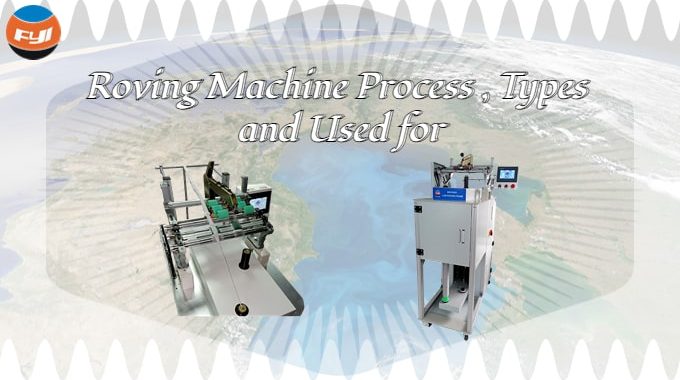
Roving Machine Process , Types and Used for
The main function of the roving machine is to draw and twist the fiber strips into roving to meet the requirements of the spinning frame processing.
Contents
What is roving used for?
The mature strips made by drawing frame are relatively heavy and must be drawn 50 times to 400 times to reach the required fineness of yarn.At present the spinning frame does not have such a large drawing capacity. In the 1950s, it was tried to spin the cooked strips directly without roving process by using a large draft spinning frame.Due to excessive draft, the short length of yarn will deteriorate. At the same time, feeding the spinning frame directly in strip form will encounter difficulties in many aspects and is not economical.
Therefore, in the traditional spinning process, in order to ensure the quality of yarn, a roving process is set between the jointing and the fine yarn to share part of the draft.However, new spinning technologies, such as rotary spinning, jet spinning, friction spinning and dust cage spinning, have eliminated the roving process. However, it is still necessary to keep the roving process in the spinning of most yarn counts, especially those with fine count and high quality requirements. The tasks of roving process are:
1. Draw, lengthen and thin the ripe strips of the drawing frame and spin into roving yarn to adapt to the drawing capacity of the spinning frame.
2. The roving yarn is twist properly to make it have a certain strength. It can be wound into a certain shape, which is convenient for storage and handling, and suitable for unwinding feeding on the spinning frame to prevent accidental drafting.
3. After drawing and twisting of roving frame, it can further improve the separation, straightening and cleanliness of fibers, facilitate the drawing of spinning frame, and improve the quality of yarn.
What is the roving process?
Roving quantification
Under the condition of standard temperature and humidity, the weight per unit length of roving is called quantification. The roving quantity should be determined according to the combination of the ripened quantity, the drawing capacity of the spinning frame, the yarn count variety and the performance of the roving equipment. When spinning pure cotton yarn, the number of ripe strips is 2.5~ 6 g/m, the drawing capacity of the spinning frame is 12~45 times, and the drawing ratio of the roving frame is 5~11.
Variety(tex) | 32~100 | 20~30 | 10~18 | 6.0~9.0 |
Roving weight(g/10m) | 5.5~11.5 | 4.8~6.9 | 3.0~5.8 | 2.3~3.3 |
Spindle speed
The control range of spindle speed of domestic traditional spindle supporting roving frame is; Coarse yarn 500~ 700r/min, medium yarn 600~85or/min, extra fine yarn 800~900r/min. Suspended ingot roving frame can break through the above range, the general fine count can reach 1000r/min.
Stretch
- Total draft multiple: The total draft multiple selected by the roving frame is mainly determined by the number of fine yarn count, the draft multiple of the spinning frame and the quantity of cooked strips. At present, with the development of the ripe strip to the heavy weight, the spinning frame has generally adopted the double ring large draft, and the drafting device of the roving frame requires strong adaptability and wide range of drafting multiple. The drafting ratio of double – ring roving frame is generally 4 ~12. In order to ensure product quality, it is not recommended to use less than 5 times the draft, generally the highest use of 9-10 times, rarely to 11 times. In the spinning of extra fine yarn, in addition to increasing the drafting ratio of coarse and fine yarn appropriately, it is necessary to reduce the number of ripe strips. Too large drafting ratio will lead to the deterioration of the evenness of the short pieces of the product.
- Drafting distribution: The three-roller and double-coil drafting has better control over the fiber, and the main drafting is only tension drafting in the anterior and posterior regions. The extension ratio of the posterior zone should be as small as possible, usually 1.15~1.25, so as not to spread the whisker strips too much in the posterior zone, so as not to weaken the adhesion force between fibers. In the four-roller double-ring drafting, the tension drawing is fixed between the front roller and the second roller, the main drawing area of the second and third roller is the drawing area of the back between the third and fourth roller.
- Clamp spacing of roller and collar pin: in the form of double collar drafting, the width of the epithelial collar pin is first selected according to the length of the processed fiber. Generally, there are three kinds of pin width, short to adapt to all kinds of raw cotton and chemical fiber below 40mm, the middle of the chemical fiber below 50mm, large for the chemical fiber below 65mm. In the form of three-roller double-coil drafting, the spacing between the front, middle and lower rollers must be determined according to the width of the epithelial pin and the length of the free zone.
- Leather ring clamp spacing: It is determined according to the fiber properties, the quantitative weight of ripe strips and roving, as well as the control degree of the fiber by the elastic clamp of leather ring.
