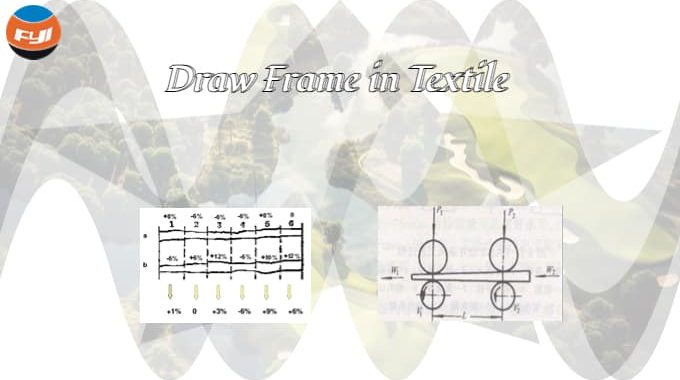
Draw Frame in Textile
Draw frame is applicable for drafting fibers of bending cotton sliver to be straight and improve the degree of uniformity of cotton sliver through combining.
Contents
The importance of draw frame
After the cotton has been opened and carded, if the raw sliver is spun directly without passing through the draw frame, there will be problems.
1. Poor straightening and parallelism of fibers in raw sliver may lead to uneven yarn evenness and poor strength.
2. A small amount of tufts in the card sliver can result in a lot of thick places and fine details.
Tasks for the draw frame
1. Merging: Improves evenness of medium and long segments of sliver.
2. Drafting: Improve the straightening and separation of fibers.
3. Mixing: Thoroughly mix the fibers
4. Quantitative control: Control the fineness of the sliver according to the fineness of the spun yarn.
5. Sliver: Winding into appropriate rolls for use in subsequent processes.
The basic principles of drawing and drafting are introduced below.
Merger principle
Several slivers are fed into the drafting device in parallel and merged together along the length direction to form a sliver. This process is called merging. After merging, the uniformity of the product will be improved to a certain extent.
1. Uniform action of mergers
There are three possible cases of merging (two roots as an example):
(1) Thick places and fine details are merged, and the uniformity is greatly improved after merging.
(2) Thick places merge with thick places, details and details, and the uniformity does not improve, but it does not deteriorate.
(3) Random merging (thickness or detail and moderate fragment merging), the unevenness is reduced.
Thus, the uniformity of the sliver after merging can be improved.
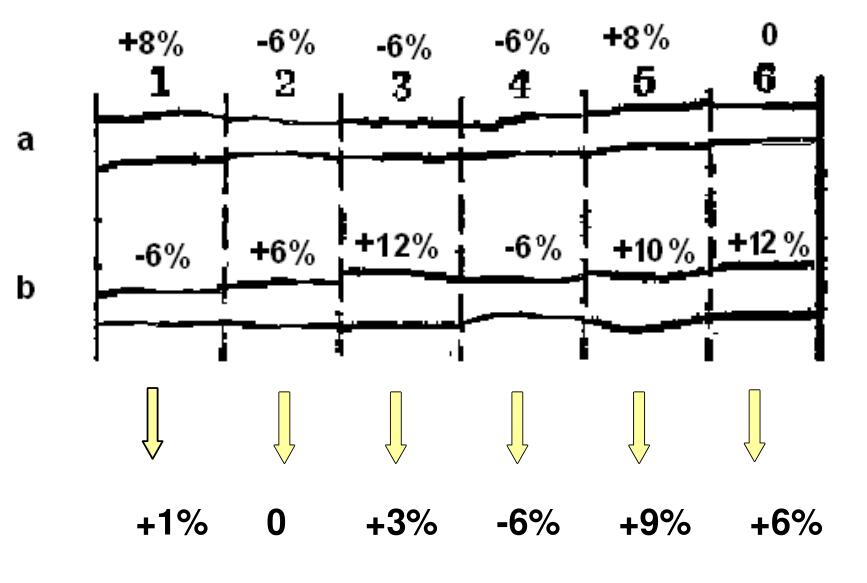
2. The relationship between sliver unevenness before and after merging
The unevenness of n fiber strips with the same weight and the same unevenness C0 combined,
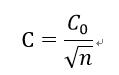
In the formula, C0 is the unevenness rate (%) of the sliver before merging, and C is the unevenness rate (%) of the sliver after merging.
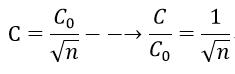
The calculation of the above formula list is as follows:
n | 1 | 2 | 3 | 4 | 5 | 6 | 7 | 8 | 10 | 12 |
C/C0 | 1 | 0.71 | 0.56 | 0.5 | 0.45 | 0.41 | 0.38 | 0.35 | 0.32 | 0.29 |
Draw a graph according to the above table:
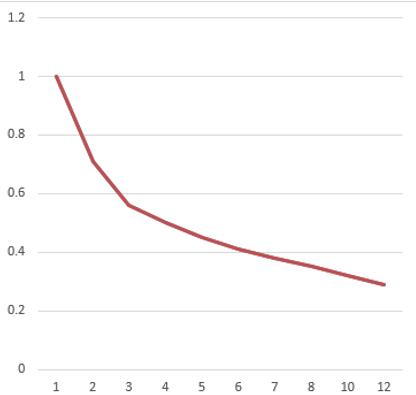
From which you can get:
- The more merging numbers, the lower the unevenness of the merging strands.
