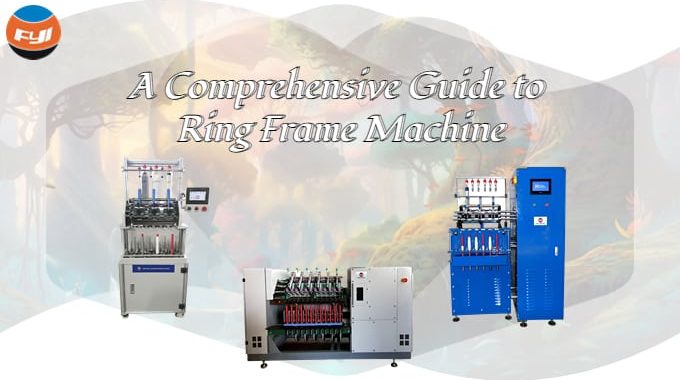
A Comprehensive Guide to Ring Frame Machine: Importance, Process, Disadvantage and Types
Contents
What is ring frame machine?
Ring frame machine: a spinning machine in which half products of roving or sliver are drawn, twisted and wound into muslin in the spinning process; sliver is drawn and twisted on a roving machine to make roving; a combing machine to carding fibers into combing slivers; a needle carding machine to combine slivers; needle drawing improves sliver structure; roving is further twisted into muslin on a ring spinning machine; spinning machine is the main machine for spinning. The output and quality of fine yarn are the comprehensive reflection of each process of spinning technology.
What is the importance of ring frame machine?
The spinning process is the last process of spinning, but also an important process of the textile factory, the total number of spinning process is an important symbol to measure the size of the cotton textile factory and production capacity, the output of spinning process determines the textile factory each process of mechanical equipment equipment, the output level, determines the production level of the enterprise; The quality and consumption of fine yarn determine the cost of spinning. The breaking rate of fine yarn is an important index of enterprise assessment. Therefore, the spinning process can comprehensively reflect the production technology and management level of a cotton mill.
The task of spinning process
1. Draft
The fed roving is drawn evenly long and fine to the required number of special yarn.
2. Twist
Add appropriate twist to the drawn whisk to make the yarn have certain physical and mechanical properties such as strength, elasticity, luster and feel.
3. Winding
The spun yarn is wound on the bobbin in a certain shape to facilitate transportation, storage and further processing.
What is the ring frame process?
Ring spinning frame is the most common. The common ring spinning frame is of double-sided multi-spindle structure, which is mainly composed of feeding mechanism, drafting mechanism, twisting winding mechanism and forming mechanism. The roving is unwound from the roving tube on the roving frame and fed into the drawing device for drawing through the guide rod and the slow reciprocating cross movement of the guide horn. The drawn whisker is output from the front roller through the yarn guide hook, through the wire ring, and wound to the bobbin tight on the spindle. The spindle turns at high speed. The wire ring is driven to turn at high speed on the steel collar by the yarn strip with certain tension. Each turn of the wire ring adds a twist to the drawn whisk. Because the rotation speed of the wire ring is less than that of the yarn tube, the continuous output yarn strip of the front roller is wound to the yarn tube. The speed difference between the wire ring and the yarn tube is the number of winding turns per unit time of the yarn tube. Depending on the control of forming mechanism, the steel collar plate rises and falls according to a certain rule, so that the fine yarn is wound into a certain shape yarn.
What is the disadvantage of ring frame?
The production of spinning frame accessories is the first step in the textile industry chain. The quality of its products, the efficiency of production and the size of processing cost play an important role in the whole industry chain. Therefore, the development of spinning technology and the promotion of new technology are paid more attention at home and abroad. With the continuous development of spinning technology, there are two kinds of spinning technology in spinning production at present: one is ring spinning technology, the other is new spinning technology, which is widely used.
Due to long hours of work, there will be some problems in the spindle position of the spinning frame, which need to be repaired by maintenance personnel, which is a very important quality control work in the spinning mill. Due to the large number of spindles, from thousands to hundreds of thousands in the same plant, how to eliminate these defective spindles is a long and arduous task, but it is extremely necessary to reduce yarn quality uneven. Most of these defects are related to ring and spoke damage, draft difference, roller deviation, yarn frame, etc.
What are the three types of spinning?
