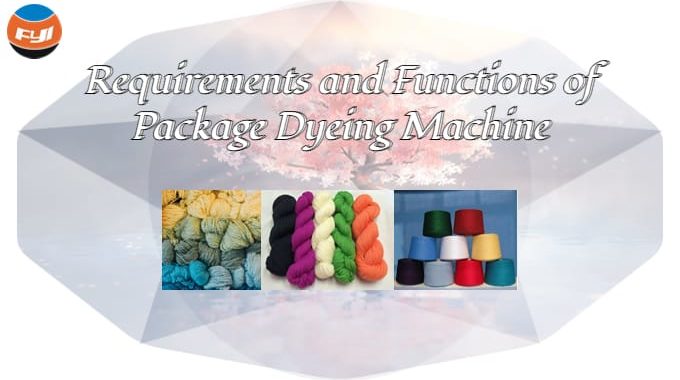
Requirements and Functions of Package Dyeing Machine
For more than a century, the package dyeing machine has been invented, and it is extensively employed in the yarn-dyed and knitting industries because of its short process flow, quick adaptability to variety changes, high efficiency, low energy consumption, and reduced pollution.
The functional scope of the machine has been enlarged in recent years with the development of allied technologies like as fiber materials, coloring materials, and electrical technology. It not only meets the dyeing process criteria, but it also considers variables such as efficiency, energy consumption, and environmental standards.
This study expounds both theoretically and practically on these new functions in order to fully comprehend them.
Basic requirements of package dyeing machine
The essential needs for package dyeing machines are wide production application, high processing quality, economy, and environmental protection.
Applicability
Yarn may be spun from a variety of fibers, and there are several sorts of yarn, thus the package dyeing machine should be capable of processing a diverse range of fibers and yarn shapes.
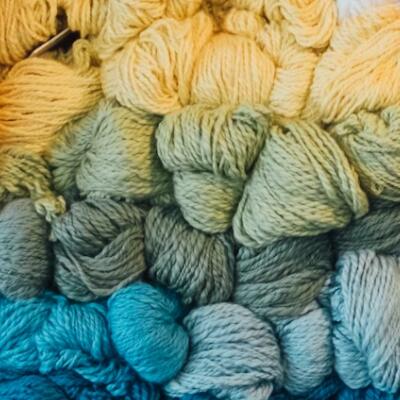
Quality
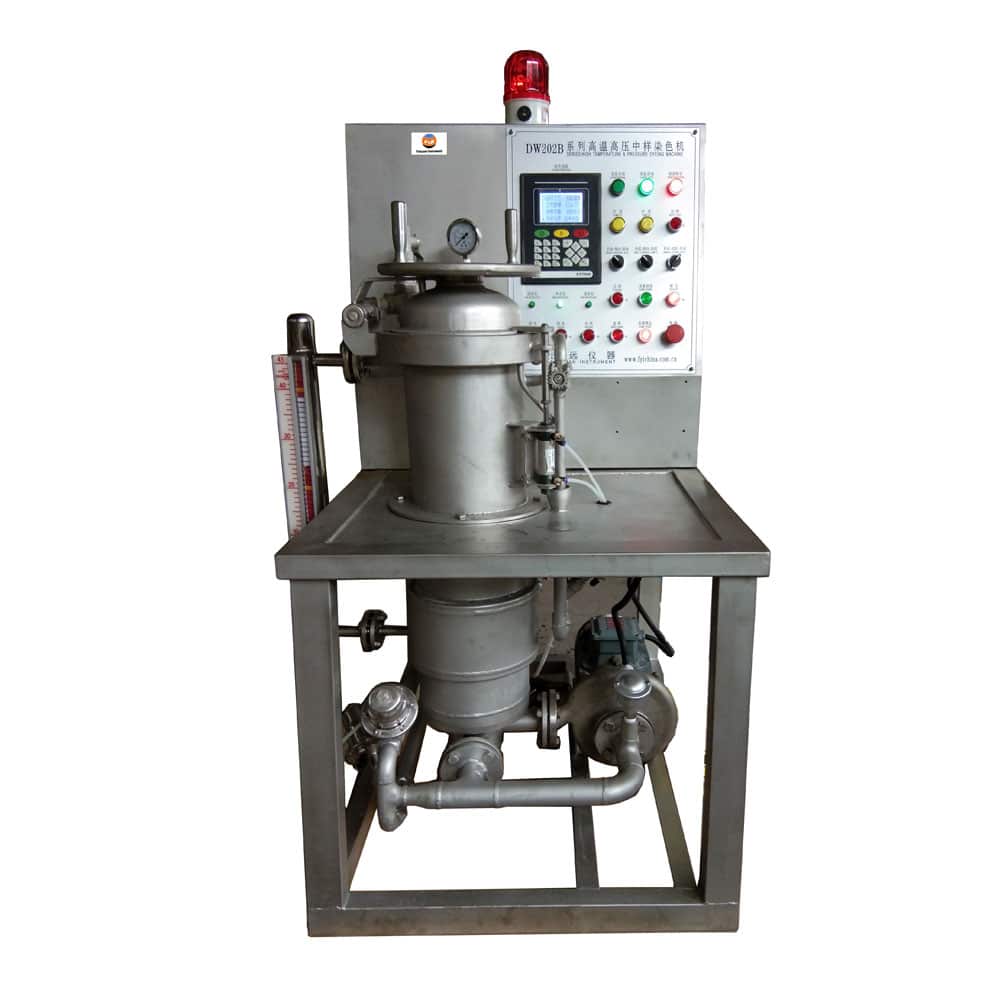
Yarn dyeing is an important step in the process of turning yarn into textile items. Any flaws in the dyeing process will be visible on the cloth, lowering the product’s quality. The most fundamental quality criteria for the package dyeing machine are uniform dyeing and high dyeing repeatability, and the quality of the yarn itself should be maintained, with no lint and continuous yarn.
Economic
The goal of firms investing in package dyeing equipment is to maximize profit by executing yarn dyeing operations. As a result, a low liquor ratio, low energy consumption, a quick dyeing time, and effective dyeing are all essential elements in lowering manufacturing costs.
