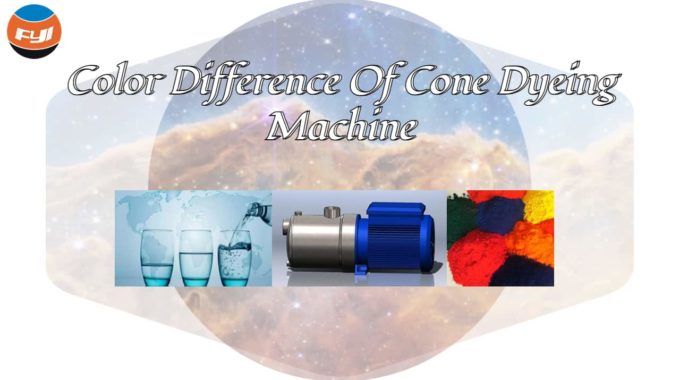
Color Difference of Cone Dyeing Machine
A cone dyeing machine is also called a package dyeing machine, a bobbin yarn dyeing machine or a cheese dyeing machine. When we introduced package dyeing before, we mentioned that there was a major flaw when dyeing with a cone dyeing machine. That is, the color difference between the inside and outside of the cheese is relatively large.
In this article, we will analyze the causes and prevention methods of the color difference between the inner and outer layers of the cheese yarn.
Contents
Manifestations of color difference
There are two cases of color difference of cone dyeing.
- The middle yarn and inner yarn have different shades of color.
- The different shades of color between inner yarn and outer yarn.
Discrimination method
Generally speaking, there are two ways to judge the color difference of the cone dyeing:
- Visually assess the degree of color difference between the inner and outer layers.
- Use a small knitting machine to knit the yarn into tubular fabric. That is, use inner, middle and outer yarns to knit together into a tubular fabric to see if the fabric has dyeing defects such as cross paths.
Causes and prevention methods of color difference of cone dyeing machine
Water quality
The water quality requirements for cone dyeing are:
- Chlorine content<0.05mg/L.
- Water hardness <25mg/L.
- The chromaticityof water <3 degrees.
- Iron content ≤ 0.1mg/L.
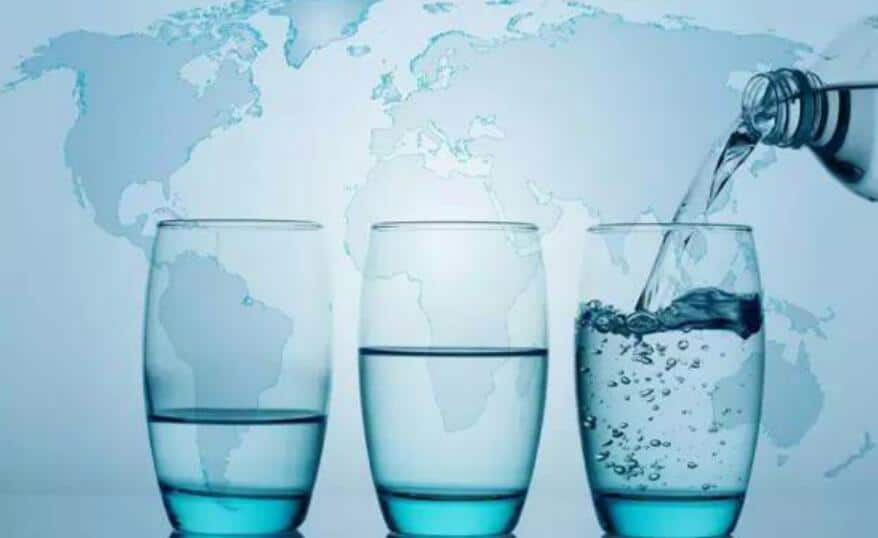
Chlorine content
If the chlorine content is high, the chlorine-sensitive reactive dyes will change color, forming different colors on the outer and inner layers of the cheese yarn.
The chromaticity of water
The chromaticity of water is an index to test the clarity and transparency of water. The higher the chromaticity, the worse the transparency of the water. Generally, water with high chroma will always contain some suspended solids and other particles. During dyeing, the cheese yarn is like a “filter”, which continuously filters the water.
Therefore, the chromaticity of water should be strictly controlled. Otherwise an adsorption layer will be formed on the inner and outer layers of the cheese yarn. And the impurities in the water will be adsorbed in this layer of yarn, so that it cannot be used in normal circulation. This often leads to the color difference between the inner and outer layers of the cheese.
Iron content
Iron content should also be controlled. If the content of Fe2+ and Fe3+ is too high, rust yellow circles will be formed at the places where the contact tightness between the two ends of the bleached yarn, the light-colored inner yarn and the cheese yarn is high. And it plays a catalytic role in oxygen bleaching, which is easy to cause partial over-bleaching and brittleness of the bobbin yarn.
Pump
Pump head and flow
When dyeing with a cone dyeing machine, the dye liquor needs to penetrate into the inner layer of the cheese by the head of the pump, and achieve a balance through the reciprocating circulation inside and outside. Therefore, the pump must have enough head and flow, and the head and flow of the pump can be adjusted by the dye liquor bypass valve.