Common roving frames are generally divided into three categories: frame spinning frames, spinning frames and ring spinning frames. Frame spinning frame and spinning frame are discontinuous spinning frame. Ring spinning frame belongs to continuous spinning frame. There are some differences in the spinning methods corresponding to these three roving spinning frames, and there are also many differences in performance.
According to relevant studies, the uniformity of these three spinning frames is relatively lower than the first two, but the spinning efficiency is higher than the other two. Each of these three spinning frames has its own merits.
The difference in the spinning of different roving frames is due to the difference in the spinning. The first two ways of walking twist is horizontal, no control area length, winding without twisting twisting without winding, the balance of twist is good, so its uniformity is much better, but its drafting area is too long.
Ring spinning frame twist is vertical, the twist balance time is short, so its uniformity is poor, because the control zone is short, so its broken end is much less problem.
It is because of the different working mechanisms that there are differences in the quality and efficiency of their production. For each enterprise, different roving spinning frame can only be selected according to the actual needs of their own production to achieve the highest efficiency.
How do you tell the four yarns apart
Ring spinning yarn
The whole yarn can be completely untwisted in ring spinning, and the yarn has no strength after untwisting:
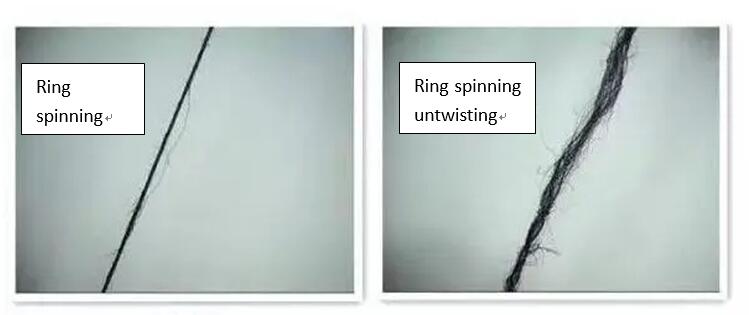
Air spinning yarn (spinning cup spinning)
As in ring spinning, the whole yarn cannot be completely untwisted. Only a few parts can be completely untwisted. Therefore, after untwisting, the untwisted nodes are not strong, and the whole yarn will break once pulled:
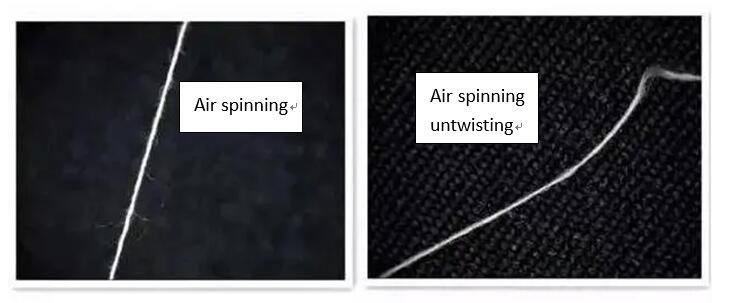
Siro spun yarn
Siro spinning the whole yarn can be completely untwisted, after the end of the twist yarn is not have strength
Of these four yarns, Siro spins the only one that appears to be a single yarn made of two yarns; Siro spinning is high grade ring spinning (when two roving pieces are input together to make a single fine yarn); Good drying, fewer feathers, greater strength than ring spinning:
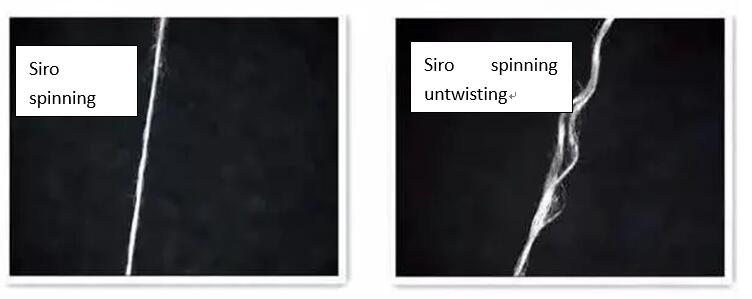
Vortex spinning yarn
After vortex spinning, the outer surface looks completely untwisted, but the yarn core is not untwisted and still has great strength:
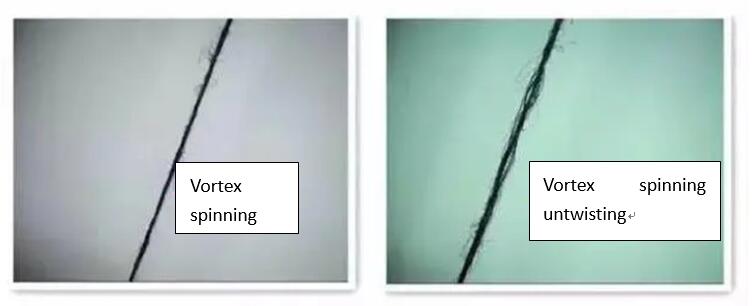
Yarn differentiation process
Step 1: Get a piece of yarn and untwist:
The whole yarn is not completely untwisted, only part of the nodes are completely untwisted, air spinning.
