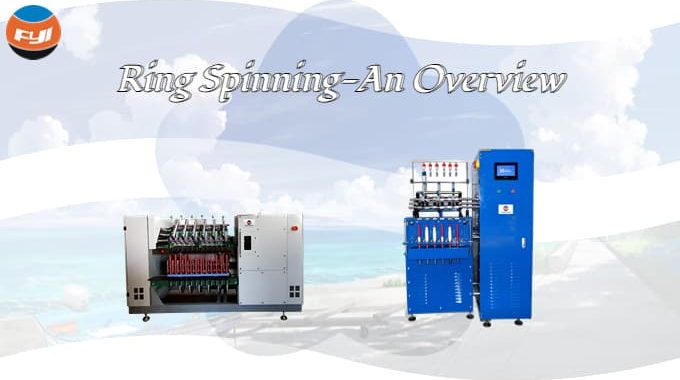
Ring Spinning-An Overview
Ring spinning is a mechanical spinning method in which the spindle, the steel ring, and the traveler are twisted, and the rollers are used for drafting.
Contents
Introduction
Ring spinning is currently the most widely used spinning method in the market. The drafted slivers or roving are drawn in through the ring traveler, the bobbin is wound faster than the traveler, and the cotton yarn is twisted into a spun yarn.
Widely used in the spinning of various short fibers. Such as carding, combing and blending, the traveler is driven by the bobbin through the yarn sliver to rotate around the steel ring. Twisting, at the same time, the friction of the steel ring makes the rotation speed slightly smaller than the bobbin to be wound. The spinning speed is high, and the shape of the ring-spun yarn is a conical helix with fibers mostly transferred from inside to outside, so that the fibers are wound and connected inside and outside the yarn. The yarn has a compact structure and high strength.
Ring spinning process
Combed
Blowing room—carding——pre-drawing——strips and coiling——combing——first drawing——secondary drawing——roving——spun yarn——winding
Carding
Blowing room——carding——first drawing frame——secondary drawing frame——roving——spun yarn——winding
The difference between ring spinning and air spinning
Yarn forming mechanism
Ring spinning belongs to grip spinning, which is a spinning method that simultaneously carries out drafting, twisting and winding. The roving is drawn to the required yarn count in the drafting system, and then twisted and wound by the steel ring and the traveler to form a yarn. The sliver has no break point throughout the yarn forming process.
Open-end spinning belongs to open-end spinning. The slivers are carded into single fibers by the carding roller. Under the action of the centrifugal force of the carding roller and the negative pressure airflow in the rotor, the fibers leave the surface of the carding roller and enter the rotor through the cotton conveying pipe, and form a fiber ring in the condensation groove. The fiber ring rotates at a high speed with the rotor, and under the action of the joint yarn, the twist is continuously transmitted and the fiber bundle is continuously stripped to form a yarn. There are break points in the yarn forming process of the strands.
Twisting method
Ring spinning twisting is held at both ends, and air spinning twisting is held at one end.
Process flow
After the mature sliver is formed by ring spinning, it is necessary to further form a roving, which can be produced directly from the cooked sliver by air spinning. After the ring spinning yarn is formed, it is generally necessary to further wind the yarn into a package, and the air spinning can directly form a package.
Yarn structure
Spindle spinning is done with both ends held in place due to drafting and twisting. Therefore, the fibers in the yarn are relatively straight. And since the fibers on the outside of the triangular region receive the greatest tension during twisting, the fibers in the center receive the least tension. Therefore, the initial tension of these fibers varies during yarn formation, so that the outer layer fibers tightly wrap around the inner layer fibers, and the yarn is relatively tight.
In air spinning, fiber separation and twisting are all done in a free state, and during the process of yarn drawing and twisting, fibers continue to slide along the wall of the condensation tank to the stripping point, so more fibers in the coating layer are formed, the fiber orientation is poor, and the yarn is fluffy.
Appearance of the yarn
The single fibers on the surface of the ring-spun yarn basically follow the twist direction, which is relatively neat, and there is little fiber entanglement in the reverse twist direction.
The single fiber on the surface of the air-end yarn has more anti-twist fiber entanglements, so the ring-spun yarn is easy to untwist, and the air-end yarn is not easy to untwist.
Yarn Requirements for Raw Materials
Due to the difference in yarn forming mechanism between air spinning and ring spinning, ring spinning generally has a relatively high yarn count, while air spinning has a relatively low yarn count. Air spinning can use shorter raw materials, while ring spinning generally requires longer raw materials.
Advantages and application scope of ring spinning technology
Ring spinning is the oldest spinning system, at least in concept, but the technology is not old. Modern ring spinning machines feature automation, require far less labor than in the past, and produce higher quality. The yarn produced by the ring spinning machine provides the standard for products produced by other systems.
High production efficiency
The production efficiency of ring spinning equipment is high, and the spun yarn is smooth, bright and high in strength, which is suitable for the production of various textiles.
Good yarn quality
Compared with other spinning methods, the yarn surface of ring spinning is smooth, without defects such as hairiness and impurities, and the yarn quality is good, which is suitable for the production of high-end clothing.
Low production cost
Ring spinning requires less equipment and lower production cost.
Disadvantage of ring spinning
Limited by traveler speed
Excessive speed of the traveler will cause severe friction, heat and burns, frequent replacement of the traveler and increased end breaks
Limited by balloon tension
As the spindle speed increases, the air resistance and inertial centrifugal force on the balloon will increase accordingly, resulting in more broken ends
Limited by ring diameter
The increase of the spindle speed will increase the time of doffing and changing the package during shutdown, which will reduce the utilization rate of the equipment, and the diameter of the steel ring will increase when the package tends to be large, which will increase the line speed of the traveler and accelerate wear
Limited by spindle load
If the spindle speed is increased, if the utilization rate of the equipment is not reduced, a large package must be used, but the large package will increase the load on the spindle, and the greater the load, the greater the vibration, and it will consume more power, which will affect the economic benefits of production.
Comments are closed.
Such a well-structured and organized article. It’s a pleasure to read.
A captivating introduction sets the tone for this insightful and well-researched blog entry.
I can confidently say that this blog has become my go-to resource for reliable information.