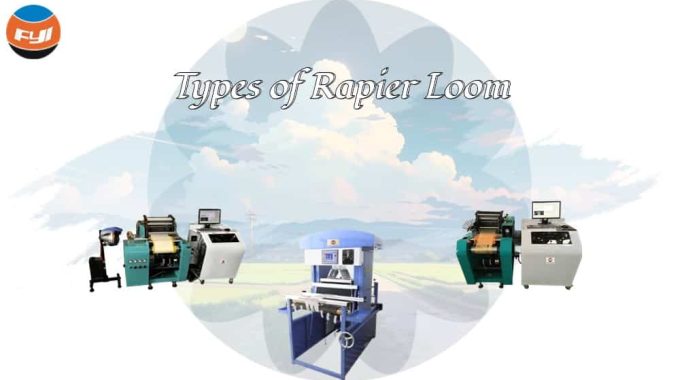
Types of Rapier Loom
Since shuttle looms have obvious problems such as low weft insertion rate and poor product quality, shuttleless looms are replacing shuttle looms, and shuttle looms will eventually be eliminated. According to different weft insertion methods, shuttleless looms include rapier looms, jet looms, air-jet looms, water-jet looms and projectile looms. Among shuttleless looms, the weft insertion principle of the rapier loom was first figured out. At first, it was a single rapier, and later a rapier loom with a double rapier for weft insertion was invented.
Since the 1950s, following the rigid rapier, flexible, steel belt, two-phase, telescopic, double-layer, three-layer and other forms of rapier looms have appeared and been put into industrial production. With good variety adaptability, it is widely used in yarn-dyed, terry, silk, linen, wool and other industries. It has now developed into a