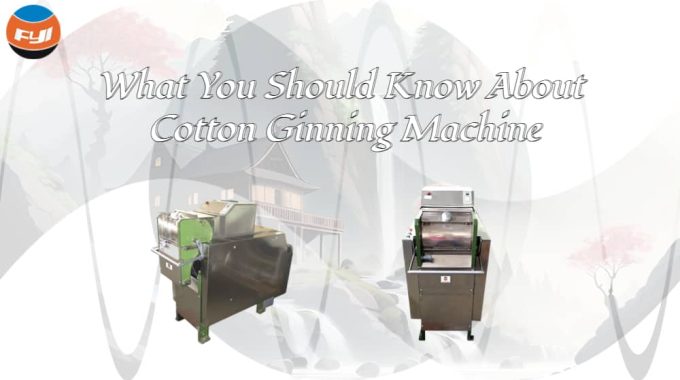
What You Should Know About Cotton Ginning Machine
A cotton ginning machine is used to process cotton, primarily to remove seeds and foreign matter, making cotton a raw material for the textile industry. It can greatly improve processing efficiency and product quality, and is one of the indispensable equipment in the modern textile industry.
Contents
Types of cotton ginning machine
Cotton ginning machine is also known as cotton gin, it can be divided into two types, one is the roller ginning machine and the other is the saw ginning machine.
Roller ginning machine
The contact traction between the roller and the cotton fiber is used to separate the fiber from the cottonseed.
Features
- Low speed, soft action, not easy to break the fiber.
- Fewer defects such as neps and wires.
- Raw cotton contains a lot of impurities.
- Lots of short fleece.
- It is suitable for processing long-staple cotton or seed cotton with poor maturity and reserved seed cotton, with an output of 40-50kg.
- The length of long-staple cotton is >33mm, and the fineness is 7000-8000 metric.
- Suitable for spinning fine yarns 3-7tex (80-200 counts).
- The appearance of the finished yarn is better, so the carding noil rate needs to be increased, otherwise the yarn strength and evenness will be affected.
Saw ginning machine
The fiber is pulled by the saw tooth hook to separate the fiber from the cottonseed.
Features
- High speed, strong effect, easy to cut fibers.
- It is easy to produce defects such as neps and wires.
- There is an impurity removal system, and the raw cotton contains less impurity.
- The short-lint rate is low, the uniformity is good, and the cotton is loose.
- It is suitable for processing fine and coarse cotton, with an output of 300-500kg.
- The fine cotton is 25-33mm long and 5000-6000 public counts.
- Suitable for spinning medium and fine yarns 9-28tex (21-60 counts).
- It is conducive to the improvement of yarn strength and evenness, but it will affect the appearance of yarn when there are many rolling defects.
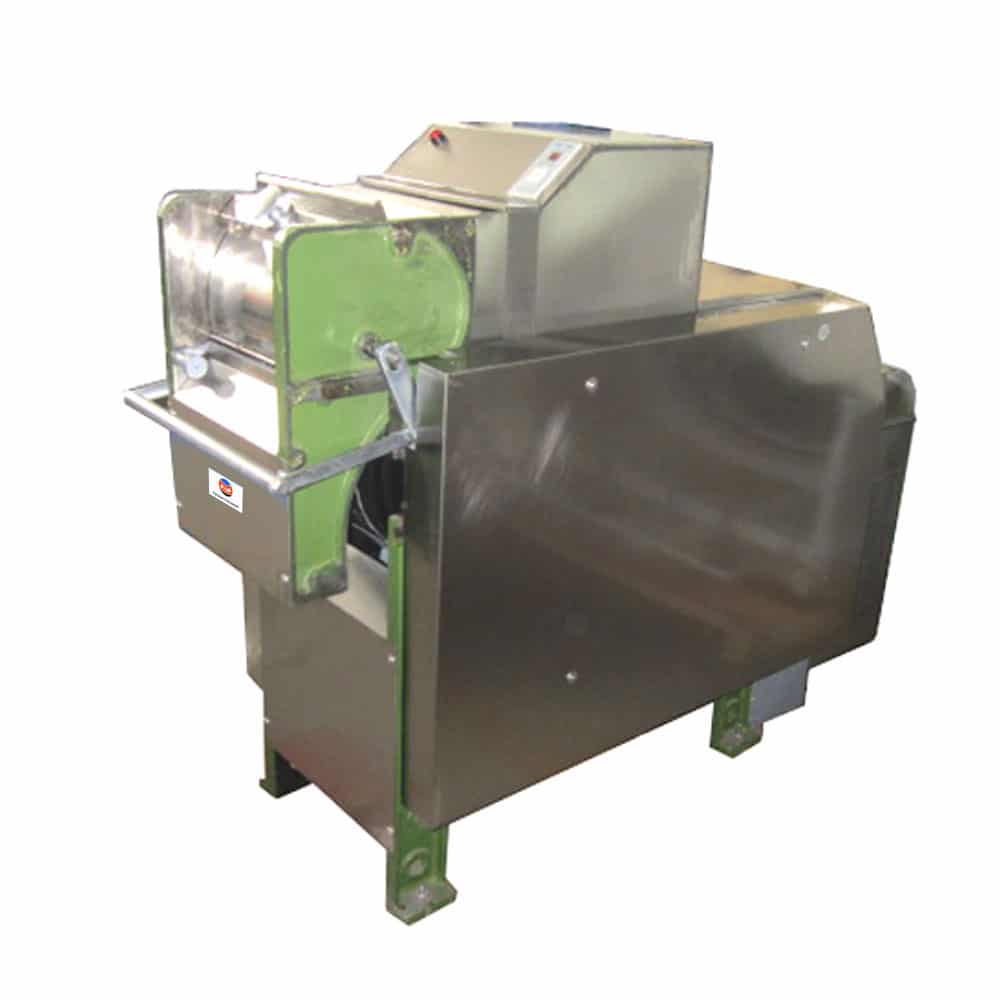
Structural composition and function
Different types of cotton ginning machines have different composition structures, and the structure composition is analyzed according to different classifications below.
