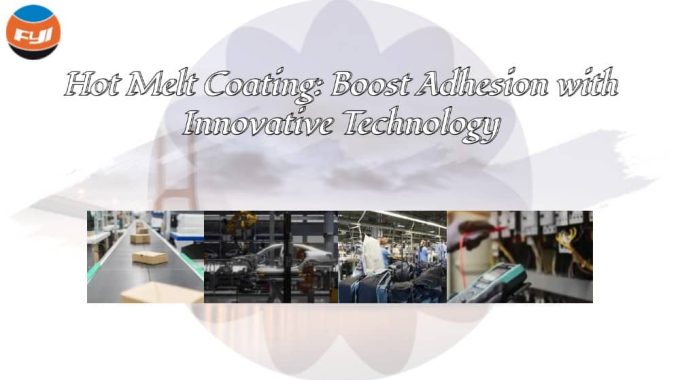
Hot Melt Coating: Boost Adhesion with Innovative Technology
Hot melt coating involves heating and melting organic compounds such as asphalt, paraffin, polyethylene, polypropylene, polyethylene terephthalate, and polyacrylic acid resins into a liquid, and then coating the substrate. The coating is carried out in an adiabatic state, and the finishing is measured with blade. The coated paper web is cooled by a cooler or a cold cylinder; The molten coating is formed on the substrate to form coating. And the coating is rolled and processed into finished products.
Contents
Working principle
First, heat the hot melt adhesive box and guide the paper or other substrate in the direction shown in Fig.1. When the hot melt adhesive box is heated to the set melting point temperature of the hot melt adhesive, the hot melt adhesive is melted. The melted adhesive is pressed into the coating die by the hydraulic system; The coating die is placed against the substrate, and the hot melt adhesive is sprayed onto it. At the same time, start the transmission motor to press the pressure roll and the composite roll together, and adjust the pressure to the appropriate level; Adjust the flatness of the substrate by adjusting the position of the deviation roll; By adjusting the tension of the clutch and brake to control the traction tension of the substrate, the machine runs smoothly, thereby achieving good coating and composite quality and effect.
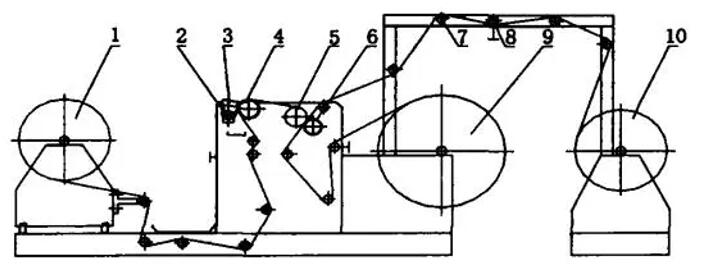
1 Web guiding and unwinding unit
2 Coating die base
3 Coating die
4 Coating roll
5 Composite roll
6 Press roll
7 Guide roll
8 Deviation roll
9 Rewinding unit
10 Unwinding unit
Main structure of coating machinery
The main structure of hot melt coating machine usually includes heating system, coating system, temperature control system, pressure control system. The heating system is responsible for heating the hot melt adhesive to liquid, the coating system is used to evenly coat the liquid hot melt adhesive on the substrate, and the temperature control system and pressure control system work together to ensure precise control of the coating process. In addition, coating machine also has some auxiliary devices, such as pneumatic clamp or mechanical clamp, used to fix the roll for coating operations.
Coating system is a key component of hot melt coating machine, and its structure usually includes coating die, coating roll, etc. The coating die affects the thickness and uniformity of the coating layer by controlling the width and shape of the coating mouth. The coating roll is the core component of the coating system, and realizes coating by rotation, and the surface material and treatment method also has an important influence on the coating effect.
Control System is the intelligent core of the entire equipment, usually using advanced PLC (programmable logic controller) and touch screen interface. Through the control system, the operator can easily set the coating temperature, pressure, coating speed and other parameters, to achieve accurate control of the coating process.
What are the factors that affect the coating of hot melt adhesive?