Environmental friendly
Many countries have given close attention to environmental protection problems. And they have enacted legislation to limit sewage outflow. High-efficiency and water-saving yarn dyeing machines have become the development target in order to decrease sewage output during the dyeing process.
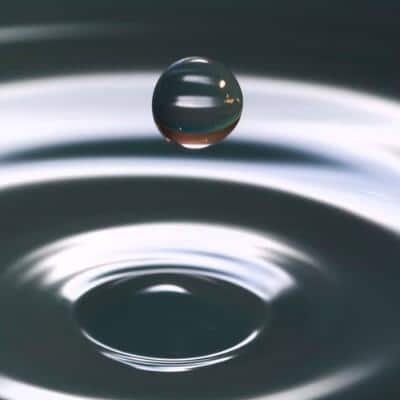
High-end yarn dyeing machines must be equipped with modern computer control systems to accurately regulate the dyeing process, tube operation, and assure dyeing repeatability in order to achieve the aforementioned fundamental criteria.
Click here to know more about the causes of yarn dyeing reproducibility issues.
Main functions of package dyeing machine
Flow control of dye liquor circulation
The circulating pump completes the forced circulation of dye liquid. The goal is to ensure that all dyed items receive the same temperature and exchange frequency of the same dye solution at the same time. The greater the interchange frequency of dye liquor and dyed item, in theory, the better the leveling effect; and the exchange frequency is connected to the circulating flow of dye liquor; the flow is given by the main circulating pump. As a result, the levelness of the package yarn is heavily dependent on the flow velocity of the main circulation pump. Too big or too little is not good for dyeing.
How to select flow?
There are no hard and fast rules for choosing a flow. Early package dyeing machines were designed based on experience to fulfill minimum flow requirements and the notion of no color difference between the interior and exterior of the package. The leakage of dye liquid within and outside the circulation is high in early bobbin dyeing machines due to major faults in the sealing structure between the bobbins, and at least 30% of them create a short circuit. To compensate for this portion of the damage, the flow must be raised.