shuttleless loom with many models and large quantities. In recent years, rapier looms have been popular among textile enterprises for their flexibility, versatility, and wide variety adaptability. They account for a considerable proportion of shuttleless loom production. The technology is mature and the level is high.
Contents
Weft insertion principle of rapier loom
The weft insertion method of the rapier loom is to use a reciprocating rapier as a weft insertion device to insert or clamp the weft yarn, and introduce the weft yarn on the fixed bobbin outside the machine into the shed. There are many forms of weft insertion for rapier looms, which can be classified according to the following characteristics.
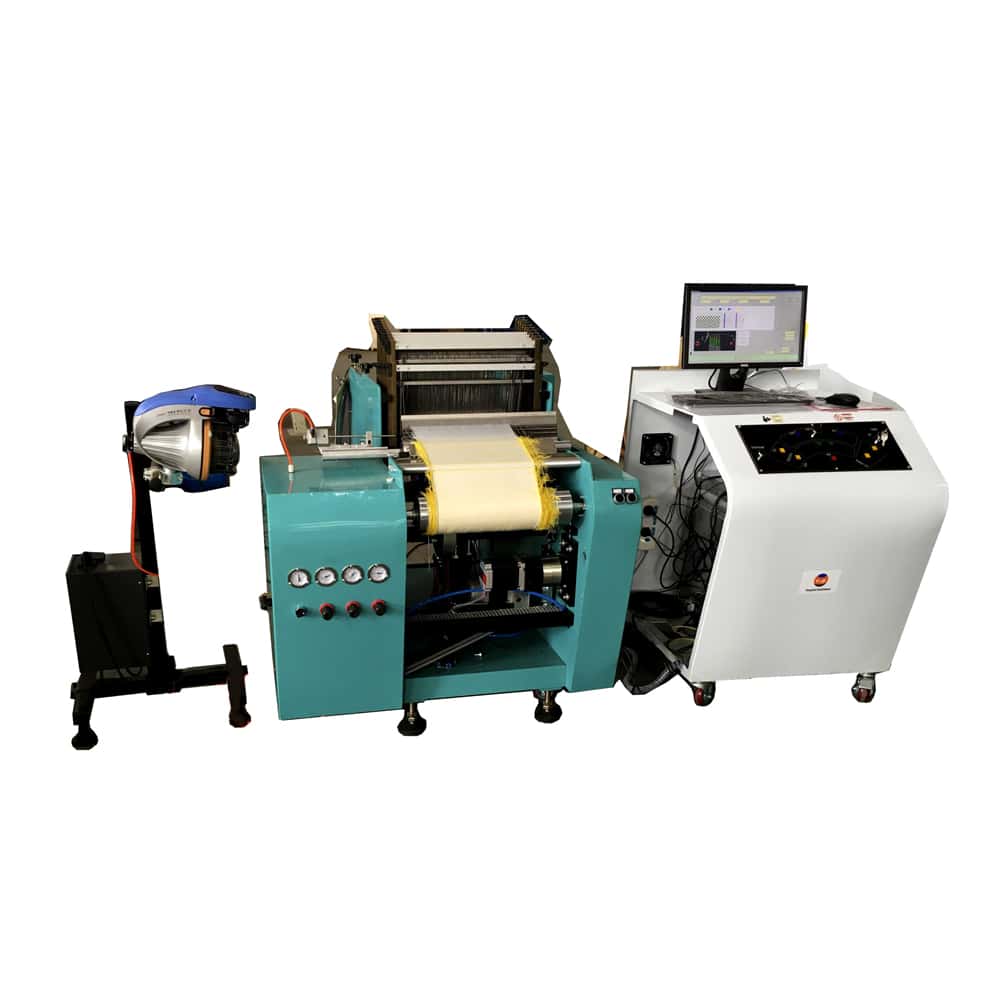
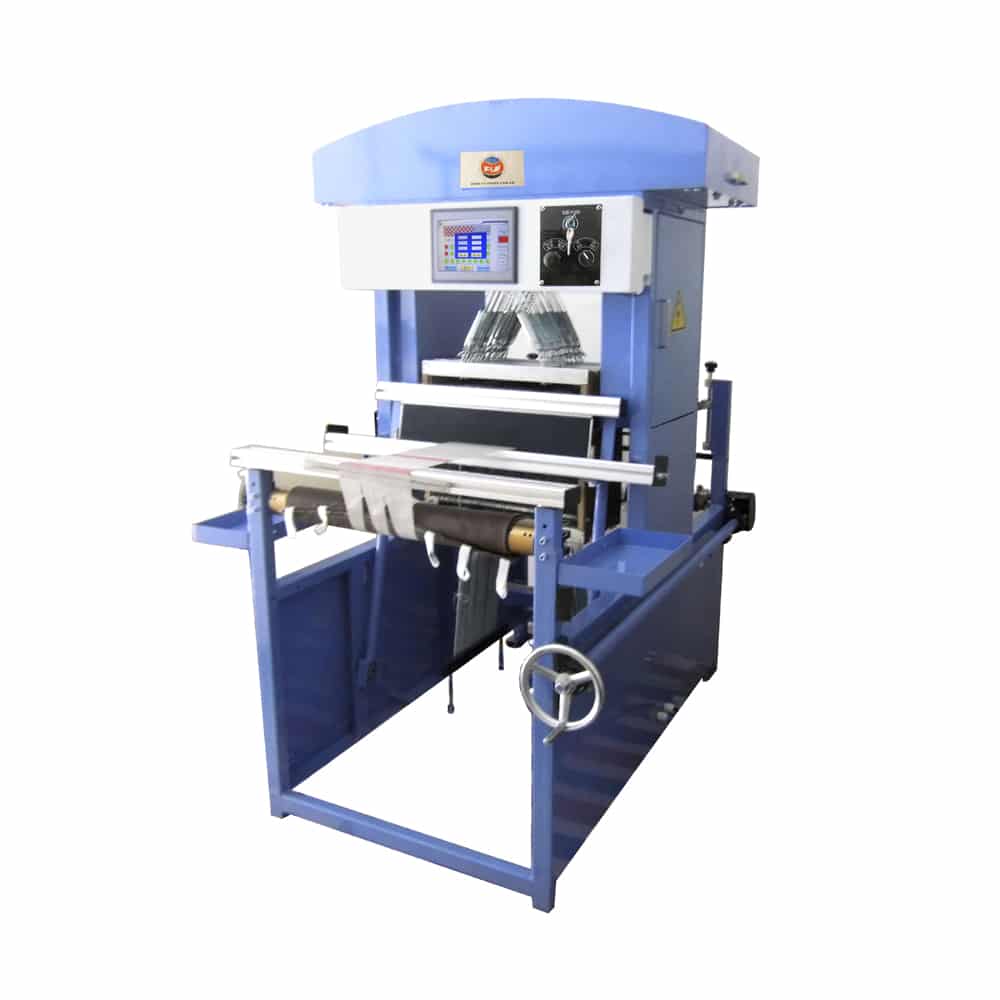

Rapier configuration quantity
Rapier looms are divided into single rapier weft insertion and double rapier weft insertion according to the number of rapier configurations.