Step 2: Look completely untwisted;
Step 3: See if there is strength:
(Yes → vortex spinning, no → ring spinning)
Step 4: See if there are two:
(Yes → Siro spinning, no → ordinary ring spinning).
DW7040H Lab Ring Spinning Frame
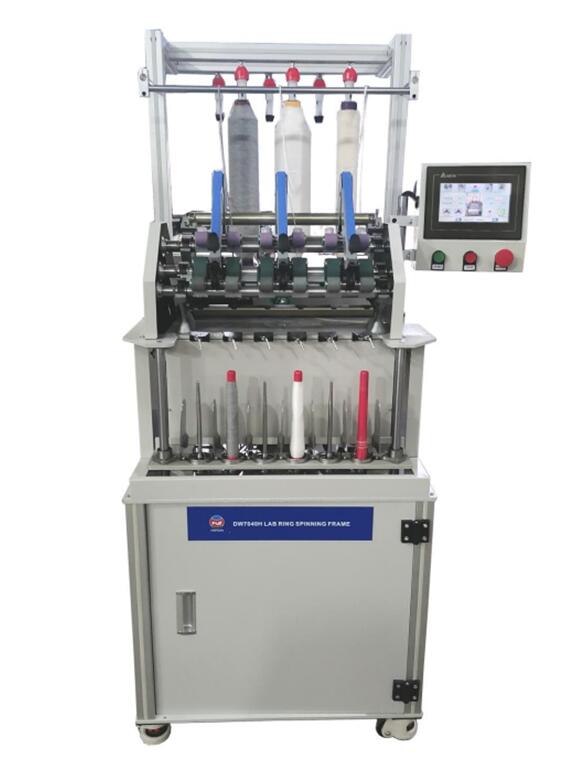
DW7040H Lab Ring Spinning Frame is used to spin roving to be spun yarn through drafting and ring spinning. It’s the ideal system for teaching, researching, etc.
Feature
- Delta brand PLC, drive, servo motor;
- PLC + touch screen control, easy to learn and operate;
- Use touch screen as man-machine interface, input technical parameters and show machine running state by touch screen;
- Use S/Z twist turning;
- Rotation speed of spindle accurate to ±1%;
- Aluminum profile body frame with four casters, free to move;
- Modular independent drive for drafting, spindle blade and flyer;
- Multi-functional design, easy to clean, set and maintain;
Specification
Control mode | Touch screen & PLC |
Number of spindles | 6 |
Applicable fiber length | 22~50mm |
Draft range | 10~50 |
Draft control | Automatic |
Roller diameter | Front roller : Φ25mm, middle roller: Φ25mm, back roller: Φ25mm |
Center distance of rollers | Front and middle: 43mm Front and back: 143mm |
Pressure mode | Spring cradle |
Twist settable range | 200~2,000 twist/m |
Twist direction | S or Z |
Max. speed of spindle | 12,000rpm |
Spindle gauge | 70mm |
Spindle length | 205mm |
Ring diameter | Φ42mm |
Yarn density range | 6~99tex (6~100Ne) |
Comments are closed.
Your posts are always well-written and engaging.
Those who are seeking reliable information on this subject will find this article indispensable.
I can confidently say that this blog is a goldmine of wisdom. Every article is packed with practical advice and actionable tips that can be applied to various aspects of life. I find myself continuously referring back to these articles for guidance and inspiration.