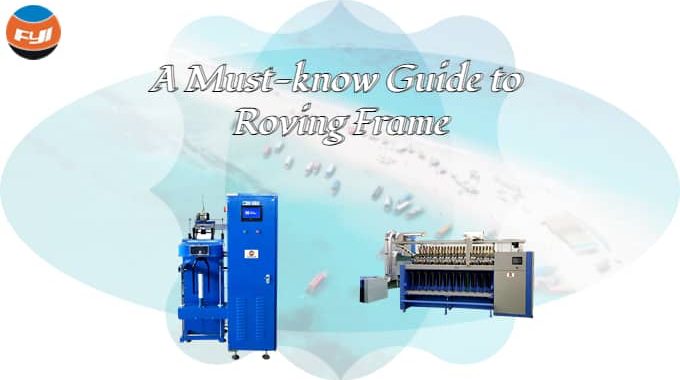
A Must-know Guide to Roving Frame
The roving frame is the main equipment of cotton spinning, and it is also one of the most complex equipment. The quality of the roving frame directly affects the physical performance of the yarn, such as evenness, weight unevenness, strength, and yarn defects. It also plays a decisive role in spinning output, energy consumption, labor, materials, labor productivity, cost, benefit, and floor area.
Contents
Roving, sliver and yarn
A roving frame, also known as a roving machine or fly frame, produces roving from a sliver. The sliver is created in a draw frame, which is located upstream of the yarn manufacturing process. The roving is the raw material used to make yarn, such as in a ring spinning machine. As a result, the roving is much thicker than yarn yet much thinner than a sliver.
Tasks for roving frame
There are three tasks on the roving frame, namely drafting, twisting and winding.
- Drafting: lengthen and thin the cooked sliver, improve the parallelism and separation of fiber straightening;
- Twisting: add proper twisting to increase the strength, facilitate winding and unwinding, and facilitate the drafting of spun yarn;
- Winding: Winding into packages, convenient for transportation and storage, suitable for feeding into spinning frame.
Drafting
The main task of the roving frame is to further draft the sliver into finer count fiber bundles, so-called rovings. This intermediate production step is necessary because the ring spinning machine cannot process coarse slivers into fine yarns. Furthermore, the handling of sliver in ring spinning machines remains unresolved.
This is because, due to the poor strength of the sliver, there is not enough space in the ring spinning frame to store the bulky sliver box that holds the sliver.
Twisting
Another task of the roving frame is to insert a protective twist in the roving to strengthen the textile fiber bundle so that it can be transported without being damaged, since the sliver as well as the fine-count roving are produced from the roving. Without a protective twist, the sliver has little coherence.
Protective twist is a slight twist that is only used to give the roving sufficient (tensile) strength, ie stability for transport. Protecting the twist is again taken care of in the drafting unit of the ring spinning frame.
Winding
The roving is helically wound around the cylindrical winding surface of the bobbin, and the height of the yarn layer decreases from the inside to the outside, forming a shape with truncated cones at both ends and a cylinder in the middle. Therefore, the roving winding movement includes two parts:
- Circumferential movement of the yarn relative to the bobbin.
- The axial movement and moving distance of the yarn relative to the bobbin decrease layer by layer.
Winding should have appropriate tightness to increase the volume of the package. At the same time, it is required that the yarn loops are arranged neatly, with clear layers, no loose loops, and no edge collapse, so that the unwinding can be smooth.
Process flow of roving frame
The roving frame is mainly divided into feeding, drafting, twisting and winding. The sliver is drawn from the sliver can at the back of the machine, conveyed by the guide roller, and fed into the drafting device. After drafting, the sliver output from the nip of the front roller is too low in strength, so the rotating flyer adds an appropriate twist (30~65 twist/m) to form a roving. The roving passes through the top and side holes of the flyer, enters the yarn guide arm of the flyer, and then leads out from the lower end of the guide arm, winds several times on the crank arm of the pressing palm, and then leads to the pressing palm leaf and winds on the bobbin. In order to wind the roving on the bobbin regularly, the bobbin rotates at a higher speed than the flyer on the one hand, and moves up and down with the dragon tendon on the other hand, and finally winds the roving on the surface of the bobbin in a helical shape. .