Single rapier weft insertion is only equipped with a long rapier wider than the cloth width and its rapier transmission mechanism on one side of the loom, which sends the weft yarn into the shed to the other end. Or extend the empty rapier into the shed to hold the weft yarn on the opposite side, and then pull the weft yarn into the shed during the withdrawal process to complete the weft insertion.
Double-rapier weft insertion is equipped with rapiers (weft-feeding swords and weft-receiving swords) and corresponding sword-transmitting mechanisms on both sides of the loom. During weft insertion, the weft yarn is sent to the center of the shed by the weft-feeding sword, and then delivered to the opposite side to the weft-receiving sword that has also moved to the center of the shed. The two swords then return separately, and the weft joining sword pulls the weft yarn through the shed to complete the weft insertion.
The structural form of the rapier
Rapier weft insertion can be divided into rigid rapier weft insertion and flexible rapier weft insertion. Whether the rapier is rigid or flexible is usually used as the basis for classifying rapier looms.
The rapier head of the rigid rapier loom is mounted on a rigid and strong rapier, and the weft insertion is completed by the reciprocating motion of the rigid rapier. There is no need to install a device to guide the rapier in the shed. The rigid rapier occupies a large space after exiting the shed, making the machine occupy a large area. The rapier is bulky and has large inertia, which is not conducive to high speed.
The rapier head of the flexible rapier loom is mounted on a flat strip made of spring steel or composite materials. The stretching of the flexible rapier strip causes the rapier head to reciprocate to complete the weft insertion. After the flexible sword belt exits the shed, it can be wound around the sword transfer wheel or retracted under the frame. This kind of flexible rapier loom occupies a small area, has a light rapier belt, is conducive to high speed, and can achieve a large width.
Weft holding method for rapier weft insertion
It can be divided into two categories: one is the fork-type rapier system, and the other is the clamp-type rapier system.
In the fork-in rapier system, the weft yarn is hung on the rapier head of the single rapier and is pushed to the other end of the shed to achieve circular weft insertion, and double weft is introduced each time. The weft yarn can also be sent to the center of the loom by the weft-feeding sword, and then hooked by the sword head of the weft-receiving sword to lead it out of the shed.
Clamping rapier system, the weft feeding rapier holds the weft yarn and sends it to the center of the loom. Then the weft connecting sword takes over the weft yarn and leads out the shed to achieve linear weft insertion, each time introducing a single weft.
The location of the sword transfer mechanism
The rapier loom’s rapier transfer mechanism is either fixedly mounted on the frame or fixedly mounted on the reed holder. The former is called a separated reed holder because the weft insertion mechanism and the beat-up mechanism are separated, while the latter is called a non-separable reed holder. Reed seat.
On rapier looms with separate reed seats, the sword transfer mechanism does not swing back and forth with the reed seat, and the reed seat is driven by a conjugate cam. During weft insertion, the reed seat is stationary at the rear, and when the reed seat moves, the sword head cannot be within the swing range of the reed. Therefore, on rapier looms with separate reed seats, the remaining length of the reed is limited, and it should be shortened if it exceeds the limit. For rapier looms with separate reed seats, the reed seat remains stationary at the last position during weft insertion. Therefore, the required shed height is small, the beating stroke is also small, and the reed base is light, which is beneficial to increasing the speed of the machine.
On a rapier loom with a non-separable reed base, the rapier and its rapier transmission mechanism swing back and forth together with the reed base. At the same time, the rapier moves left and right relative to the reed base to complete weft insertion. It can use the ordinary crank-link beating mechanism, but the beating stroke is larger to match the movement of the rapier in the shed. And the shed height is required to be larger to avoid excessive squeezing of the rapier head with the warp when entering and exiting the shed. In addition, the moment of inertia of the reed seat is also large, which affects the further increase of the vehicle speed.
Leave a Reply
You must be logged in to post a comment.
I join the ranks of loyal readers who eagerly anticipate each new blog post.
See how the author seamlessly weaves personal anecdotes with factual evidence to support their arguments.