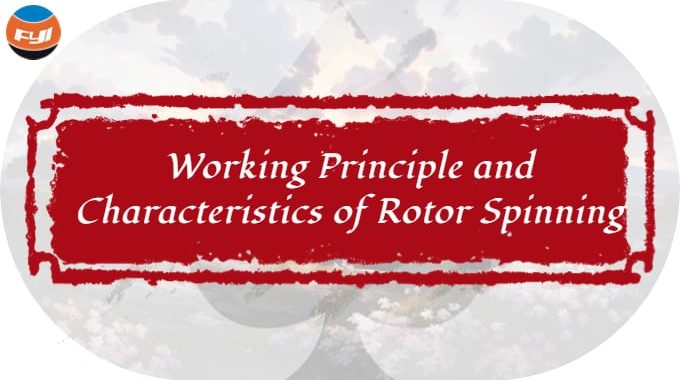
Working Principle and Characteristics of Rotor Spinning
Contents
Rotor spinning working principle
Rotor spinning is a new spinning methods, this spinning method belongs to the category of open-end spinning. Rotor spinning does not use spindles, mainly relying on opening roller, rotor, false twisting device and other components. The opening roller is used to grasp and opening the fibers fed by the feed roller, and the centrifugal force generated by its high-speed rotation can transport the fibers out. The rotor’s rotation speed is more than 10 times higher than the opening roller. According to the principle of fluid pressure, cotton fibers enter the rotor along with the air flow and form a fiber flow, and constantly flow along the inner wall of the rotor. At this time, insert a yarn from the draw-off tube into the rotor, the fibers on the rotor inner wall are drawn out and twisted by the rotor rotating, as if while feeding the fiber constantly, while twisting, so that the yarn is connected with the fiber of the rotor inner wall. The spinning yarn is drawn out and wound onto the yarn tube by the yarn drawing winding mechanism. Rotor spinning makes twisting and winding process separately, which can solve the contradiction between high speed and large winding. It can increase the output of yarn exponentially.
Materials used in rotor spinning
The rotor spinning machine suitable variety raw materials, such as:
Cotton
Cotton waste and noil
Recycled fibers
Short staple of wool, linen, and silk
Chemical fibers
Blends of cotton and man-made fibers
and so on.
The main parts of rotor spinning machine
Feed roller and feed plate
Feed roller and feed plate clamp the sliver and feed the sliver into the opening roller. The feed roller speed can be adjusted according to spinning process.
Opening roller
The opening roller is to decompose the sliver into a single fiber state, and at the same time to remove fine impurities in the sliver, so as to achieve the purpose of improving strength and reducing the broken head. The opening roller generally adopts aluminum alloy tire base, the surface is planted with steel needles or toothed pieces, and combined or coated with metal card clothing, the diameter is about 60-80mm, its function is mainly to opening the sliver that hold by feed roller and feed plate, to achieve the fiber in the single fiber state of transportation, for the fiber rearrangement and combination preparation.
Rotor
Rotor is the key element of rotor spinning. The inner wall of the rotor is called the slip surface, and the largest diameter is the coagulation trough. The centrifugal force generated by the high-speed rotation of the rotor plays the role of agglomerating fibers. Relying on the action of air flow and centrifugal force, the single fiber after opening slides from the sliding surface of the cup into the coagulation trough to form a ring-shaped free end bard, and every rotation of the rotor run, a twist is generated on the yarn (if the twisting efficiency is not counted).
Its function is to enhance the twist of the fiber buddle in the condenser of the rotor coagulation trough, strengthen the stripping ability, and reduce the twist and the breakage of rotor spinning yarn.
Delivery rollers
The yarn formed in the rotor is continuously taken off by the delivery roller through the nozzle and the draw-off tube and wound onto a cross-wound package. The stretch is also completed in this process.
Temperature and humidity requirement
Workshop temperature and humidity have a direct impact on production. Temperature and humidity should be adjusted according to the season and variety. In general, the workshop temperature is controlled at about 23 °C, and the relative humidity is about 60%. If the temperature of the workshop is too high (low relative humidity), the broken heads number increases, the yarn evenness and strength is low, and the formation is bad. If the temperature of the workshop is too low (high relative humidity): the broken heads number and thick knots increase, the yarn evenness and strength is low, and the formation is also bad.
Workshop temperature and humidity control range (for reference)
Winter season: Temperature ≥20℃, humidity:60%-70%;
Summer season: Temperature ≤30℃, humidity:60%-70%;
The characteristics of rotor spinning yarn
Strength
There are many bending, folding and winding fibers in rotor spinning process, and the internal and external transfer of the fiber is poor, when the yarn is subjected to external force, the rotor spinning yarn strength is lower than the ring spindle yarn. The main reasons are as below: the fibers breaking are not in isochronism, and the contact length between the fibers is short, the probability of slip-off increases.
Yarn evenness and impurities
The rotor spinning yarn is formed in the rotor, it avoid roller drafting and mechanical waves, and during the condensation process, it get a merging effect, these factors make the rotor spinning yarn evenness is good than the ring spindle yarn.
The sliver is opened into individual fibers and the impurities in the fibers is exhausted before the fiber transferred into the rotor, so the rotor spining yarn is relatively clean, and the yarn defects are few and small.
Wear resistance
The yarn wear resistance is not only related to itself uniformity, but also closely related to the yarn structure. The ring spinning yarn fiber is a regular spiral, when subjected to repeated friction, the spiral fiber gradually becomes axial fiber, and the whole yarn is quickly worn off due to loss of twist disintegration. The rotor spinning yarn is covered with irregular winding fibers, so it is not easy to disintegrate and thus performance better wear resistance than ring spinning yarn.
Twist
The twist of the general rotor spinning yarn is about 20% more than the ring spindle yarn, which will cause difficulties in some post-processing (such as the processing of pile fabric), and the twist is large, the yarn feels hard, which affects the feel of the fabric. Therefore, it is necessary to research measures to reduce the twist of the rotor spinning yarn under the premise of ensuring a certain single yarn strength and breaking.
Elasticity
Spinning tension and twist are the main factors affecting yarn elasticity. Generally, the spinning tension is large and the yarn elasticity is poor. Because the spinning tension is large, the fiber is easy to exceed the elastic deformation range, and the fiber in the yarn is difficult to slide after yarn, so the elasticity is poor. Large twist gets good elasticity. Because the yarn twist is large, the fiber inclination angle is large, and when stretched, it shows spring-like elongation, so the elasticity is good. The rotor spinning yarn is a low-tension spinning yarn, and the twist is more than the ring spindle yarn, so its elasticity is better than the ring spindle yarn.
Fluffiness
The fluffiness of the yarn is expressed by the specific volume (cm3/g). Due to the poor straightness of the fibers in the rotor spinning yarn, and the irregular arrangement, the tension of the yarn during the twisting process is small, and the outer layer is wrapped with winding fibers, so the structure of the rotor spinning yarn is fluffy.
Dyeing property and sizing absorption
Due to the fluffy structure of the rotor spinning yarn, and therefore strong water absorption, so the dyeing property and sizing absorption of the rotor spinning yarn is better.
Comments are closed.
This article tackles a complex topic with ease and clarity.
The author’s storytelling ability shines through in this captivating and educational blog post.
One cannot help but be impressed by the depth of knowledge demonstrated by the author in this blog.
All I can say is that reading this article was a truly enlightening experience – it broadened my horizons.