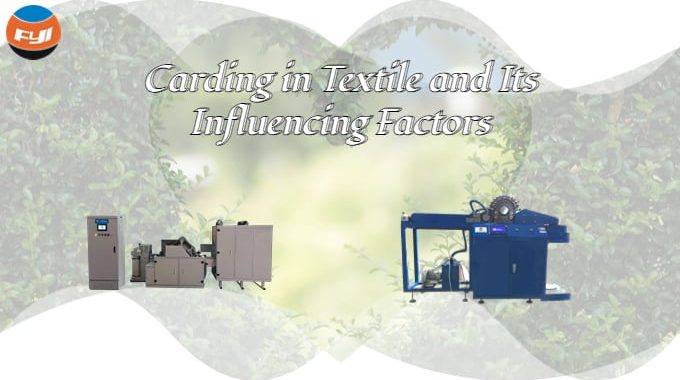
Carding in Textile and Its Influencing Factors
The essence of spinning is to ensure that the fibers are arranged in an orderly manner along the axial direction. To accomplish this task, carding in textile is the foundation and key. The main task of carding is to decompose the cotton bundle into single fibers and preliminarily complete the work of fiber orientation, while removing nep impurities and some short fibers. Below we will summarize the factors that affect the quality of carding, and conduct a simple analysis.
Contents
Raw cotton
The main factors affecting the carding quality of raw cotton are fiber maturity, fineness, micronaire value, cotton linters rate, and the number and content of defects in raw cotton.
Maturity of cotton fiber
Maturity is a comprehensive index to evaluate the intrinsic quality of cotton fiber. It directly affects the color, strength, fineness, natural twist, elasticity, moisture absorption, dyeing and other properties of cotton fiber.
Mature cotton fibers have many natural twists, good elasticity, and good color. It is not easy to form neps and short fibers during the carding process. After carding, the separation, straightness, and parallelism of the fibers are better.
When the maturity is poor, the fineness is fine, the strength is poor, and the length is long, it is more difficult to process in carding. At this time, the distance between the cotton board and the stabbing stick and the distance between the main carding area should be appropriately enlarged, and the speed should be reduced.
The fineness of cotton fiber
Fibers with normal maturity and finer fineness are soft and elastic to the touch, with good fiber cohesion and high strength. Under the same quantitative conditions, the number of fibers is large, easy to be held by the needle teeth, and the carding force is relatively large. If the fiber is not mature enough, although the fiber is thin, the elasticity is poor, and short fibers and neps are easily formed during the carding process, which affects the carding quality.
Effect of raw cotton length
The length of fiber in raw cotton is not only an important index to measure the quality of raw cotton, but also an important factor to determine the quality of yarn. The early theory believed that the length of cotton fiber is positively correlated with the yarn quality, that is, the longer the fiber length, the better the yarn quality. But with further research, a different view was put forward, that is, the fiber length is positively correlated with the strength quality index of the yarn, but not with the unevenness index of the yarn. When the fiber length is between 2 and 4 cm, the unevenness of the yarn increases to a certain extent with the increase of the fiber length, and its growth rate is closely related to the yarn count. Of course, this is the conclusion calculated by the theoretical model, and whether it is in line with the actual production needs to be verified by the production practice, but it also shows that the influence of the length of the fiber on the quality of the yarn cannot be ignored.
The influence of the uniformity of raw cotton
The fiber uniformity of raw cotton is the key factor affecting the carding machine sliver and yarn quality. Raw materials with high fiber uniformity will have significantly better raw sliver and yarn unevenness CV values than raw materials with poor fiber uniformity. For example, at present, the Uster evenness CV value of pure cotton card sliver is generally around 3.5%, while the Uster evenness CV value of chemical fiber card sliver is generally around 2.8%. One of the important factors is that the fiber regularity of ordinary raw cotton is less than 80%, while the regularity of chemical fibers is usually above 95%.
Number and content of defects
There are three types of impurities in raw cotton.
The first category is impurities that are easy to remove, such as leaf sediment and cottonseed.
The second category is impurities that are easy to break, difficult to remove, and have a greater impact on yarn quality during cleaning, such as sterile seeds, fibrous rod chips, broken seeds, etc.