Roller ginning machine
The roller ginning machine is mainly composed of five parts: feeding system, cleaning system, cotton pressing system, separation system and discharge system.
1. Feeding system: including feed inlet, conveyor belt and vibrating screen and other components. Their main function is to convey the raw material (i.e. cotton) from the outside to the inside of the gin and pass it through vibrating screens for initial cleaning.
2. Cleaning system: including fan, vacuum cleaner and cleaning cover and other components. Their main function is to suck away the impurities (such as branches, leaves, etc.) entering the cotton ginning machine from the feed port, and discharge them out of the machine.
3. Cotton pressing system: including steel wheels and rubber rollers and other components. Their main function is to compact the cotton after preliminary cleaning for better subsequent processing.
4. Separation system: including brushes and sieves and other components. Their main function is to separate the compressed cotton from cottonseed and other impurities for further processing.
5. Discharge system: including components such as discharge port and fan. Their main function is to discharge the separated cotton and cottonseed out of the cotton ginning machine respectively, and to suck away the impurities remaining inside the cotton gin.
Saw ginning machine
The basic structure of the saw ginning machine is composed of several parts such as feeding, cleaning, and ginning.
Feeding and cleaning system
The cotton feeding and cleaning part of the saw ginning machine is composed of cotton storage box, flower feeding roller, speed governor, cleaning roller, miscellaneous net, miscellaneous spiral, cotton dripping board and other parts. It works like this:
(1) Store the seed cotton separated by the conveying device to ensure the continuous and uniform production of the cotton gin.
(2) Loosen the seed cotton and remove impurities to facilitate the hooking of the sawtooth and improve the quality of the lint.
(3) The seed cotton is continuously and evenly supplied to the ginning part, and the amount of flower feeding can be adjusted within a certain range, so that the cotton gin is in a continuous and normal working state.
Ginning system
The ginning part is the main working part of the ginning machine, which consists of three parts: the front box, the middle box (also known as the working box), and the rear box (also called the brushing box).
- The front box is located under the front of the cotton gin. Its function is to remove boll shells, stiff petal cotton, small flower heads and other heavy debris in the seed cotton, so as to improve the quality of lint, protect the saw blade from damage, and feed the seed cotton evenly into the ginning work box
- The middle box is also called the ginning work box, which is the main part of the saw ginning machine, and its function is to separate the cotton fiber and cottonseed.
- Back box, also called brushing box, its function is to blow off the cotton fiber on the saw blade, send it to the cotton collection part, and remove some impurities in the cotton fiber.
Working principle
Roller ginning machine
The working principle of the roller ginning machine can be simply summarized as follows: the cotton that has been preliminarily cleaned is transported to the pressing system through the feeding system, and then compacted by steel wheels and rubber rollers to make it more compact. Subsequently, the cotton is separated from the cottonseed and other impurities through the separation system and discharged out of the cotton gin through the discharge system.
Specifically, the workflow is as follows:
1. Cotton feeding: First, the cotton after preliminary cleaning is sent into the cotton gin by the conveyor belt. During this time, the vibrating screen will further clean it.
2. Compaction: Next, the cotton that has been preliminarily cleaned and entered the interior of the cotton gin will be compacted by steel wheels and rubber rollers for better subsequent processing.
3. Separation: The compacted cotton will enter the separation system, where brushes and sieves will separate the cotton from cottonseed and other impurities.
4. Discharge: Finally, the separated cotton and cottonseed will be discharged out of the cotton gin through the discharge system, while the impurities remaining inside the cotton gin will be sucked away.
Saw ginning machine
The seed cotton is preliminarily loosened and cleaned by the multi-drum cleaning machine, and then fed into the cotton storage box, and then enters the front box along the cotton feeding roller and cleaning roller along the cotton board. The front box is equipped with mechanical parts such as cotton take-in rollers and shell resistance ribs. The saw blades of the saw drum protrude from the gap of the ribs of the blocking shell and contact the seed cotton in the front box, and the seed cotton is transferred to the saw drum by the cotton pulling roller. When the saw blade drum rotates, the saw blade catches the fiber and brings the seed cotton into the middle box through the shell resistance rib. Since the seed cotton is continuously brought into the middle box by the saw blade and rotates with the saw blade drum, the lap movement is formed in the lap box (composed of arc-shaped cohesive plates and movable cover plates). When the seed cotton is brought to the ginning ribs by the saw blades of the saw drum, the cotton seeds cannot pass through because the gap of the ginning ribs is smaller than that of the ginned cotton seeds. Then, the fiber is separated from the seed and brought into the back box by the saw blade, and the unpassed seed will be output from the seed outlet.