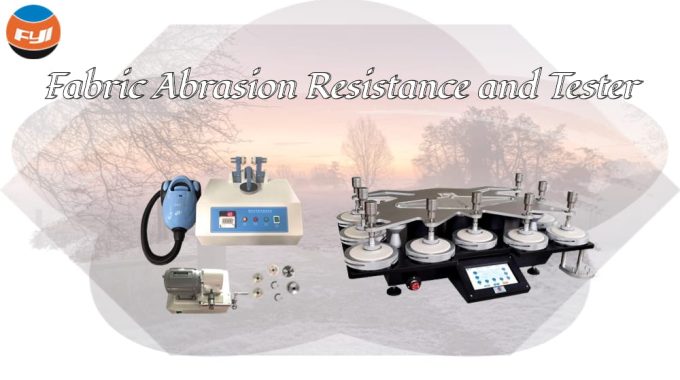
Fabric Abrasion Resistance and Tester
Contents
What is fabric abrasion resistance
Fabric abrasion resistance refers to the fabric’s resistance to wear and tear. Abrasion refers to the phenomenon that fabrics are gradually damaged due to repeated friction from other objects during use.
The abrasion resistance of a fabric is mainly measured by its number of flat wears. When the yarn structure, yarn number and density of the fabric are the same, the number of flat grinding times is closely related to the friction support area of the fabric. That is, the larger the friction support area, the higher the number of flat grinding times.
When using instruments to measure the abrasion resistance of fabrics in the laboratory, instruments are used to simulate various wear conditions of the fabrics in actual wear. Wear mainly includes the following types:
(1) Flat wear: The fabric is subject to reciprocating or rotating plane friction, such as the wear under the sleeves of clothes, the buttocks of trousers, and the bottom of socks.
(2) Bend wear: It is the repeated friction of the fabric in the bending state, such as the wear and tear of elbows, knees and other parts.
(3) Folding: It is the wear and tear on the folded edges of fabrics, such as the wear on the collars, cuffs, trousers and other folded edges of clothes.
4) Dynamic wear: such as the wear and tear of fabrics in a washing machine.
The abrasion resistance of fabrics is evaluated by the weight loss of the fabric after a certain number of wears. Under certain conditions, the greater the weight loss, the worse the wear resistance of the fabric.
The factors affecting fabric abrasion resistance
Fiber properties
Geometric Features
- The longer the fiber, the better the wear resistance.
- Moderate fineness is beneficial to wear resistance. If it is too thin, the stress will be great; if it is too thick, the number of fibers will be small, the cohesion force will be small, and the bending resistance will be poor.
- The flexural abrasion resistance and folding abrasion resistance of special-shaped fiber fabrics are worse than those of round fiber fabrics.
Mechanical properties
If the elongation at break, elastic recovery rate and specific work at break are large, the abrasion resistance of the fabric is generally better.
Yarn structure
- The twist should be moderate. If it is too large, the fiber segments will have small mobility, hardness, and small contact surface; if it is too small, the yarn structure will be loose and the fibers will be easily extracted.
- The thicker the yarn, the better the wear resistance, especially flat wear.
- The yarn has good consistency and is wear-resistant. (The thick joints are loose and the fibers are easy to extract)
- Thread fabrics have better resistance to flat abrasion than yarn fabrics, but have poorer resistance to curved abrasion and hemming abrasion.
- The radial distribution of blended yarn requires fibers with good wear resistance to be distributed in the outer layer of the yarn.
Fabric structure
- The higher the square meter weight, the better the wear resistance.
- The structural phase and supporting surface are near the fifth structural phase. The supporting surface is large and the wear resistance is good.
- The density of the fabric is moderate and the wear resistance is good.
- Fabric organization, fabric density and organization should be considered comprehensively. The warp and weft densities are low, and the plain weave is more wear-resistant; the warp and weft densities are high, and the satin weave is more wear-resistant.
Test conditions
- Selected abrasives.
- Tension and pressure.
- Temperature and humidity in the experimental environment.
- The direction of friction, especially for satin.
Finishing
The abrasion resistance of cotton and viscose fabrics after finishing, different pressures during testing show different results. For example, the wear resistance decreases when the pressure is high, and increases when the pressure is low.
How to improve the wear resistance of fabrics
Fiber properties
The main properties that affect the wear resistance of fibers are the physical properties of fiber stretching, bending and shearing. Comparing the types of fibers, the abrasion resistance is: nylon > polypropylene > vinylon > ethylene > polyester > acrylic > chlorine > wool > silk > cotton > linen > rich and strong fiber > cupro fiber > viscose fiber > acetate fiber >Fiberglass. Comparing the fiber structure, the wear resistance of circular cross-section structural fibers is higher than the strength of special-shaped fibers; the thinner the fibers, the worse the wear resistance. Therefore, in order to improve the wear resistance, it is necessary to choose circular cross-section fibers with good wear resistance.
