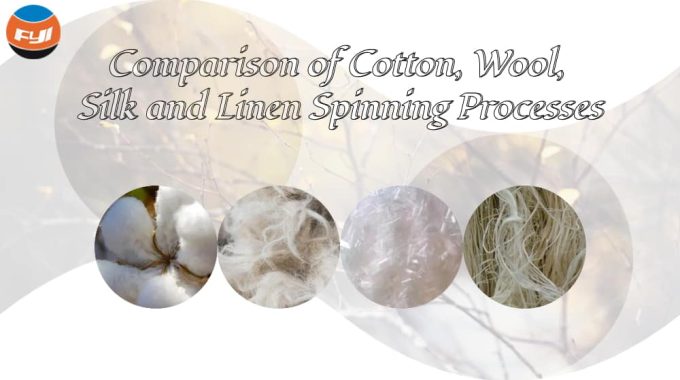
Comparison of Cotton, Wool, Silk and Linen Spinning Processes
Spinning, as an engineering technology, processes fiber aggregates, and its essence is the process of changing fibers from a chaotic state into an orderly arrangement in the longitudinal direction. Currently, the commonly used spinning raw materials are mainly natural fibers and chemical fibers. Natural fibers mainly include cotton, wool, silk, hemp and other fibers. The use of natural fibers for spinning has a long history.
Although cotton, wool, silk, and linen are all natural fibers, they have their own characteristics. Some fiber properties are very different, and the spinning performance is very different. It is difficult to use a unified processing method to make spun yarn. Below, we select four common natural short fibers: cotton, wool (hair), spun silk (silk), and ramie (hemp) to compare their spinning processes.
With the development of textile machinery and the improvement of spinning principles, special spinning systems for cotton spinning, wool spinning, silk spinning and linen spinning have been formed after long-term practice. Their technological processes are different.
Contents
Cotton spinning process
According to the performance of raw materials and product requirements, the cotton spinning process can be mainly divided into carding process, combing process and waste spinning process.
- Carding process
Raw cotton——Cotton blending——Opening and Cleaning/Blowrooming-Carding——Carding——Drawing——Roving——Spun yarn——Post-processing
- Combing process
Raw cotton——Cotton blending——Opening and Cleaning/Blowroom-carding ——Carding——Combing preparation——Combing——Drawing——Roving——Spun yarn——Post-processing
- Waste spinning process
Waste, yarn waste——Opening and Cleaning——Carding——Roving
Wool spinning process
According to different product quality requirements and processing techniques, the wool spinning process can be mainly divided into carded wool spinning system, combed wool spinning system, and semi-worsted wool spinning system.
- Carded wool spinning process
Raw wool——Primary processing——Optional wool——Combing wool——Wet and oiling——Carding——Spun yarn——Post-processing
- Worsted wool spinning process
Raw wool——Primary processing——Top manufacturing——Strip dyeing and recombing——Pre-spinning——Post-spinning
- Top manufacturing process flow
Combing wool——Wet and oiling——Wool carding——Gilling——Combing—— Gilling
- Strip dyeing and recombing process
Pine cones——Dyeing——Dehydration—Rewashing and drying——Mixing——Gilling ——Recombing——Gilling
- Semi-worsted wool spinning process
Combing wool——adding wet oil——carding——drawing——roving——spun yarn
Silk spinning process
The silk spinning process is relatively long. According to the floss making process, it can be divided into circular combing floss making and combing floss making.
- Silk spinning process
Silk spinning raw materials——Primary processing——Floss making——Spinning——Spun silk
- Circular combing floss making
Scoured waste silk——Wet——matching——Open——Cut——Round——Row——Stretch——Finishing
- Combing floss making
Scoured waste silk——Matching——Wet——Open——Roller comb——Rubber ring Drafting——Needle comb——Straight combing——Finishing
Linen spinning process
There are many types of hemp fiber. Currently, the more mature spinning systems include ramie spinning, flax spinning, etc. The ramie spinning process is as follows.
Raw linen——Initial processing——Opening——Carding——Combing preparation——Combing——Needle combing——Roving——Spun yarn——Post-processing
Analysis of four technical processes
From the above comparison, it can be found that the spinning process of cotton spinning is obviously shorter and less equipment is used in each process. In the wool spinning process, top manufacturing can also be sold as a separate finished top. For top dyeing products with high product quality requirements, it also needs to go through the strip dyeing and recombing process, that is, the top is dyed and combed again.
In the silk spinning process, the fine cotton obtained after initial processing needs to be made into fine cotton by circular combing or combing to obtain fine cotton and then spun. The circular combing cotton making process is long and labor-intensive, and the fine cotton produced has fewer grains. ; Combed cotton is similar to top manufacturing. Although the process is shorter, the quality is not as good as circular combing.
Ramie spinning generally uses a complete set of equipment from the combed wool spinning system for spinning, with only partial modifications to the equipment, and the process is similar to the cotton spinning process.