Roving weight(g/10m) | Under 3.8 | 3.3~5.2 | 3.8~5.7 | 5.0~6.9 | 6.2~7.9 | 7.1 above |
Gauge block size A(mm) Pin spacing X(mm) | 5.5 4 | 6 4.5 | 6.5 5 | 7.5 6 | 8.5 7 | 9.5 8 |
- Roller pressure
Roller pressure: The roller pressure of the roving frame is to ensure that the roller clamp mouth has enough holding force to overcome the drafting force and prevent the yarn from slipping and speed stratification at the roller clamp mouth. Roving frame spring pressure, the pressure can be adjusted according to the draft force. In order to ensure normal drafting, the output roller pliers in the main drafting area of the double coil must maintain a large pressure. Because of the small drafting force in the back area, the pressure between the upper and lower roller and between the back roller can be small. The drafting force is related to fiber property, quantity, drafting multiple and roller spacing, which should be considered comprehensively. In addition, it is also necessary to consider the running speed of the roller. Generally, high speed pressure should be heavy, and vice versa. - Aggregator: the aggregator on the roving frame is mainly set up to prevent fiber diffusion. The opening size of the collector, the front area should be appropriate to the output quantity, and the back area and feed. The entry aggregator is adapted to the feeding ration.
Twist
Roving should have a certain twist to withstand the tension of roving winding and unwinding in the next process, to reduce abnormal elongation and prevent broken ends. Twist, on the other hand, serves as an additional boundary of friction in the back stretch of the yarn to control the movement of the fibers. The twist of roving is determined mainly by the length of the fiber and the fineness of the roving. It is also selected with reference to other properties of the fiber, the process of the spinning back area, and the breakage of the roving end.
Winding density
Roving density has a direct impact on roving capacity, so it must be tightly wound to increase the capacity. Axial density configuration must be based on the principle of yarn ring alignment. In small yarn, the gap between roving rings is less than 0.5mm. Under the condition of naked eye observation, the surface of the tube can be faintly seen when winding the first layer of yarn. Gaps should not be too thin, should not be too dense, to prevent embedding and overlap.
Roving tension
Roving is a product of weak twist. After being subjected to tension, it is easy to produce accidental draft, resulting in yarn unhook. When the tension is too large, the accidental draft will increase and the roving will deteriorate. The tension is too small, the weight of the full tube is reduced, and it is difficult to carry and store and unwind. Therefore, too much tension will affect the breaking rate of roving frame and spinning frame, increase labor intensity and reduce production efficiency. If the tension difference of roving between different pastilles on the same table and in the same row is too large, the difference of roving packing and capacity will increase, which will not only affect the quality of roving, broken end and normal operation of the roving frame, but also affect the roving pagoda section working method on the spinning frame, and increase the labor intensity of workers. When the tension difference between large and small yarns, front and back yarns, as well as between tables is too large, it will directly affect the unevenness of long roving segments and weight of fine yarns. So to spin quality yarn, we must control roving tension.
What are the different types of roving?
Roving frame according to the twisting mechanism is divided into wing roving frame and twisting roving frame. Spun roving frame produces spun roving by continuously applying twist to the yarn strip by rotating the spun wing. The spinning roving machine relies on a pair of rolling sheets to clamp and twist the yarn strips, forming false twisting alternating between positive and negative twisting on the yarn strips to produce no twisting roving yarn. Ingot roving frame and twisting roving frame can be divided into first, second and single roving frame. Various roving frames have different feeding forms, roving rolls and machine number of ingot, but the machine structure and function are roughly the same.
DW7030H Lab Roving Frame
DW7030H is a model independently developed by Fanyuan. It is used to spin cotton sliver to be roving through drafting and flyer spinning. It’s the ideal system for teaching, researching, etc.
Feature
- Delta brand PLC, drive and servo motor;
- PLC+Touch screen control, easy to learn and operate;
- Use touch screen as man-machine interface, input technical parameters and show machine running state by touch screen;
- Use Z twist turning;
- Rotation speed of spindle accurate to ±1%;
- Aluminum profile body frame with four casters, free to move;
- Modular independent drive for drafting, spindle blade and flyer;
- Ball line guide rail pair design, low friction resistance and low power consumption, ensuring the reliability of supporting plate when moving up and down;
- Multi-functional design, easy to clean, set and maintain.
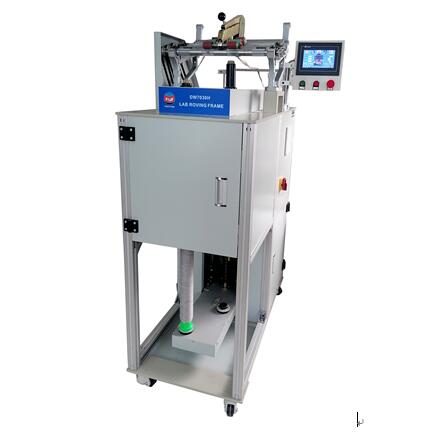
Specification
Control mode | Touch screen & PLC |
Number of spindles Applicable fiber length | 2 22~50mm |
Can size | 250mm ×550mm |
Roller size | 28/28/28mm |
Pressure mode | Spring-weighted |
Draft multiple | 4~12times |
Twist range | 15~80 twist/m |
Flyer form | Suspended |
Spindle speed range | 20~800rpm |
Roving bobbin size | φ45×445mm |
Capacity | Approx.0.25~1kg/h |
Yarn density range | 200~1,000tex |
Leave a Reply
You must be logged in to post a comment.
Your writing has a way of making me feel inspired and motivated.
Your attention to detail is evident in every word you write.
Did you ever wish for a blog that simplifies complex topics? This one does it brilliantly.