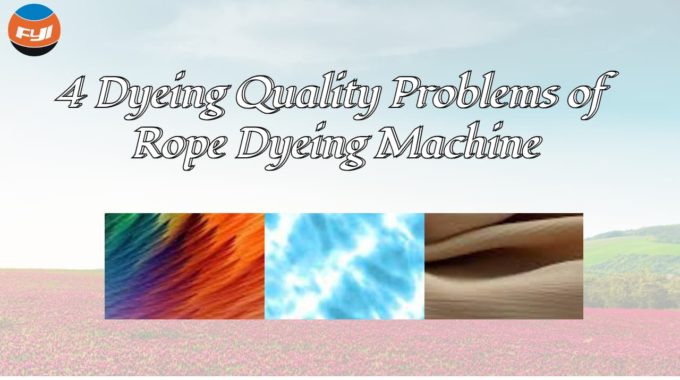
4 Dyeing Quality Issues with Rope Dyeing Machine
Rope dyeing machine, also known as rope dip dyeing machine. It is a type of equipment for interweaving thin silk, wool, cotton, and chemical fiber materials with loose, normal temperature rope dip dyeing. It is appropriate for many textile printing and dyeing operations, including loose rope scouring, dyeing, washing, and others. (An additional rope dyeing machine utilized in the denim facility will not be included in this article.)
Contents
Types of rope dyeing machine
Wool, silk, cotton, and their mixed knitted textiles, as well as chemical fiber imitation fabrics that are unsuitable for tension and pressing, are the major materials rope dyeing machines are used for.
Additionally, it may be used to scrub, bleach, soap, and wash various silk, cotton, and cotton-blend knit materials. This is due to the elongation, chafing, and loosening that certain textiles are prone to. Dyeing and processing machinery should meet the special requirements of these fabrics with low tension and low friction.
there are several sorts and variations of this apparatus. Ordinarily, there are four types of the dyeing equipment
At present, there are several sorts and variations of this apparatus. Ordinarily, there are four types of the dyeing equipment:
- Normal temperature and normal pressure rope dyeing machines.
- Normal temperature and normal pressure overflow dyeing machines.
- High temperature and high pressure overflow dyeing machines.
- Jet dyeing machines.
Dyeing Quality Issues
Knitted fabrics are pre-treated, colored, and finished mostly in rope dyeing machines. The brief duration of this process is one of its distinguishing features. In a tubular shape, the knitted cloth can be directly pre-treated and coloured. During the processing, the tension on the fabric is minimal. And the rope dyed knitted fabric has a nice feel to it.
However, because of the influence of the dyeing process and the structural characteristics of the rope dyeing machine itself, this type of method will also have dyeing quality issues. Dyelot chromatism, tube difference, stripes, and wrinkles are some examples.
1.Dyelot chromatism
Rope dyeing of knitted materials mostly use batch dyeing equipment, which are appropriate for small batches and a wide range of colors. Unlike the continuous dyeing machine, the batch dyeing machine has a restricted one-time cloth capacity. If the capacity of a single machine is exceeded by a batch of the same dyed fabric, it will be dyed in different cylinders or batches.
Dyelot chromatism will occur even if the same tank is dyed in batches or the same dyeing procedure is completed in different tanks of the same model. The reason for this is that the conditions of use differ. Differences in water, steam, electricity, and industrial operations are examples. And the equipment operation circumstances of multiple machines at different periods or different machines all at once. Even the features of different main circulation pumps of the same type, as well as the production and performance of components, may differ.
Of course, in actual applications, the dyelot chromatism generated by this reason must be kept within an invisible to the naked sight range.
As a result, in order to eliminate the influencing elements in this regard, the present knitted fabric rope dyeing machine is trending toward a multi-tube or multi-dyeing tank design. The dyelot chromatism exists whether in the same tank or in other tanks of the same model.
However, in actual applications, separate cylinder dyeing (finger colouring the same fabric) is unavoidable; instead, investigate how to better manage the dyelot chromatism within the permissible range.
The dyelot chromatism can be regulated within the prescribed range if the reasonable dyeing process and the specified operation technique are combined with a dyeing machine with good structural performance and sophisticated control, and the entire dyeing process is fully automatic controlled.
2.Tube difference
The batch rope dyeing machine connects the rope textiles end to end in a loop for periodic cycle operation. Because the average residence duration in a tube (trough) is 2-3 minutes, the length of the fabric in a tube (trough) is restricted.
Multiple tubes (trough) are frequently utilized for dyeing in the same bath to improve the fabric capacity of a single machine.