Analysis and comparison of primary processing of cotton, wool, silk and linen yarns
Seed cotton picked from cotton plants, wool sheared from sheep, scraps from the silk weaving industry, and hemp peeled from stems are the original state of natural fibers. These raw materials contain many different components and cannot be directly processed into yarn. Therefore, it is necessary to carry out preliminary processing of these raw materials to remove the spinning-impeding components in the fiber raw materials, increase the spinnability of these natural fibers, and make the fibers meet the spinning requirements. A comparison of the ingredients and initial processing methods of these raw materials is shown below.
Seed cotton | raw wool | silk | Raw hemp | |
Main ingredients | Cellulose, cottonseed, carbohydrates, lipids, pectin, ash, etc. | Protein, mutton fat, sheep sweat, sheep dung, grass thorns, stems and leaves, sand | Silk fibroin, sericin, pigment, wax, fat, inorganic matter | Cellulose, hemicellulose, pectin, lignin, wax, water soluble matter, ash |
Ingredients that hinder spinning | Cottonseed, sugar substances | various impurities | Sericin, various impurities | non-cellulosic gum |
Preliminary processing method | Ginning and desugaring | Mechanical and chemical combination | refine | Degumming |
Process flow | Saw tooth or top roller gin Spray anti-stick additive | Select, open, wash, dry (carbonization) | Pre-refining treatment refine Post-refining treatment | Two cooking methods Cook twice and practice once Boil twice and rinse once Boil twice, rinse once and boil once |
Preliminary products | Lint (raw cotton) | Wash hair | scoured waste silk | degummed ramie |
As can be seen from the above, these natural short fiber raw materials contain a lot of spinning-impeding components. The common point of the initial processing of short fibers is to remove these spinning-impeding components through a series of physical or chemical treatment methods to obtain spinning requirements. of primary processing products. Due to the different spinning-retardant components of various raw materials, different natural fibers require different initial processing techniques and methods.
The cotton seeds and sugar substances in seed cotton cannot be removed during fabric finishing and are the main components that hinder spinning. Cottonseed is the seed of the cotton plant and can be removed by mechanical blowing. According to the different forms of initial processing machines, it can be divided into two methods: saw-tooth gin and top roller gin. Cotton seeds and fibers are separated from each other through the action of top rollers and blades or saw teeth. For the sugar substances in seed cotton, biological or chemical methods can be used to remove sugar. Such as water spraying, steaming, washing, enzymatic and other methods to remove sugar. Currently, the method of spraying spunbond additives is commonly used.
Raw wool contains a lot of physiological inclusions and living environment debris, which seriously affects wool spinning processing. Raw wool is first selected, and then various impurities are removed through a series of mechanical and chemical methods such as opening, scouring, drying, and carbonization to obtain relatively pure scoured wool that meets the requirements of wool spinning production. Unhairing mainly uses the action of the hair opening cylinder to loosen the wool pieces into loose wool bundles, and remove as much impurities as possible; wool washing involves washing away lanolin, sheep sweat, plant impurities, etc. through emulsification or solvent methods. Obtain washed wool; drying wool is to dry the washed wool coming out of the water roller of the wool washing machine to control the moisture regain of the washed wool. For the initial processing of woolen wool, carbonization is also required. Carbonization uses the property that cellulose is not acid-resistant while wool is acid-resistant to remove plant-based impurities. It requires pickling, acid rolling, drying, carbon removal, neutralization and other processes to obtain carbonized washed wool.
Silk spinning raw materials come from a wide range of sources, and their main components are silk fibroin and sericin. Although both are proteins, only silk fibroin is suitable for spinning processing. A small amount of sericin can play a protective role, so the main purpose of refining is Most of the sericin, grease, dust and other impurities are removed to produce a clean, fluffy, dry cotton with a certain degree of rigidity and elasticity. Pre-refining treatment mainly involves sorting, loosening and removing impurities from raw materials to determine the refining method and process; Refining can be divided into chemical refining and biochemical refining according to the principle. Currently, the saponin refining method is often used; Post-refining treatment Including washing, dehydration and drying processes, the final product is made into scoured waste silk suitable for subsequent use.
Ramie is a hemp fiber that is widely used and has a complete spinning system. Raw hemp contains more non-cellulose colloids, which are mainly polysaccharide carbohydrates and aromatic compounds. The initial processing of raw hemp is the degumming of hemp fiber. There are currently two basic methods of degumming: chemical degumming and microbial degumming. The most commonly used method is chemical degumming, which is mainly based on alkali scouring. There are many process methods for chemical degumming. The two-boiling method has a short process, but the quality of the dried hemp produced is not high; the two-boiling and one-cooking method produces good-quality dried hemp but takes a long time; the two-boiling and one-blanching method produces a lower-quality dried hemp. Good, the process time is short; the quality of dried hemp produced by two boiling, one bleaching and one scouring is the best, but the process is long and the cost is high. During the production process, the process can be reasonably selected according to product needs.
Leave a Reply
You must be logged in to post a comment.
I wanted to keep reading more and more, as each paragraph revealed a new layer of knowledge and understanding.
Most articles I come across merely scratch the surface, but this one delves deep into the heart of the matter.
I find it hard to believe that one person could possess such a wealth of knowledge on the subject matter.
I was blown away by the author’s ability to take a seemingly mundane topic and turn it into a fascinating read.
Find yourself coming back to this blog time and time again for its fresh perspectives and thought-provoking insights.