1167 : Thermoplastics pipes, fittings and assemblies for the conveyance of fluids —Determination of the resistance to internal pressure.
GB/T 6111: Thermoplastics piping systems for the conveyance of fluids — Determination of the resistance to internal pressure.
GB/T 15560: Standard test method for short-time hydraulic failure and resistance to constant internal pressure of the plastics pipes for the transport of fluids.
Conclusion
Hydrostatic pressure testing machines play a vital role in ensuring the safety and reliability of pressure vessels, pipelines, and other critical components. By understanding their functionality and benefits, businesses can make informed decisions when investing in this essential testing equipment. With proper selection and regular use, hydrostatic pressure testing machines help maintain high safety standards, reduce risks, and enhance overall operational efficiency. If you have further questions or need assistance in choosing the right machine, feel free to reach out!