Types of yarn
The abrasion resistance of yarn is closely related to the structure of the yarn. Different spinning methods, different fiber winding methods in the yarn, different cohesion forces between fibers, and different wear resistance. In traditional ring-spun yarn, most of the fibers are in the form of spirals. When rubbed repeatedly, the spiral fibers gradually turn into axial fibers. The yarn is prone to lose twist, disintegrate and wear out quickly, so the wear resistance is poor. Non-traditional spinning has obvious advantages in wear resistance. Rotor yarn, air-jet yarn and vortex yarn are all composed of yarn core and outer fiber. The surface of the yarn is covered with irregular winding fibers, and the yarn is not easy to disintegrate. At the same time, the friction coefficient of the yarn surface is large, and the yarns in the fabric have good cohesion with each other and are not prone to relative slippage, so the wear resistance is improved. Compared with ring-spun yarn, the fibers of compact spinning yarn are arranged neatly and straightly, the yarn structure is tight, and the fibers are not easy to fall apart, so the yarn has good wear resistance.
Fabric organization
The organizational structure of the fabric determines the tightness and thickness of the paper film, which has a significant impact on its wear resistance. Among the three basic structures, the plain weave has the best wear resistance, the satin weave has the worst wear resistance, and the twill weave is in the middle.
Fabric finishing methods
