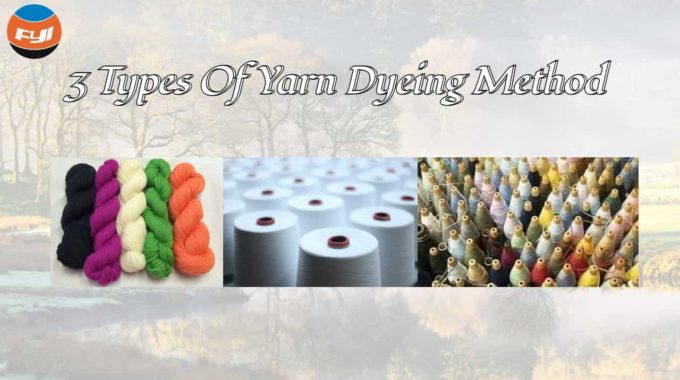
Yarn Dyeing | 3 Types of Dyeing Method
Yarn dyeing refers to dyeing the yarn to a selected color before weaving or knitting. Yarn dyeing can generally obtain a good and firm leveling effect. It can be woven with natural yarn according to different design requirements, so as to obtain higher economic value and shorten the delivery cycle.
Generally speaking, yarn dyeing costs more than fabric dyeing. But because it has the advantage of fast delivery, it is easier to adapt to changes in popular colors. At the same time, it can meet the needs of small batches and multiple varieties. In addition, the yarn dyeing machine is relatively simple. Thus, it is more economical in terms of maintenance.
Yarn dyeing has a history of nearly a thousand years. Hank dyeing has been used for a long time. It was not until 1882 that the world had the first patent for cheese dyeing, and later beam dyeing appeared. This article introduces 3 different yarn dyeing methods and their advantages and disadvantages.
Contents
Hank yarn dyeing
Hank dyeing first requires the conversion of spun yarn or filament on a reel into a framed hank. Dip dyeing is then carried out in a hank dyeing machine. This is one of the most expensive dyeing methods.
Advantages of hank dyeing
- The hank dyeing equipment is simple and cheap, and can even be carried out with very simple pools. It can also be easily produced by manual methods without the need for power.
- When dyeing fluffy yarns or yarns with strong shrinkage, there is a leveling effect and a bulky feel that are difficult to achieve in cheese dyeing.
- The dyeing versatility is strong, and it is suitable for dyeing almost all yarns.
Disadvantages of hank yarn dyeing
- Hank dyeing requires a lot of loading and unloading processes, so it requires a lot of labor.
- The yarn payload is small, and the utilization rate of dyeing and chemical materials is low. Therefore, the production efficiency is low and the consumption of water, electricity and steam is high. This results in high production costs. In addition, environmental pollution is also very serious.
- The hank dyeing has an additional yarn shaking process, and the production process is long.
- When useing hank dyeing, the yarns are heavily intertwined with each other. In this way, the effect of the cloth surface will be poor due to the large number of joints, and the production efficiency of the subsequent process will be reduced. At the same time, there are many yarn hairiness, which causes the fabric surface to contaminate the fibers with each other, making the fabric surface feel unclean.
Cheese dyeing(yarn package dyeing)
There are some other names for cheese dyeing, such as package dyeing, bobbin dyeing or cone dyeing. Cheese dyeing has low loss, high quality, fast delivery and good benefits. As an important dyeing method, cheese dyeing has been adopted by the majority of yarn dyeing and finishing factories.
Here is the process of package dyeing. The spun yarn or filament is wound on a bobbin full of holes, and the winding density is required to be appropriate and uniform. Then put it on the dyeing column (also known as yarn bamboo, spindle rod, insert rod, etc.) of the yarn carrier (also known as flat plate, hanging tray, creel, etc.) of the dyeing machine, and put it into the cheese dyeing machine. With the function of the main pump, the dye liquor penetrates and circulates between the yarns or fibers in the package, so as to achieve the purpose of dyeing.
Advantages and disadvantages
Advantages: It has large dyeing processing capacity and small liquor ratio. Compared with hank yarn dyeing, cheese dyeing has the advantages of fewer production processes, no entanglement of yarns, high production efficiency, and less labor intensity. It is widely used in industrial production
Disadvantages: During the dyeing process, the cheese yarn is not easy to be dyed uniformly. There are also disadvantages such as high requirements for winding and large color difference between the inner and outer layers. The fluffy effect and softness are not as good as skein dyeing.
Beam dyeing
Yarn beam dyeing can be divided into beam dip dyeing and beam pad dyeing.
Beam dip dyeing
According to the requirements of the color and quantity of the warp yarns of the colored fabric, the original yarn is wound on the perforated coil on the loose warping machine to form a loose warp beam (which can be regarded as a large bobbin). It is then mounted on the yarn carrier of the dyeing machine and placed in the beam dyeing machine. By the action of the main pump, the dye liquor penetrates and circulates between the warp beam yarns or fibers to achieve dip dyeing. The method of obtaining warp yarns with uniform color is called beam dyeing.
Beam pad dyeing
Beam pad dyeing is mainly used in the production and processing of denim with color warp and white weft. It is to put a certain number of dilute shafts into each dyeing tank. And after repeated multi-dipping, multi-rolling, and repeated ventilation and oxidation, the dyeing of indigo (or vulcanization, reduction, direct, paint) dyes is realized. After pre-drying and then sizing, warp yarns with uniform color and luster can be obtained, which can be directly used for weaving. The dyeing tank in warp padding can be multiple (sheet machine) or one (ring machine), this equipment used in conjunction with sizing is called sheet dyeing and sizing machine.
Advantages and disadvantages
Advantages: Compared with cheese dyeing, warp beam dyeing can save dehydration, yarn drying, loosening and rewinding processes, thus saving a lot of manpower and material resources. In addition, the economic benefits of this yarn dyeing method are considerable. Not only that, the process is short, the speed is fast, the raw material is saved, the evenness of the cloth surface is good, and the cloth machine has less end breaks and high efficiency.
Disadvantages: At the same time, beam dyeing risk is also very high, the process is complicated, and there is little room for recovery from problems. In the production process, problems such as color flower and color difference often occur, which affect the production quality.
Leave a Reply
You must be logged in to post a comment.
Good. It solved my doubts about yarn dyeing classification for many years.
This is the perfect blog for everyone who would like to find out about this topic. You know a whole lot its almost hard to argue with you (not that I actually would want toÖHaHa). You definitely put a fresh spin on a subject which has been discussed for ages. Wonderful stuff, just excellent!
Perfect work you have done, this website is really cool with great information.