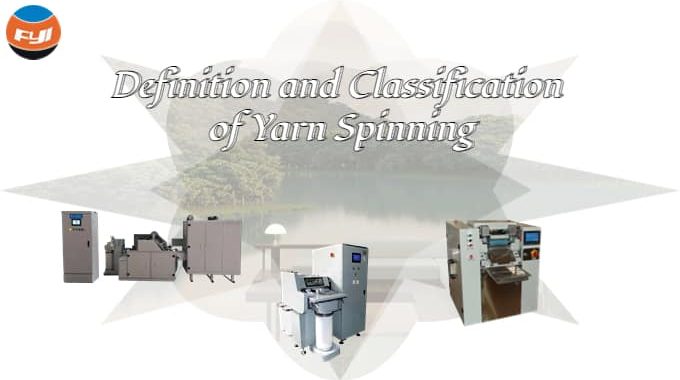
Definition and Classification of Yarn Spinning
What is yarn spinning
Yarn spinning is the technique of making yarn from fibers. The fibers can be wool, cotton or other natural materials, or they can be synthetic. Spinning produces a yarn that can then be used to make fabric.
Types of yarn spinning
Spinning can take numerous forms, but they all have the same goal: to transform fibers into yarn. Some varieties of spinning are more popular than others, but each has its own set of benefits.
Woolen and cotton are the two most common forms of spinning. The process of converting raw wool into yarn is known as spinning. The yarn is generally thick and heavy since it is spun on a spinning wheel. Cotton spinning is the transformation of raw cotton into yarn. The yarn is generally thin and light, and it is spun on a spinning wheel or spinning jenny.
There are also additional styles of spinning that are less common but have their own advantages. The process of converting raw silk into yarn is known as silk spinning. The yarn is generally very thin and delicate since it is spun on a spinning wheel. The process of spinning raw hemp into yarn is known as hemp spinning. The yarn is generally exceedingly fine and robust since it is spun on a spinning wheel. There are also chemical fiber spinning such as wet spinning and melt spinning, which will be introduced in the future.
