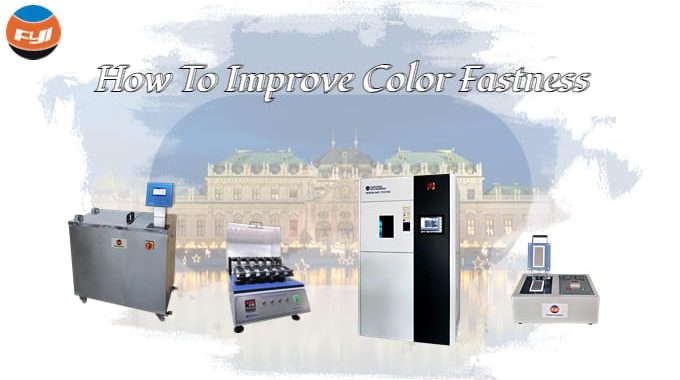
How to Improve Color Fastness
Last update: May 23, 2025
After dyeing, the fabric’s capacity to retain its original color can be represented by evaluating various color fastness. Washing fastness, rubbing fastness, light fastness, sublimation fastness, and other fabric indicators are commonly used for assessing color fastness.
The greater the fabric’s washing fastness, rubbing fastness, light fastness, and sublimation fastness, the better the dyeing fastness.
The key elements influencing the aforesaid fastness are two:
First is dye performance, and the second is dyeing and finishing procedure formulation.
The foundation for increasing color fastness is the selection of dyes with outstanding performance, and the formulation of a suitable dyeing and finishing process is the key to ensuring color fastness. Both are necessary and cannot be overlooked.
Contents
Washing fastness
Fabric washing fastness is divided into two categories: fading fastness and staining fastness. In general, the lower the fading fastness of a cloth, the lower its staining fastness.
The staining of the fiber may be determined when testing the staining fastness of a specific textile by measuring the staining of the fiber to the six regularly used textile fibers. Polyester, nylon, cotton, acetate, wool or silk, and acrylic are the six most regularly used textile fibers. A competent independent professional inspection business performs the staining fastness test on the six fibers, and such a test is pretty objective and fair.
For cellulose fiber products
The washing fastness of reactive dyes is greater than that of direct dyes for cellulose fiber goods. Insoluble azo dyes, vat dyes, and sulfur dyes have a more sophisticated dyeing procedure than reactive dyes and direct dyes. As a result, the washing fastness of the last three colors is superior.
To increase the washing fastness of cellulose fiber goods, it is therefore required not only to select the appropriate dye, but also to select the appropriate dying technique. Washing fastness may be considerably improved by appropriately strengthening water washing, color fixing, and soaping.
For polyester fabric
The washing fastness of the fabric after dying may match the customer’s requirements for the deep color of polyester fiber as long as it is fully restored and washed. Polyester textiles, on the other hand, are generally softened by using cationic silicone softeners to improve fabric feel. At the same time, when the polyester fabric is heated to a high temperature, the anionic dispersion in the disperse dye may distribute over the surface of the fiber due to thermal migration of the dye. As a result, after setting, the washing fastness of the polyester fabric with rich color and sheen may be unqualified. This requires not only the sublimation fastness of disperse dyes to be considered when selecting disperse dyes, but also the thermal migration resistance of disperse dyes.
There are several ways for determining the washing fastness. When assessing the washing fastness of textiles, different findings will be made based on different testing standards. When the client recommends special washing fastness indications, if specific testing standards can be offered, it will facilitate communication between the two sides. Although strengthening washing and post-treatment may enhance cloth washing fastness, it will also raise dyeing factory emission reduction.
Find some high-efficiency detergents, rationalize the dyeing and finishing process, and expand research on short-process procedures, all of which may not only enhance production efficiency but also contribute to energy conservation and emission reduction.
Rubbing fastness
The rubbing fastness of the fabric is the same as the washing fastness, and it also includes two aspects: One is dry rubbing fastness and the other is wet rubbing fastness.
