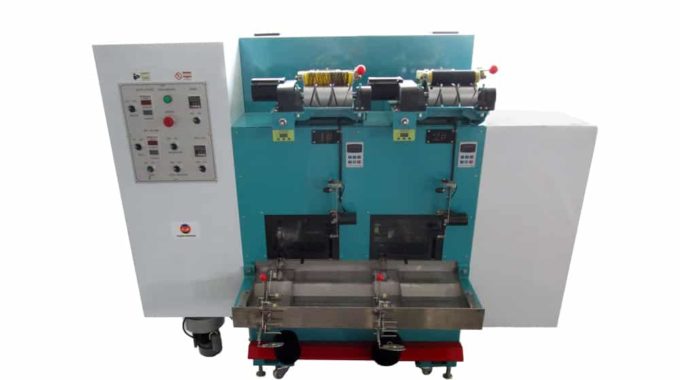
What is Yarn sizing Machine ? The development of Yarn sizing machine
Contents
What is Yarn sizing Machine?
Yarn Sizing Machine GA392 is the equipment for sizing the yarn. After spun into yarn, the fiber has lower strength and more hairiness, which cannot meet the requirements of weaving. In order to improve the yarn strength, reduce hairiness, reduce friction on the surface of the yarn, reduce friction and then sizing for yarn .
Development of Lab Yarn sizing machine
It is difficult to directly weave the original yarn because of its weak interlock and many hairiness on the surface. In order to improve the weavability of warp yarns on the loom. The warp yarns can bear the repeated friction, stretching and bending between warp stop sheets, heald, sley and warp yarns, without losing hair or even breaking. This is what we often say, warp sizing is designed to stick down the hairiness, enhance wear – resistant.
The process of warp sizing dates back to ancient times. At that time, the hand sizing was to roll the warp yarn into sheets, paste it with a brush or reed, and wind it into a weaving shaft after drying. Yuan dynasty acla) in the “agricultural book” use brush Lu graphic for warp sizing. The “overpaste” section in “skywork” records the methods and tools of using starch, bovine skin glue, and bone glue silk. At the end of the 18th century, power looms appeared in Britain, which separated sizing and weaving into an independent process, thus giving rise to the rudiment of modern sizing machine.
After several improvements, by 1853, British patent j. boroff, and so on. So that the sizing machine has its basic characteristics.
- sizing methods: there are several methods of sizing
- Skein sizing is the earliest sizing method used in modern times. There are two ways of sizing: manual and mechanical. This method is suitable for the small batch production of yarn-dyed, ribbon and copy.
- Single yarn sizing: remove single yarn from the bobbin, pulp on the sizing machine of single yarn, and wind the yarn bobbin after drying. Also can be installed in the low speed winding machine slurry tank and dryer. There is also a special design “single yarn sizing machine”. Although this method has low yield and high consumption, it has good sizing quality and high film integrity. Sometimes used in silk and ramie weaving. Recently, it is often used in special fiber sizing.
- The weaving shaft sizing —— is made of the dividing warping machine and then wound to form the weaving shaft. Mainly used in silk weaving, yarn-dyed multi-varieties and small batch production.
- Warp sizing —- -simultaneously extract some warp yarns on the warp shafts, immerse them in the slurry, press out excess slurry, dry and divide the yarn, and finally turn the yarn into woven shaft according to the specified length. This is the most widely used sizing method. In the old silk mill for mucilage, also useful for mucilage.
- Combined grouting — install a set of grouting and drying device between the creel and the head of the warper to synthesize the warping and sizing process, which is mainly used for the sizing of synthetic filament.
- Add dyeing and drying equipment before slurry tank of slurry machine. Mostly used in denim production.
Development history of sizing equipment
Development of drying device
With the formation of sizing machine along with the mechanization of weaving, the change of sizing machine has been very large in the past 100 years. Before the 1950s, China’s sizing machine was dominated by double drying cylinder, which was two large copper drying cylinder pulled by warp sheets to dry the wet yarn. It was called double drying cylinder sizing machine (used at that time: division sung sizing machine —— lu shi sung was an old engineer in Shanghai institute of textile science).
In this way, the sizing speed is slow (about 20m/min), and the elongation of the sizing is quite large. It is now out of use. Later, in the study of “big brother of the Soviet union”, the introduction and manufacture of hot air slurry machine (named 142), and as a national stereotypes machine, promoted and applied in textile factories across the country. The textile factories established in the 1950s and 1970s almost all use g-142 sizing machine {full hot air (G142D), hot air + cylinder (G142C), total cylinder (G142E)}. It is heated by the heater air, air heat transfer, moisture carrier and wet sizing yarn to dry sizing. Hot air slurry machine by hot air flow mode of different natural convection and hot air jet.
The hot air jet type also has the high pressure jet and the low pressure jet two kinds. The hot air jet slasher has high drying efficiency, with the highest speed up to 45m/min, but it is generally used around 20m/min.
In order to overcome the respective defects of the hot air type and the hot air type. After the improvement of the combined heat air type. The hot air drying is usually arranged in the front (called the hot air predrying). And the drying of the hot air type is completed after the drying. This kind of sizing machine has a wide adaptability, high drying efficiency, good quality of sizing and a speed of 35m/min ~ 55m/min. For example: g-146 sizing machine.
In recent decades, with textile clothing to thin, soft, close and comfortable development; And the actual trend of high speed, high efficiency and wide width of loom. Higher requirements are put forward for sizing machine and sizing process. Feel the above three kinds of sizing machine has been inadequate. Thus modern sizing machine are basically more than with smaller diameter slasher cylinder machine (drying cylinder diameter is 800 mm Φ). And it is based on multiple finish drying cylinder to the nine drying cylinder. There are 16, even more than 24 drying cylinder sizing machine. At present, domestic and foreign famous sizing machine is basically belong to this category. The slurry speeds can range from 50m/min to 80m/min, and some can reach over 100m/min.
Development of slurry absorption system
As the name implies, slurry absorption mode and slurry absorption device of slurry machine are also key parts of the slurry machine. There are three methods of warp absorption: the warp layer is immersed in the slurry to absorb the slurry and solvent (usually water). Polyurethane grouting: the warp yarn is pulled at a certain wrapping Angle through the pulping roll with slurry to allow the warp layer to absorb a certain amount of slurry and solvent (water). This method is mainly used in the silk industry for viscose and synthetic filament sizing. Towing in modern sizing is an improved version.
Spray suction: spray the prepared slurry to the yarn layer at a certain pressure. Or apply it to the yarn sheet by electrostatic spraying. And then make the paste on the yarn layer fully pasting and drying semi-dry sizing. Exploratory trials have been rare.
The cotton textile industry has been using the mortar method. In the past, the slurry machine was mainly a single slurry tank with single immersion and single pressure. And the slurry attracted was basically attached to the surface of the yarn.
If you need more information about yarn sizing machine theory or yarn sizing machine price .please send email to [email protected].
Comments are closed.
This is pretty cool, well, i had something to share people may check this if useful.