Cotton spinning
Cotton fibers
The production of cotton fibers is the largest in natural fibers. And they are very versatile. We can use it for sewing clothes, sheets, bedding and other articles of life. It can also be used as canvas and conveyor belt materials. Or we can make it into floc for heat preservation and filler materials.
Cotton fibers are divided into fine cotton and long staple cotton. Compared with fine wool cotton, long wool cotton is whiter, finer, longer and shinier. It is the best cotton variety and is generally used for high-grade fabrics.
Cotton spinning system
The raw materials used in cotton spinning production include cotton fiber and cotton-type chemical fiber, and its products include pure cotton yarn, purified fiber yarn and various blended yarns. In the cotton spinning system, according to the raw material quality and yarn quality requirements, it is divided into carding system, combing system and waste spinning system.
Typically used for spinning coarse and medium special yarns, as well as weaving regular textiles.
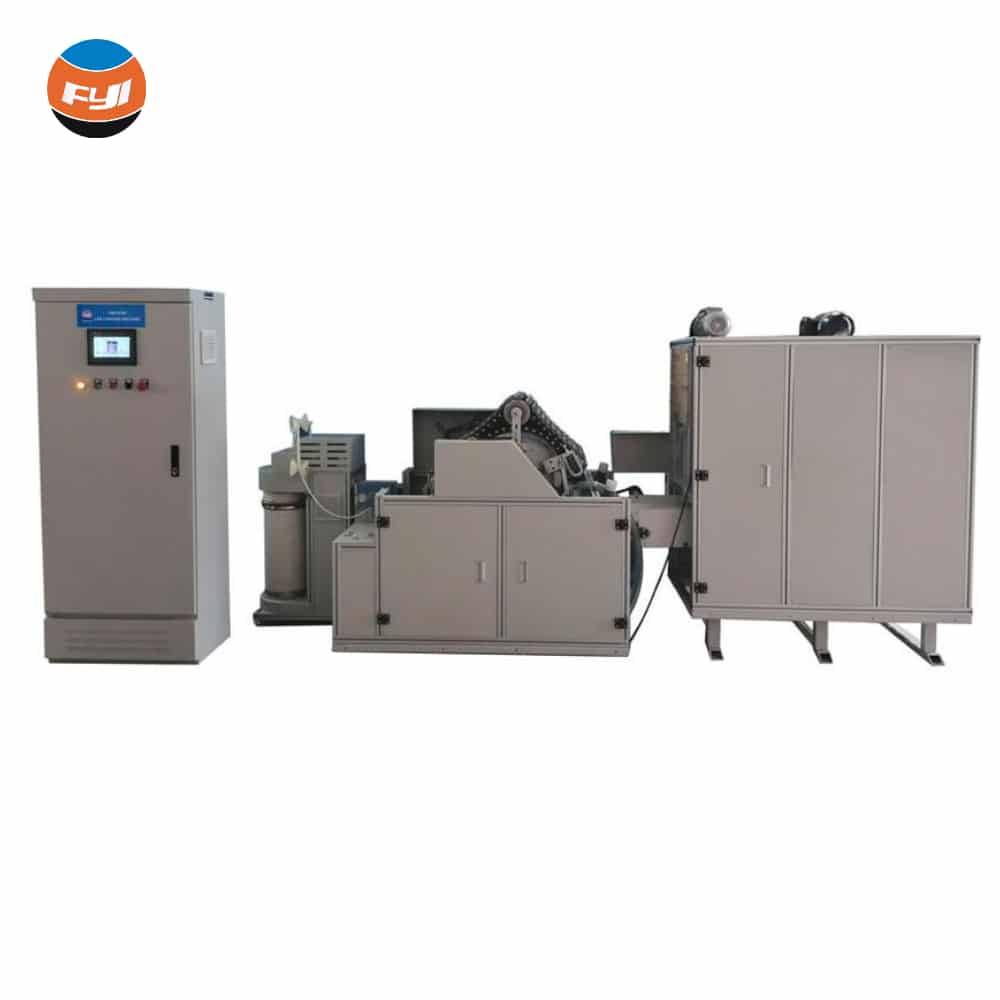
The combing technique is used to produce high-quality cotton yarn, unique yarn, and cotton and chemical fiber mixed yarn.
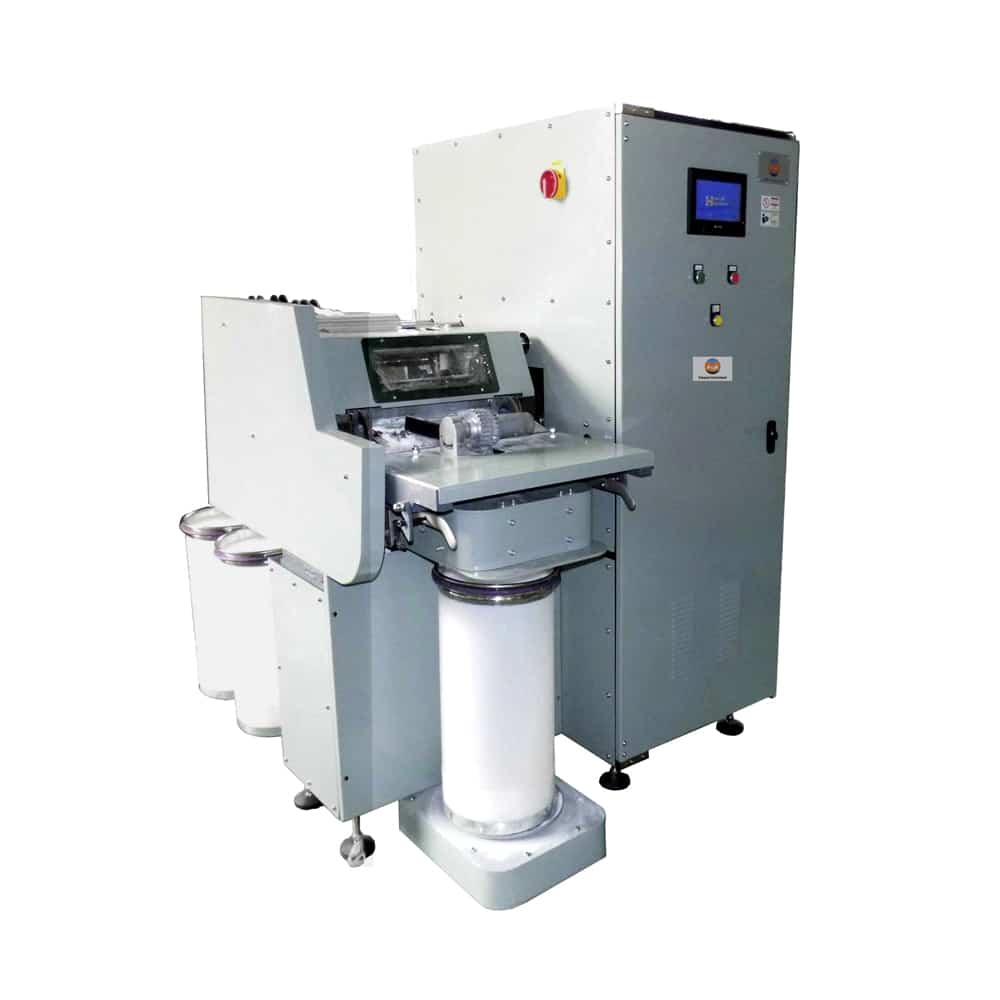
- Waste spinning system
Waste spinning systems are used to manufacture low-cost coarse cotton yarns.