Obtain the physical sample card of the fabric’s dry rubbing fastness and wet rubbing fastness using the fabric rubbing fastness tester, and compare the fabric color change sample card and the staining sample card to assess the dry rubbing fastness and wet rubbing fastness of the textile. It’s quite convenient.
When assessing the rubbing fastness of dark-colored fabrics, the grade of dry rubbing fastness is usually one grade higher than the grade of wet rubbing fastness.
As an example, consider straight coloring black cotton cloth. Although it has been thoroughly repaired, the dry and wet rubbing fastness are not very high, and it occasionally fails to fulfill client requirements. Reactive dyes, vat dyes, and insoluble azo dyes are commonly used for dyeing to increase rubbing fastness. Strengthening dye selection, color fixing treatment, and soaping are all excellent ways to increase textile rubbing fastness.
- Special additives that can improve the wet rubbing fastness of textiles can be selected to improve the wet rubbing fastness of deep-color cellulose fiber products, and the wet rubbing of the product can be significantly improved by padding the special additives when the finished product is finalized. fastness.
- When shaping dark-colored chemical fiber filament goods, the wet rubbing fastness of the product can be increased by adding a tiny quantity of fluorine-containing water repellant.
- When acid dyes are used to dye polyamide fiber in deep colors, the wet rubbing fastness of nylon fabric in deep colors may be significantly increased by utilizing a particular color fixing agent for nylon.
- When evaluating the wet rubbing fastness of sanded dark-colored items, the degree of wet rubbing fastness may be lowered because the short fibers on the surface of the sanded product will break off more plainly than other products.
Color fastness to light
Sunlight possesses wave-particle duality, and sunlight that carries energy in the form of photons has a substantial influence on the dye’s molecular structure. When photons disrupt the fundamental structure of the chromogenic component of the dye structure, the color of the light produced by the dye chromophore changes, generally becoming lighter until it is colorless. The more noticeable the dye’s color shift in sunlight circumstances, the poorer the dye’s light fastness.
Many approaches have been used by dye makers to increase the light fastness of their colors. Increasing the relative molecular weight of the dye, the possibility of internal complexation of the dye, and the coplanarity and length of the conjugated system of the dye can all help to increase the dye’s light fastness.
During the dyeing and finishing process, suitable metal ions are added to achieve grade 8 light fastness in phthalocyanine dyes. Forming a compound within the dye molecule can boost the dye’s vividness and light fastness greatly. Choosing colors with improved light fastness for textiles is the key to boosting the product’s light fastness level. The effect of modifying the dyeing and finishing processes on enhancing the light fastness of textiles is not clear.
Sublimation fastness
Because the dyeing mechanism of polyester fibers differs from that of other dyes, sublimation fastness may directly reflect the heat resistance of dispersion colors. For other dyes, assessing the ironing fastness of the dye is the same as checking the dye’s sublimation fastness. The dye’s sublimation fastness is poor. The dye in the solid state is easily detachable from the interior of the fiber in a gas state in the dry heat state. In this manner, dye sublimation fastness can also indirectly reflect fabric ironing fastness.
FAQs
Q1: How can I improve washing fastness in dark-colored cotton fabrics?
Use reactive or vat dyes, apply fixation agents, and optimize rinsing to reduce dye residue.
Q2: Why does wet rubbing fastness often underperform dry rubbing?
Water acts as a lubricant, increasing dye transfer. Solutions for improving wet rubbing fastness include using fluorinated water repellents or cationic fixatives.
Q3: What standards govern sublimation fastness testing?
ISO 105-P01 and AATCC 117 are widely used for evaluating sublimation fastness in synthetic fabrics.
Q4: Can dyeing processes reduce environmental impact?
Yes. Adopting short-process dyeing methods for enhanced color fastness minimizes water/energy use and chemical waste.
Comments are closed.
Pretty! This was an excellent post. Thank you for giving this information.
Thank you for such an informative post!