The third category is the harmful defects that are difficult to remove and have obvious harm to the quality of the yarn, such as soft seed skin, stiff flakes, yellow roots, and foreign fibers.
In addition, the wires and neps in the raw materials, especially the tightly wound wires and neps, are difficult to remove during the carding process, which increases the number of neps and impurities in the yarn.
Chemical fiber
Among all chemical fibers, the friction coefficient and specific resistance of the fiber have the greatest impact on spinning performance and carding quality. In the process of carding and drafting, the static friction coefficient (Us ) and dynamic friction coefficient (Ud ) of fiber and fiber, fiber and carding element, fiber and drafting element have a great relationship with the effect of carding and drafting.
Coefficient of friction | relationship with grooming |
Low Us | Fibers are easy to separate and generate little static electricity |
Low Us | The fibers are not easy to separate, the cotton mesh is well cohesive, and static electricity is easily generated |
Low Ud | Slightly poor grip on fiber, small card clothing with static electricity |
Low Ud | Good grip on fiber, strong static electricity |
Chemical fibers have high specific resistance, and the static electricity generated cannot be eliminated in time. It will cause the cylinder and rolling wheel to be wound around, the cotton web will be difficult to form, the bell mouth will be blocked, and normal production will not be possible. Generally, when the specific resistance of the fiber is less than 1×108, the spinning production is normal.
Carding component factors
The carding effect is closely related to the opening element. Carding and carding components mainly include licker-in roller clothing, cylinder clothing, doffer clothing, fixed flat clothing and movable flat clothing. Fiber carding is a process of continuous carding, transfer, re-carding, and re-transfer. Only by correctly solving the relationship between carding and transfer, can we obtain fully and perfect combing, mixing and transferring, and obtain the best carding effect and carding quality.
Carding machine mechanical state factors
The carding machine is the carrier that realizes various carding processes and completes the entire carding process. If the manufacturing accuracy of the carding machine and the flatness of the card clothing are necessary conditions to ensure carding efficiency, then the mechanical state of the carding machine is a sufficient condition.
From the perspective of long-term production practice,
- The accuracy of carding machine process gauge affects the Uster evenness CV value of carding machine card sliver.
- The distance between the feeding roller and the feeding plate of the carding machine and the size of the holding force affect the unevenness of the sliver of the carding machine.
- The main function of the rear pre-carding area is to card large fiber bundles into small fiber bundles to improve the carding efficiency of the movable flat.
- The pre-carding area is the process of sorting the single fiber after carding and changing the fiber shape.
- The biggest influence on the carding efficiency of the carding machine is mainly the carding area of the movable flat plate. The carding effect in this area determines the carding efficiency and carding quality of the carding machine to a large extent.
Yield factor
The output and quality of the carding machine are a pair of contradictions, which are more prominent at this stage. The ability of the carding machine to remove defects in the mat cotton is called carding efficiency. Under the condition of not considering other factors, the degree of carding is relatively fixed. When the number of defects in the raw material increases, the carding efficiency and carding quality of the carding machine will inevitably decrease. The increase in the output of the carding machine means the increase in the amount of mat cotton processed per unit time, which will inevitably lead to a decline in the carding efficiency and carding quality of the carding machine. In order to ensure the carding efficiency and carding quality of the carding machine, it is necessary to ensure that the carding degree of the carding machine is relatively stable, that is, the number of single fibers subjected to the action of the needle teeth in a unit time remains relatively stable. Modern carding machines increase output from the three aspects of increasing the working arc length of the cylinder, the working width of the cylinder and the working speed of the cylinder. The fundamental reason is to ensure that the carding degree of the carding machine is relatively stable while increasing the output.
The fiber carding effect directly affects the yarn quality. Therefore, carding technology is the core technology in textile engineering. Strengthening the research on carding technology is a key element to stabilize and improve yarn quality.
Comments are closed.
I am genuinely grateful for the knowledge and insights I have gained from reading your blog.
They have managed to create a blog that appeals to a wide range of readers.
This blog is an exquisite blend of educational and entertaining content. It strikes a perfect balance between imparting knowledge and engaging readers with its engaging writing style. These articles are a sheer pleasure to read.
Find inspiration in the thought-provoking content of this blog.