Fabric finishing is a kind of finishing that combines physical and chemical methods to give the fabric certain properties. Such as protective finishing: waterproof, fireproof, mildew-proof, oil-proof, cold-proof, atomic radiation-proof, melt-proof, pilling-proof, etc. Resin finishing can significantly improve the wear resistance of fabrics.
Fabric abrasion tester
Martindale Abrasion And Pilling Tester YG401 Plus
YG401 Series Martindale Abrasion and Pilling Machine (Plus) is used to determine the abrasion resistance of wool and wool blends woven fabrics, knitted fabrics and nonwovens under certain pressures. Also used for pilling property test of most fabrics (especially woolen woven fabrics) under low pressure. It was designed to give a controlled amount of multi-directional abrasion, between the fabric surface and a crossbred wool abrading fabric, at comparatively low pressure until thread breakdown, or unacceptable change in color or appearance occurs.
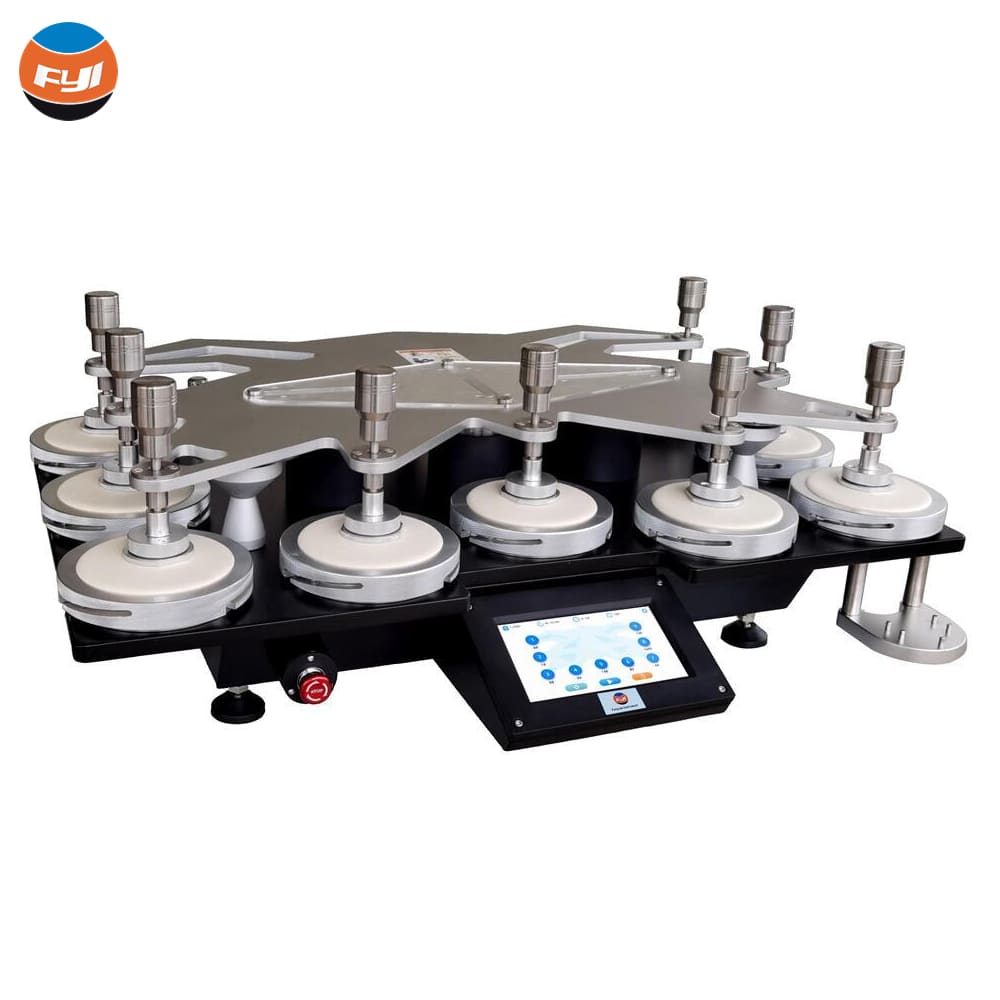
Taber Abrasion Tester YG522N
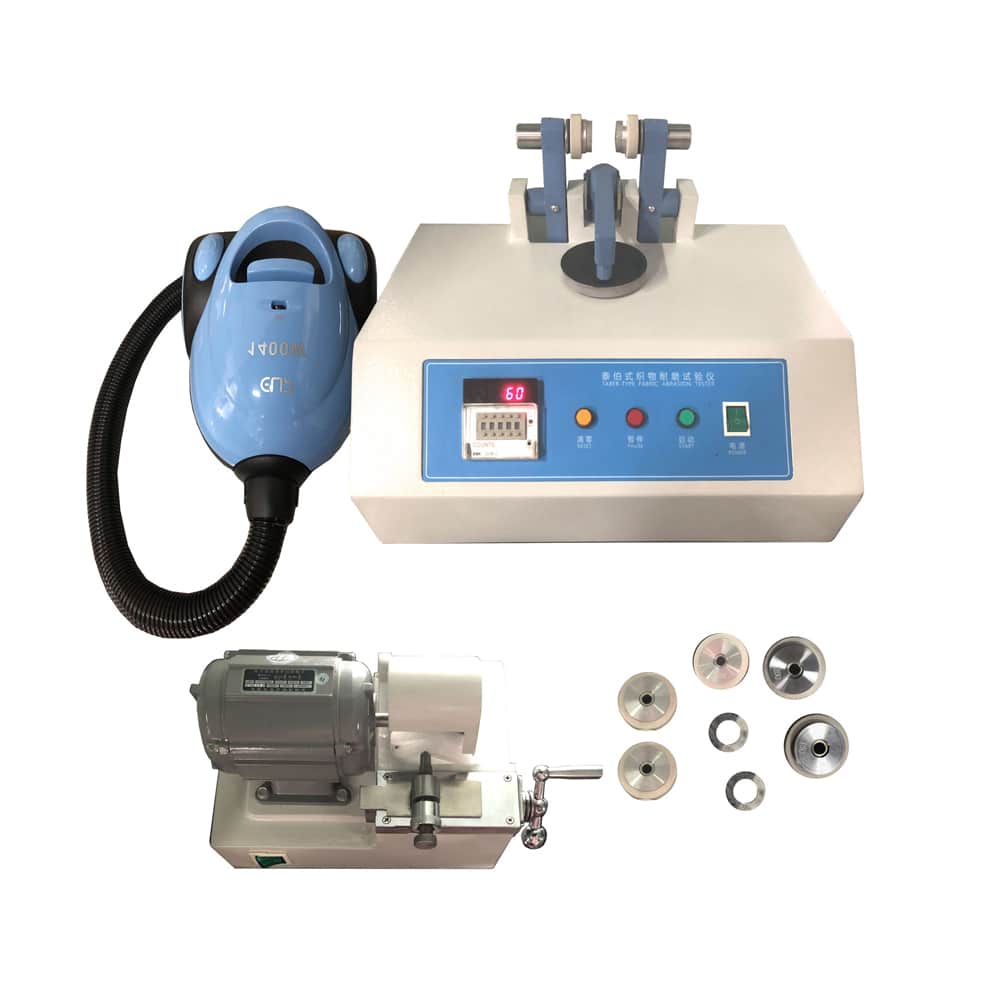
Taber abrasion tester is suitable to conduct wear resistance test for different materials, such as cloth, paper, paint, plywood, leather, floor tiles, natural rubber, etc. Fix the sample on the test turntable, select the required test weight, and ensure that the test grinding wheel does not contact with the sample fixed fixture during the testing process. Adjust the governor switch to the minimum. After setting the test number according to the test requirements, the whole machine is in the test state.
Leave a Reply
You must be logged in to post a comment.
All aspects of the blog, from its layout to its use of multimedia, are carefully crafted to enhance the reader’s experience.
Both entertaining and educational, this blog strikes the perfect balance between substance and style.