Composition of roving frame
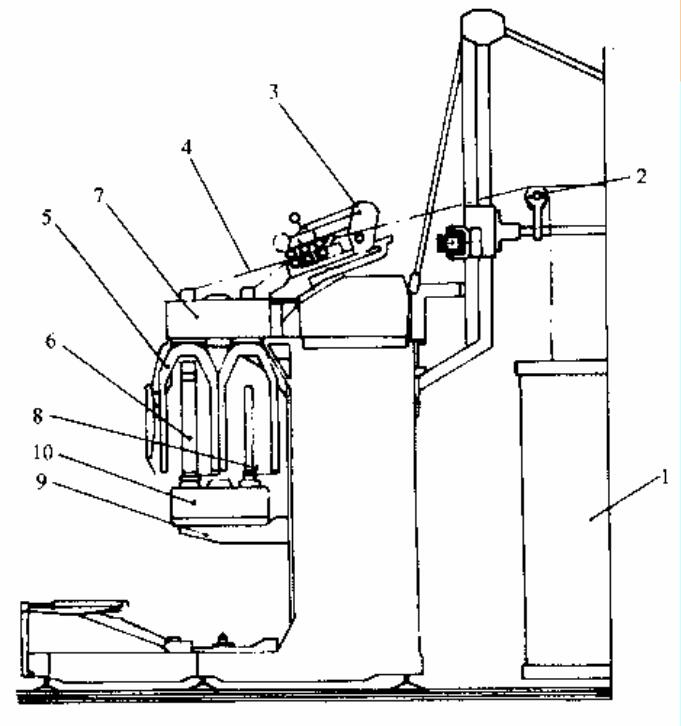
1——Cotton sliver can 2——Guide roller 3——Drafting device 4——Roving 5——Flyer
6——bobbin 7——upper dragon tendon 8——spindle rod 9——lifting pendulum 10——lower dragon tendon
Roving tension and roving elongation
Roving tension
Tension refers to the tensile force acting on the axial direction of the sliver, and its expression is the tension of the sliver. In the roving winding process, in order to make the roving smoothly wound on the bobbin, the winding speed of the bobbin must be slightly higher than the output speed of the front roller, so the sliver must be tense and produce tension.
During the advancing process, the sliver must overcome the frictional resistance at the top sleeve of the flyer, the hollow arm, and the presser palm, so the tension of each section of the sliver from the front roller to the bobbin is different. The winding tension from the presser palm to the bobbin tube is the largest, followed by the tension from the hollow arm, and the spinning tension from the front roller to the top tube of the flyer is the smallest.
Roving elongation
When the tension on the sliver is high, the sliver will elongate due to the relative displacement between the internal fibers, and the degree of elongation can be expressed by the elongation E.
Ε=(l1+l2)/l2*100%
In the formula: l1 – the measured length of bobbin winding (m);
l2——the calculated length of the front roller (m).
Since the spinning section is the sliver forming area, the twist is small and unstable. Although the spinning section has the smallest tension, it is the easiest to elongate. Therefore, it is customary to call the sliver tension of this section roving tension. Small changes in the roving tension will sensitively affect the elongation, thus affecting the uneven weight and evenness of the roving. Therefore, the roving tension is required to be kept at an appropriate level during spinning, so as not to damage the uniformity of the output sliver. It is also necessary to ensure sufficient winding density.
The relationship between roving tension and elongation
The tension of the roving can be determined by visually observing the spinning section. If the sliver is tight, the tension will be high, and if the sliver is loose, the tension will be low. Visual observation can only be used for qualitative analysis but not quantitative analysis, so elongation can be used to indirectly reflect the tension of roving in production.
Factors affecting the relationship between tension change and elongation change include raw material, spinning type, flyer structure and material, whether to use false twister and the structure and material of false twister, machine section size, winding size, process speed, workshop temperature, etc. humidity etc. In the case of adopting a certain false twist method and normal temperature and humidity in the workshop, the roving elongation can be used as an indirect method to detect the roving tension. At this time, the elongation should be controlled within the range of 1.5% to 2.5%, and the maximum should not exceed 3%, and the difference in elongation should be controlled within 1.5%.
Comments are closed.
Too often, blog posts lack substance, but this one is a breath of fresh air.
More real-life examples and personal anecdotes would have enhanced the readers’ connection to the blog topic.
About the topic, this blog provides a comprehensive analysis that leaves no stone unturned.