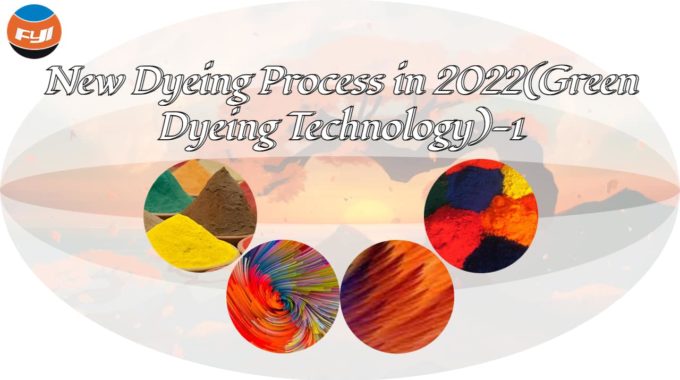
New Dyeing Process in 2022(Green Dyeing Technology)-1
With the progress of society and the improvement of people’s quality of life, people pay more and more attention to the environment and their own health. Wearing “green textiles” and “ecological textiles” has become the living needs of people in today’s world. Green dyeing technology is the key development direction of textile dyeing in the future.
Green dyeing technology is distinguished by the use of non-harmful dyes and auxiliaries, as well as the dyeing and processing of textiles using non-polluting or low-polluting procedures. The amount of colored sewage emitted after dyeing is little, and it is easy to filter and deal with, as is the amount of energy consumed, and the dyed goods are “green” or ecological textiles. To that purpose, much research has been conducted in recent years both at home and abroad, and various innovative dyeing processes with lower pollution or ecological needs have been presented and pushed.
Waterless dyeing, energy-saving dyeing, solubilizing dyeing, new paint dyeing, short-process, multi-effect dyeing and finishing, computer application and controlled dyeing are all examples of the new dyeing process.
Contents
Dyeing with natural dyes
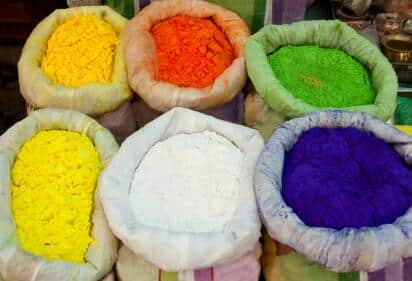
With the prohibition on some synthetic dyes, people’s interest in natural dyes has grown again, owing to the fact that most natural dyes are environmentally friendly, biodegradable, and have minimal toxicity. Synthetic dyes are made from petroleum and coal chemical compounds. These resources are now being depleted fast. In this regard, the creation of natural dyes is also beneficial to environmental conservation. Although natural dyes cannot totally replace synthetic dyes because to their numerous shortcomings, they are useful as a partial substitute or complement to synthetic dyes.
The chemical structure of natural colors is still unknown, and the extraction procedure is also quite inefficient. As a result, research and development are required for its extraction and use, particularly the complete usage of plant leaves, flowers, fruits, and rhizomes, and the use of other industrial wastes to extract natural colors. Natural dyes with high production and performance are predicted to be generated through genetic engineering as biotechnology advances. Natural dyes’ characteristics and structures are poorly understood, and further study is needed.
Substitute Dyestuffs for Banned Dyes
Many synthetic dyes have been outlawed due to the gradual improvementof ecological textile standards such as Eeo-Tex Standard 100, prompting dye makers to generate a huge number of synthetic dyes that fulfill ecological requirements in recent years. More dyes will be created in the future, as will dyeing process.
Dyeing with high fixation or high uptake dyes
One of the most serious environmental issues in dyeing is dye pollution in dyeing effluent. The creation and use of dyes with high dye absorption or fixation rates can significantly reduce dyes in wastewater while simultaneously improving dye utilization rates. At the moment, various reactive, dispersion, and cationic dyes with high fixing rates have been created, which minimizes residual colors in wastewater, as well as water consumption for washing after dyeing and the amount of wastewater produced.
Dyeing with high fastness dyes
Dye fastness is strongly connected to the ecological criteria of coloured fabrics. The color fastness of textiles can be detected by a color fastness tester. Some water-soluble dyes that were formerly employed, such as direct dyes for dyeing cellulose fibers, acid dyes for dyeing wool and silk, and so on, have poor wet fastness. Such dyes not only harm the environmental quality of textiles, but the dyeing wastewater is difficult to filter. Such dyes have increasingly being phased out in favor of dyes with high color fastness, such as reactive dyes with high wet fastness.
In the past, disperse dyes were mostly employed to color synthetic and acetate fibers. The wet fastness is good due to the low solubility of dispersion dyes, and the waste water is very easy to filter. Disperse dyes for wool and silk textile dyeing have been investigated and developed in recent years, and are particularly useful for coloring mixed textiles of these fibers and synthetic fibers. The increased use of such dyes is also beneficial to the promotion of “green” dyeing methods.
One-bath, one-step and short-run dyeing
Blended or interwoven textiles of different fibers are frequently colored with more than two types of dyes, which not only has a long process flow and is expensive, but also uses a lot of energy, water, and sewage. One-bath dyeing research and development is good for reducing sewage and saving energy. Dispersive/active one-bath dyeing, for example, is gaining popularity and becoming more extensively employed.
Many dyestuffs, such as disperse/reactive dyeing, must be fixed in two phases. To fix the color, disperse dyes require high temperature steaming or baking, whereas reactive dyes require saturated steam. To fix the color, appropriate additives might be applied. They are steamed or baked at high temperatures in order to achieve one-step fixing. The one-step dyeing technique may also meet the goal of shortening the dyeing process, conserving energy, saving water, and boosting production efficiency, all of which are environmentally advantageous.
One-bath, one-step and short-process processes also include bleaching and dyeing, dyeing and finishing, and the process flow is shorter.
Low liquor ratio, low feed solution dyeing
Dyeing using a low liquor ratio or a low feed solution not only saves water, but also results in a higher dye usage rate and reduced waste water outflow. Some of the modern slow-flow and gas jet dyeing equipment, for example, are now dying with extremely tiny bath ratios and keeping the materials in quick circulation with very little coloring effluent.
The employment of a spray, foam, and single-sided dosing roller system may significantly lower the dosing rate, which is especially useful for administering dye liquid or other chemicals during pad dyeing, such as lye for fixing the color of reactive dyes. Not only does this save water and sewage, but it also enhances fixation and saves steam or thermal energy.
Similarly, the use of a high-efficiency rolling mill and a vacuum suction system may increase the impact of cushioning and deliquoring while saving energy, water, and pollution.
Computer-controlled staining
Use a computer to manage the dying process to get the optimum dyeing process. For example, at the moment , the entire dyeing process is optimized and controlled by computer based on the dyeing characteristic values of reactive dyes and the kinetic parameters of dyeing and fixing, which not only efficiently performs “right first time” dyeing, but also has good product quality and a short production cycle. This method is also applicable to other types of dyes, such as dispersion dyes and other dyeing.
More dyeing processes such as waterless dyeing and low temperature dyeing will be posted in the next blog.
Leave a Reply
You must be logged in to post a comment.
Loving the information on this site, you have done great job on the content
The author’s ability to simplify complex ideas is truly commendable.