- When the combined number is small, increasing the number of roots will reduce the unevenness significantly; when the combined number is large, the unevenness will not decrease significantly.
- Therefore, when choosing the number of merging roots, the comprehensive effect of merging and drafting should be fully considered. The larger the number of merging roots, the better. Generally, 6-8 merging is used. Generally, 6-8 merging is used.
3. Ways to Improve Sliver Irregularity
The types of unevenness are divided according to the sampling method:
(1) Internal unevenness I: Unevenness in the same eye or in the same package.
(2) Outer unevenness E: Unevenness between different packages.
(3) Total unevenness T: The comprehensive response of internal unevenness and external unevenness.
The relationship between these three unevenness is T*T=E*E+I*I.
The way to reduce the unevenness of the sliver is:
- Light and heavy sliver matching: The slivers produced by different cards (light sliver, heavy sliver, medium weight sliver) are matched and fed to each eye of the draw frame.
- Positive feeding: Reduces unintentional elongation caused by negative dragging sliver feeding.
- End-break automatic stop: to ensure the correct number of feeding strands
Fundamentals of Roller Drafting
1. Drafting overview
Drafting: The strands are drawn long and thinned, so that the cross-section of the strands becomes thinner and thinner, and the fibers are straightened and parallel.
Roller drafting: Rollers with different speeds are used to achieve drafting.
The essence of drafting actually refers to the relative slippage between fibers.
2. Conditions for implementing drafting
- There are two jaws that actively hold the sliver: roller pressurized
- The distance between the jaws should be greater than the quality length of the fiber.
- The surface linear speed of the first pair of (output) rollers is greater than the surface linear speed of the latter pair of (feeding) rollers.
The three conditions are also the three main process parameters of drafting.
3. Draft type
The first type of drafting is tension drafting: the speed difference is small, the axial relative displacement does not occur between the fibers, and the strands undergo elastic deformation. Prevent the beard from falling loose.
The second type of drafting is displacement drafting: the speed difference is large, relative movement occurs between fibers, and the strands are drawn and thinned, which is a permanent deformation.
4. Drafting ratio
The draft ratio E indicates the degree of elongation and thinning of the fiber assembly. Generally divided into two types, mechanical drafting multiples and actual drafting multiples.
The formula of mechanical draft ratio (theoretical draft ratio) is E=V2/V1, and V1 and V2 refer to the surface speed of the front and rear rollers.
The formula for the actual draft ratio is E=L2/L1=W1/W2. L 2 and L 1 refer to the length of the aggregate before and after drawing, and W1 and W2 refer to the linear density (quantitative amount) of the aggregate before and after drawing.
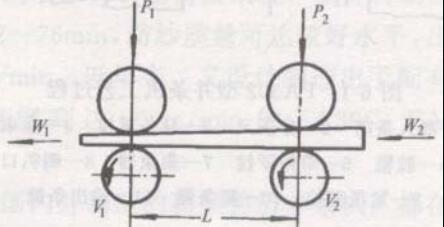
The calculation formula of drafting efficiency η is η=actual draft ratio/mechanical draft ratio*100%.
Due to factors such as roller slippage, the drafting efficiency is often less than 1; when there is a lot of fiber loss, the drafting efficiency is occasionally greater than 1.
The reciprocal 1/η of the drafting efficiency is called the drafting ratio, and its value is obtained from historical statistical data. According to 1/η in actual production, the mechanical drafting ratio is calculated, and then the number of teeth of the drafting conversion gear is determined.
5. Combination and distribution of drafts
Drafting combination
Each drafting mechanism usually consists of 1 to 3 drafting areas. The partial drafting undertaken by the drafting zone varies according to the condition of the fed sliver, drafting type, and mechanical conditions. Reasonably combine various types of drafting zones to form a drafting mechanism with simple mechanism and good effect, and rationally distribute partial drafting of each drafting zone, which can increase the total drafting amount and improve product quality.
Distribution of draft
After the sliver is drafted, the connection between fibers is weakened, and the ability to withstand drafting in the next drafting zone is correspondingly reduced. So too much draft zone doesn’t necessarily increase the total draft much. Sometimes a collector is used after a drafting zone to make the fibers in the sliver tightly assembled, and then drafted.
For example, the drafting of 4 pairs of simple rollers can have three drafting areas. Their draft distribution gradually increases from back to front, which is called continuous draft or incremental draft. If a collector is used in the middle drafting area to make the strands drafted in the rear area close together, and the drafting ratio is equal to or close to 1, then the drafting mechanism of 4 pairs of rollers actually only uses two drafting areas, called For dual zone drafting. Dual-zone drafting is characterized by the addition of a collective zone between the two drafting zones.
Related precision control issues
Improving the drafting mechanism and increasing the drafting ratio can reduce the number of process passes and increase productivity. Mechanisms that increase the draft ratio are sometimes referred to as high-draft mechanisms. Direct drafting from sliver into spun yarn is called super draft, and the drafting ratio can reach about 250 times. The larger the draft ratio, the easier the fibers are to spread, and thus the more precise control is required.
Comments are closed.
He has a remarkable talent for connecting with readers through his writing.
A blog like this is long overdue – it offers valuable insights and expert analysis.
From personal anecdotes to comprehensive research, this blog offers a well-rounded reading experience.
This article tackles an important issue that often goes overlooked in mainstream media.
To say that I was impressed by this article would be an understatement – it provided a comprehensive understanding of the topic.
Most impressive is the author’s ability to tackle complex topics with clarity and depth.