At the same time, in real applications, the water absorption is vary according to the different types of yarns, as is the needed flow rate. There are various drawbacks to using a constant flow rate. Because of the difference in water absorption, the flow rate of colored pure cotton yarn is greater than that of coloured polyester-cotton mixed yarn. The inner and outer color difference of the pure cotton package yarn may arise if the flow rate of the polyester-cotton blended package yarn is satisfied; whereas the flow rate of the pure cotton package yarn may be satisfied, the polyester-cotton blended package may be deformed or fluffed.
Synchronous dyeing control
The amount of the dye liquid circulating flow not only influences dyeing quality, but also causes some energy waste.
The dyes have varied dye absorption rates in different temperature regions during the dyeing process. A greater cycle frequency should be assured in the temperature portion with high dye absorption; in the temperature section with low dye uptake, the dye liquid cycle frequency can be lowered. This enhances the levelness of the colored material while also lowering energy usage, which has long-term economic advantages. As a result, it is important to manage the circulating flow of dye liquid in real time to guarantee that a reasonable flow can be provided under all operating conditions, including the change of yarn species and load, which is the most recent so-called synchronous dyeing control.
At present, the more advanced package dyeing machines have this kind of control. The control approach is to enter the flow curve data of the main circulating pump under varied speed circumstances into the computer and, using PLC logic control, give the needed Dye liquor circulation flow according on the specific process needs. Simultaneously, the feedback signal is supplied to the PLC via sensing of the pressure differential between the inside and outside of the package to correct for the divergence between the real flow and the programmed flow.
Differential pressure control
It’s worth noting that modern package dyeing machines are labeled with differential pressure control, which is incorrect. The main circulating pump’s head is utilized to overcome the resistance of the complete circulating system (including the package). And the actual working point of the main circulating pump is determined by the intersection of the main pump flow and the pipe network flow
In practice, when the identical master cylinder is loaded with package, the pipe network characteristic curve is likewise determined. The pressure differential mainly refers to the pressure drop created as the dye fluid flows between the inner and outer layers of the package, however it may alter during the dyeing process but cannot be regulated. ( For example, the change of winding density of man-made fibers in contact with water causes changes in pressure drop)
Heat transfer method and structure
The heat exchanger completes the heating, heat preservation, and cooling of the dye fluid throughout the dyeing process. Heat exchangers come in a variety of configurations. Currently, the package dyeing machine uses indirect steam heating and cooling water cooling. Most classic package dyeing machines employ a coil-type heat exchanger positioned in the bottom section of the main cylinder, which requires a specific amount of space in the main cylinder. At the moment, the majority of the most complex package dyeing machines employ tubular heat exchangers located in the main circulation pipeline.
According to the heat transfer principle, the tubular heat exchanger has a greater heat exchange efficiency than the coil type heat exchanger, and the placement of the tubular heat exchanger in the main circulation pipeline can better assure the dye liquid. The homogeneity of temperature throughout the circulation system plays an important role in enhancing dye absorption rate and color fastness throughout the heating or heat preservation process.
The typical way for ensuring the smooth implementation of dyeing temperature control is to raise the heating rate by expanding the heat exchange area, but this takes up too much space and the coil is too lengthy. When steam flows through the end of the coil, condensed water is created mostly after the steam in the front section releases latent heat, which not only does not release heat, but also absorbs heat, lowering the overall heat exchange efficiency. As a result, it is required to strive to enhance the heat transfer coefficient by modifying the shape and structure of the heat exchanger, with one example being the usage of an external tubular heat exchanger.
Reversing device and control
Circulating dye liquor reversing method
There are two ways of reversing the circulating dye liquor: one uses an axial-flow main circulating pump, the other uses a centrifugal pump or a mixed-flow pump.
Axial-flow main circulating pump
The forward and reverse rotation of the main pump allows the dye liquid to flow inside and outside. The structure is basic, and the pipeline takes very little area, which helps to reduce the liquor ratio. Second, the influence is minimal when the dye fluid is reversed. However, because the commutation of dye liquid is achieved by the forward and reverse rotation of the motor in this arrangement, and the switching frequency is high, it has an effect on the motor’s life.