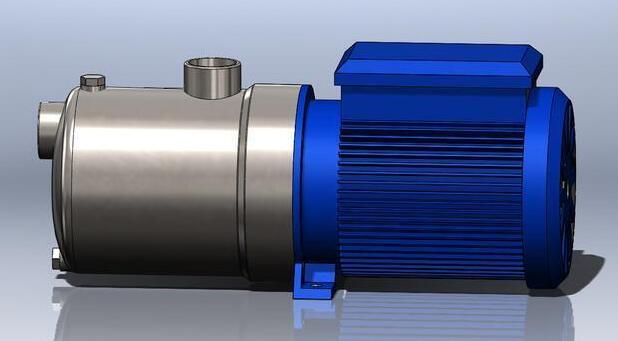
If the lift and flow are too large, some short fibers in the yarn will come out of the yarn twist and float out, causing fluff or even breakage;
If the lift and flow rate are small, the dye liquor penetration will be poor, resulting in the phenomenon that the color of the middle layer of the cheese is lighter than that of the inner and outer layers.
After small sample and medium sample experiments, the required head and flow range can be initially measured. Generally, the flow rate of dyed cotton yarn is between 35 and 50L/(min.Kg), and the flow rate of dyed polyester-cotton blended yarn is between 30 and 40L (min.Kg).
Forward and reverse cycle time
The time ratio of the positive and negative circulation of the cheese in the dyeing process depends on the pump head and flow, and the type of yarn. Generally, the reverse cycle (outer→inner) time is longer than the positive cycle (inner→outer) time for package yarn.
If the color of the cheese yarn is light in the inner layer and dark in the outer layer, the positive circulation of the dye liquor should be increased;
If the color of the cheese is dark in the inner layer and light in the outer layer, the reverse cycle time should be increased.
Dye
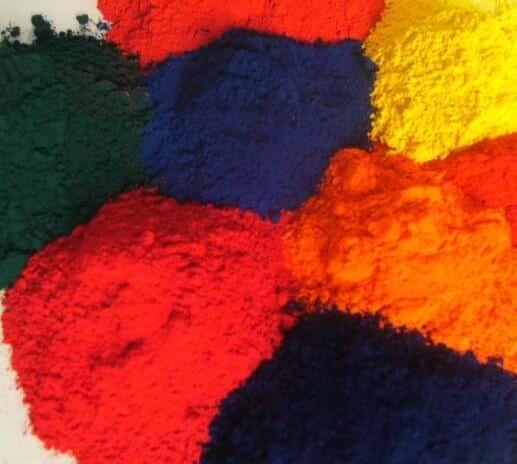
When dyeing polyester-cotton blended yarn and cotton yarn, the choice of dyestuff is the most important factor affecting the color difference between the inside and outside of the cheese. Due to the particularity of cone dyeing, the dyes used are required to have good permeability, excellent migration and dyeing fastness.
The following principles should be followed when combining colors:
- The adaptability of dyes to fibers.
- The dyes generally do not use the same type.
- The properties, directness, diffusivity and color fastness of dyes should be as consistent as possible.
If the selected dyes have good compatibility, synchronization and reproducibility, the inner and outer layers of the cheese can be dyed evenly.
The design of dyeing process
The dyeing process of polyester-cotton blended yarn (two-bath method) is:
Grey yarn → pre-shrinking (steaming) → winding → pre-treatment → dyeing and polyester → cleaning (reduction cleaning) → cotton dyeing → post-treatment → drying → yarn rewinding → weaving
Dyeing process of cotton yarn:
Grey yarn → winding → pre-treatment → cotton dyeing → post-treatment → drying → weaving
Pre-shrinking(steaming)
Pre-shrinking is to steam the package yarn at 130℃ for 30min before winding to untwist the yarn and achieve a certain retraction. The process of pre-shrinking is often ignored by many dyeing factories and not adopted.
Because synthetic fibers and their blended yarns have great shrinkage (about 5% to 10% shrinkage). If they are not pre-shrinked, they will have serious shrinkage when they are scouring with caustic soda and dyeing at high temperature. The inner yarn of the cheese yarn shrinks faster and tighter than the outer yarn. It is not easy to make the dye liquid penetrate evenly. Therefore, for polyester-cotton blended yarns, it is extremely important to do a good job of pre-shrinking. Cellulose fibers have almost no shrinkage during dyeing, so pre-shrinking is not required.
Package winding density
Yarns of different types of fibers should have a certain winding density during winding. And the winding density of different bobbins and the inner and outer layers of each bobbin should be uniform.
If the winding density of the package is too low, the shape of the package will be deformed; on the contrary, if the density is too high, the package will be tight and the penetration will be poor, resulting in impermeability. The winding density of the cone dyeing machine should be determined according to the pump head, flow rate and external pressure of the package yarn dyeing machine.
The winding density of the general package yarn is as follows:
Yarn Type | Winding Density (g/cm3) | Roll Hardness (%) |
Unmercerized cotton yarn | 0.3~0.4 | 30~20 |
Mercerized cotton yarn | 0.25~0.3 | 25~15 |
Polyester cotton blend | 0.3~0.4 | 30~20 |
Nylon yarn | 0.2~0.3 | 30~20 |
The finer the bobbin yarn, the smaller the winding density of the corresponding bobbin yarn should be.
Comments are closed.
I’ve read a few of the blog articles in your website and I really like your blogging style. I added it to my list of favorite websites and will be returning soon.
Two full thumbs up for this magneficent article of yours. I’ve really refreshing examining this article today and I figure this might be a champion among other article that I’ve scrutinized yet.
I’m extremely appreciative that I read this. It is incredibly beneficial and excellent in every way.
I found the color difference in my cone dyeing machine,too.