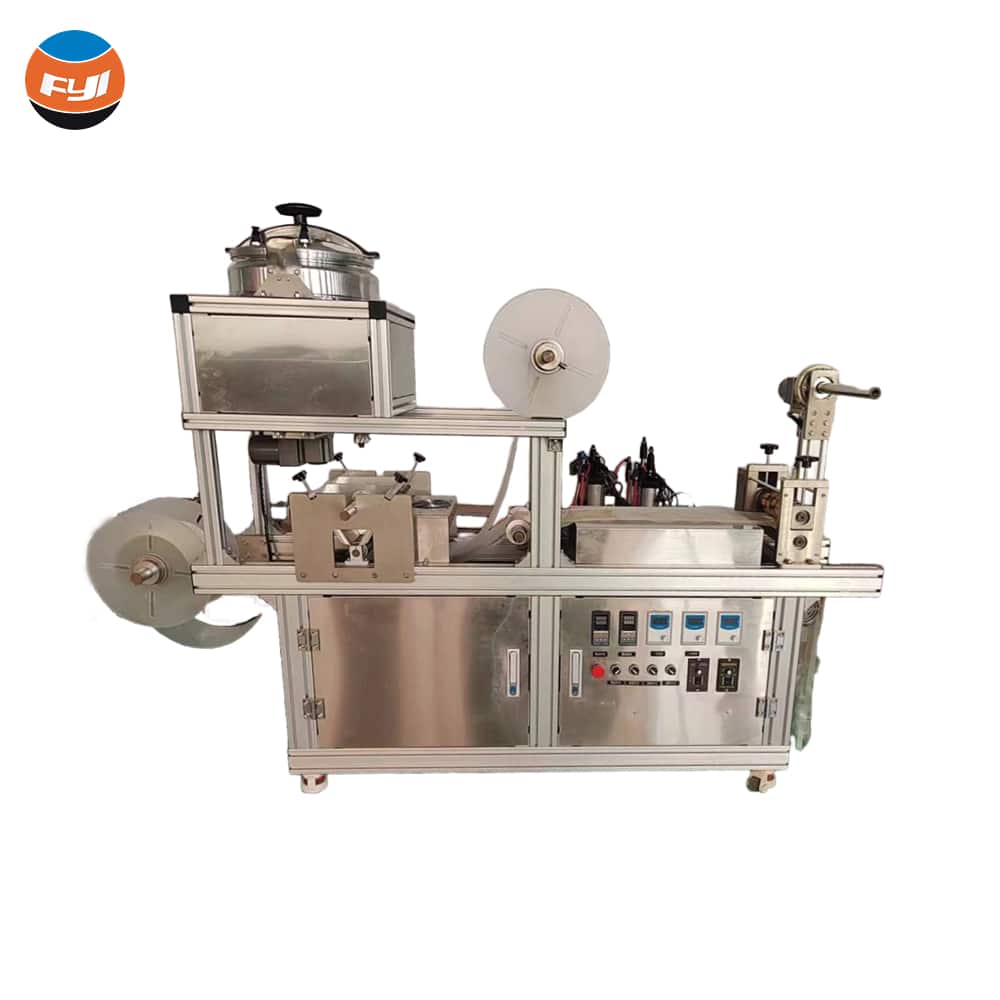
Temperature: The viscosity of hot melt adhesive will change with temperature. Generally speaking, as the temperature increases, the viscosity of hot melt adhesive will decrease, resulting in an increase in coating amount. Therefore, controlling the temperature of hot melt adhesive is one of the important factors in adjusting the coating amount.
Pressure: The pressure of the coating machine can also affect the coating amount of hot melt adhesive. If the pressure is too high, the hot melt adhesive will be squeezed out too much, resulting in excessive coating amount; On the contrary, if the pressure is too low, the coating amount will decrease. Therefore, reasonable control of the pressure of the coating machine is the key to maintaining an appropriate coating amount.
Speed: The coating speed also has an impact on the coating amount of hot melt adhesive. Generally speaking, a coating speed that is too fast will result in a decrease in coating amount, while a speed that is too slow will result in an increase in coating amount. Therefore, adjusting the coating speed is one of the important means to regulate the coating amount.
Geometric shape and surface characteristics: In practical applications, it is necessary to consider the shape and surface characteristics of the coated object, such as flatness, roughness, etc. These factors will affect the distribution of hot melt adhesive on the surface, thereby affecting the size of the coating amount.
Advantage
Compared to traditional coating techniques, hot melt adhesive composite coating machine have the following advantages:
- The melting point of the melt adhesive is relatively low, which saves energy during the production process;
- The application amount and speed of adhesive glue are higher than traditional coating techniques;
- The viscosity of hot melt adhesive is relatively high, so it can bond different materials more firmly;
Different adhesive systems can be used to meet the production and processing requirements of different industries. For fields with higher precision requirements, hot melt coating machine can not only greatly improve production efficiency, but also reduce product quality losses.
Application area
Packaging industry: Hot melt adhesive is widely used in carton bottom sealing, sealing, tape coating and other processes. Hot melt coating machine can help the packaging industry to study the coating performance of different types of hot melt adhesive on high-speed production lines, improve the sealing strength and production efficiency.
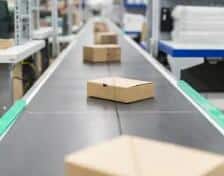
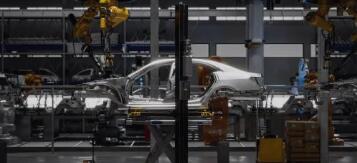
Automobile Manufacturing: In the automobile manufacturing process, hot melt adhesive is used in the body assembly, sealing and other key links. The coating uniformity of hot melt adhesive can be optimized through the hot melt coating machine, and the bonding strength and durability of automotive components can be improved.
Textile Industry: In the textile industry, the hot melt coating machine can be used to study the performance of different hot melt adhesive on the waterproof and windproof properties of textiles. By optimizing the coating process, the functionality and adhesion of textiles can be improved.
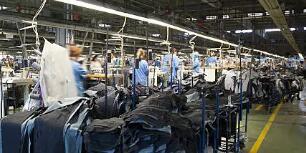
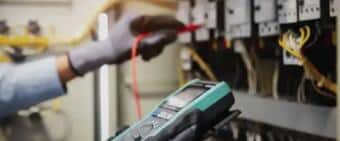
Electronics Industry: In the electronics industry, hot melt coating machine plays a key role in the packaging and fixing of electronic components. By studying the coating effect of different hot melt adhesive on the surface of electronic devices, the reliability and stability of electronic products can be improved.