Centrifugal pump or mixed-flow pump
The internal and external circulation of dye liquor is realized through the reversing device.
As the volume of yarn increases, the lift of the axial flow pump becomes difficult to satisfy the requirements, thus most package dyeing machines now utilize a centrifugal pump or a mixed flow pump with a reversing device.
The form of the reversing device
There are several varieties of reversing devices, the most common of which are: gooseneck, right angle elbow, and valve plate.
- The gooseneck type (also known as “X” type) reversing device has a superior streamline flow channel, so the resistance is low, but it takes up a lot of area and costs a lot to make. This construction is primarily intended for reversing the double suction centrifugal pump.
- Right-angle elbow type reversing device, the existing right-angle transition has been changed to arc transition, the local resistance of the flow channel is small, the manufacture is simple, and the rotating shaft is also placed horizontally instead of vertical.
- The valve plate reversing device is the most basic type of reversing device. It has the following properties: steady dye liquor commutation, no impact, and good water flow characteristics. When the main cylinder is filled with yarn, it may cause water to enter inside and outside the yarn at the same time (particularly quick water entry), ensuring that the inside and outside of the yarn absorb water uniformly and the yarn is not washed.
The new package dyeing machine’s reversing mechanism is mostly of the right-angle elbow and valve plate types, and its performance and reliability are excellent.
Commutation control is primarily concerned with controlling the internal and exterior cycle times. Varying yarn kinds, yarn shapes, and winding densities have different control times. Following the successful completion of the process test, the successful parameters must be entered into the computer, and the computer and PLC control system will automatically complete.
Dosing system
The degree of the feeding system’s control program has a significant impact on dyeing quality. The previous single linear feeding method is insufficient for the new coloring process. For light-dyed yarns, for example, linear feeding cannot manage dye uptake, and non-linear metering must be utilized to assure adequate dye uptake. This type of control may be based on the varying hues of different dyes, and the dyes or auxiliaries can be delivered more precisely in different temperature areas, so that the colored item obtains the optimum dyeing result and color fastness. This is especially crucial for reactive dyeing techniques.
Overflow salting device
Reactive dyeing procedures necessitate the use of huge amounts of salt. Controlling the salt content in the dye bath can alter the dye absorption rate and speed. Different amounts and rates of salt addition must be used for dyeing at different depths of color. As a result, the way in which salt is applied should be carefully considered.
The typical method of salt addition is to return a considerable volume of dye liquor from the main tank to the feeding barrel (some auxiliary tanks) to dissolve the salt, then inject it into the main tank. The downside of this approach is that the main tank must reserve a large amount of dye liquor to guarantee that once the liquid required for the salt solution is pulled out, the top yarn in the tank is not exposed to the liquid surface, so the unnecessary liquor ratio is actually increased.
If an overflow type salt addition device is employed, the dissolved salt and salt injection may be performed concurrently, and there is no need for excessive liquid return to keep the main tank’s liquor ratio as low as feasible. At the same time, the concentration of the salt solution may be altered constantly during the salt injection procedure.
Temperature rise proportional control
It is critical to have proportional control over the heating rate. Because the dyeing rate and degree of fixation are proportional to the heating speed during the dyeing process. The frequency of the shut-off valve opening and shutting controls the traditional heating rate. Such a heating curve is truly stepped, and controlling a modest heating rate is challenging. When proportional control is used, the heating rate curve becomes continuous and smooth, temperature fluctuations are eliminated, and the heating rate may be adjusted within a relatively narrow range. This has a nice leveling effect on some coloured yarns that are temperature sensitive.
With the constant development of new dyeing processes, the functions of dyeing machines are becoming more demanding. The features of modern dyeing machines include controlled dyeing, simultaneous dyeing, and quick dyeing. They should study attentively as equipment producers and users to develop or improve the functionality of the equipment.
Comments are closed.
It’s fantastic. Thank you for writing such an informative piece.
Thanks for sharing your post! Keep it up
helpful resources
These are the kinds of blog posts that inspire me to keep learning and exploring new ideas.