- Cotton and chemical fiber blending system
Because of the differences in the characteristics and impurity level of polyester and cotton fibers, they cannot be combined and processed in the cleaning and carding process when blended. To guarantee proper mixing, use three draws while combining on top.
The cotton spinning process begins with harvesting the cotton plants. The cotton is then washed and sorted by size. The cotton is then put into the spinning machine. Spinning machines twist cotton fibers together to make cotton yarn.
Wool spinning
Wool fibers
Wool is a traditional natural fiber with unique properties, which cannot be replaced by synthetic fibers and has many ideal uses. Wool fiber properties show that wool is a versatile fiber that can be processed into fibers of different colors and fineness grades, such as paint rollers, mattress pads, blankets, outerwear, gear cloth, high fashion, carpets, curtains, screens, ski wear and tennis covers etc.
Advantages
1. Wool fiber has inherent heat and cold insulation capabilities, as well as the ability to absorb water and steam. Wool goods have a natural insulating effect due to the presence of air between the curled wool strands. It can absorb 30% of its own weight growth until it feels wet, and after absorbing moisture, the fiber creates heat. As a result, when wool fibers are worn on the human body, they feel warm and dry rather than chilly and sticky.
2. When wool absorbs moisture from the air, it tends to block liquid penetration. The liquid on the surface of the wool fibers will roll off the cloth, assisting in dust resistance. It may also keep the cloth looking younger for a long period. If the wool garment is done, it will be returned to its original shape.
3. Wool is a pretty big industrial raw material used in the fashion industry. It is antistatic, easy to sew, has an excellent drape resistance to dust, is easy to dye, quick to iron, and has a nice form. And it can keep people cool in hot weather and warm in cold weather.
Disadvantages
1. The wool fabric feels thick and tingly against the skin. The weight of wool textiles is determined by the yarn count, but because wool yarns are typically used to enable smooth further processing, lighter fabrics are difficult to achieve, which is why wool fibers cannot be utilized in various industries.
2 Hairiness is a significant issue in wool yarns, impacting the wool combed textile business. Wool yarn hairiness was discovered as a characteristic of wool yarn as early as 1950. The detection of yarn hairiness is accomplished by counting the number of hairs within a specific distance on the yarn body. Yarn hairiness is messy and disorderly on the yarn body, and there are also protruding fiber tails or head ends, fiber loops, etc. In ring spinning, most of the hairiness is protruding from the end of the yarn body.
Wool spinning system
The wool spinning system uses wool fiber and wool-type chemical fiber as raw materials, and the whole production process of spinning wool yarn, wool and chemical fiber blended yarn and pure chemical fiber spinning on wool spinning equipment.
(1) Carded wool spinning system
(2) Worsted wool spinning system
The worsted wool spinning system has many procedures and a long process, which can be divided into two parts: sliver making and spinning.
Combed sliver production is also called wool top manufacturing. A separate factory can be set up, and the product (combed wool top) can be sold as a commodity.
Some worsted wool spinning mills do not have a sliver-making process, and use combed wool sliver as raw material. The production process includes pre-spinning and post-spinning; The second combing after dyeing, the combing process flow is similar to the sliver making process. In addition, there is also a semi-worsted spinning process system between combed and carded.
Comments are closed.
Thank you very much for providing information.
That is one of the most well-researched and comprehensive articles I have read on the topic.
All the articles on this blog are well-researched and informative, making it a reliable source.
With so much noise on the internet, this blog is a beacon of clarity and authenticity.