The one-time cloth capacity of the multi-tube (trough) dyeing machine has been increased. According to the batch size of the dyed fabrics, it can be placed in a dyeing machine with a basic corresponding capacity, and the dyeing process can be completed at one time as much as possible, so as to avoid the appearance of dyelot chromatism.
However, if the multi-tube (trough) dyeing machine is improperly operated or the structure and performance of the equipment are affected, tube difference will also occur.
There are several causes for the tube discrepancy, which can be summarized as follows:
Equipment shape and structure size
To guarantee that the fabric in each tube (trough) follows the same flowing route, the nozzle (or overflow), cloth guide tube, cloth storage tank, and other forms and structural specifications of each tube must be the same; otherwise, tube variances will occur.
The flow and pressure of circulating dye liquor
The flow and pressure of the circulating dye liquid are not consistent in the nozzles or overflow ports of each pipe. This relates to the structural design of the dye liquor’s main distribution conduit, as well as the flow rate and head of the main circulation pump.
The length of the cloth
The length variation between each tube (slot) carrying cloth is too great, resulting in irregular contact frequency between each tube of fabric and dye solution. At the same cloth speed and nozzle pressure, the color of the small capacity tube is darker, while the color of the big capacity tube is lighter. In general, the length variation between each pipe cloth should not be more than 5%.
Nozzle pressure and line speed of cloth lifting roller
The nozzle pressure of each tube and the linear speed of the cloth lifting roller are uneven, resulting in the same fabric length and contact frequency as the dye fluid cannot be attained.
Cloth blocking
Cloth blocking happens during the dyeing process, particularly at high temperatures where the dying is quick. In addition to the tube difference, the blocked tube may have chromatic aberration. To reduce the phenomena of cloth blocking, it should run at a low pace after the cloth has been fed, and then gradually raise the needed line speed after the fabric flows smoothly. The linear speed of the knitted fabric should be no more than 300m/min.
3.Stripes
Knitted fabric stripes are classified as weft (crosspiece) or warp (longitudinal). Warp stripes are common in pure cotton knitted textiles. This is because the weft-knitted tubular fabric is not blown open as it exits the guiding roller. And the stripes appear in areas that have not been opened and folded in a long time. Another issue is that the nozzle aperture is too tiny, causing the fabric to be excessively tight when passed through in a bundle. As a result, the cross-sectional area of the rope-like knitted fabric should ideally not exceed two-thirds of the nozzle diameter.
Weft and warp stripes appear on polyester knitted garments. The reasons are not only related to cylindrical expansion and nozzle diameter, but also due to structural tensions created during the weaving process. This structural tension is released during initial wet work at a certain temperature. If the pretreatment is rope-like, it produces weft or warp prints. And there will be streaks during the coloring process.
As a result, real experience demonstrates this. When using the open width pretreatment as the initial wet treatment. It has the ability to completely relax the structural tension of retracting knitted materials, preventing stripes during rope dyeing. In most cases, this procedure may be carried out concurrently with refining.
4.Wrinkles
Rope dyeing wrinkles in knitted materials appear on occasion.
Wrinkles are classified as either transient or permanent. Tentering can remove temporary wrinkles, however persistent wrinkles cannot be removed even after tentering. The wrinkle markings discussed here are mostly permanent wrinkles.
Wrinkles are caused primarily by the following factors:
Cool down too fast
The common chemical fiber knitted textiles are above the glass transition temperature when the fixing procedure is done. In the dye tank, the rope textiles are stacked irregularly. If the temperature drops too quickly at this time, the cloth will get chilly, fixing the stacking folds and forming permanent creases.
The cloth is blocked and knotted
The cloth becomes blocked and knotted during the dyeing or fixing process and cannot be used. It must be cooled and halted to be removed, and wrinkles grow quickly at the knots during this period.
The fabric is loaded excessively
The rope dyeing machine’s cloth capacity refers to the maximum fabric capacity of a certain gram weight. It is often made of medium-thick materials. In practical applications, the particular loading must be established based on the fabric’s actual grammage.
Fabrics with a maximum cloth capacity greater than the reference gram weight can surpass the nominal cloth capacity. Fabrics having a weight less than the benchmark should have a maximum cloth capacity less than the nominal cloth capacity. This is because a cloth with a length shorter than the specified grammage is too lengthy. It is possible to produce creases if it stays in the groove for too long (more than 3mim).
This blog is reproduced from 4 Dyeing Quality Problems of Rope Dyeing Machine.
Comments are closed.
You have done a amazing job with you website
It’s clear that you put a lot of thought and research into each and every one of your blog posts.
A must-read for both enthusiasts and experts in the field.