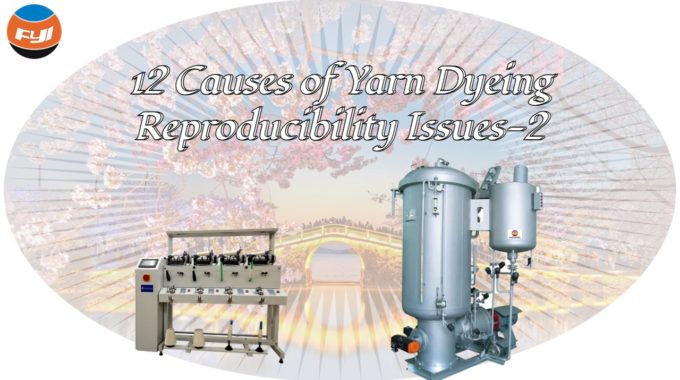
12 Causes of Yarn Dyeing Reproducibility Issues-2
The five objective outside factors that affect the reproducibility of yarn dyeing have been listed before. The seven additional human-generated subjective elements and solutions are discussed below.
Subjective elements of yarn dyeing reproducibility issues
1、Winding quality
The apparent color depth of the cheese yarn’s dip-dyed color is greatly influenced by the weight ratio of the dye to the material being dyed. In most cases, package dyeing and loading just counts the quantity of bobbins; additional weighing is not necessary. The weight of the loaded yarn is thus determined by the weight of the winding. Therefore, the winding must weigh 100% of all loose packages.
Additionally, holes are drilled into the bobbin and the beam coil to allow the dye liquor to pass through. It will result in “eye exposure” if the bobbin winding position is incorrect or the reciprocating distance is insufficient. In addition to making the end face of the bobbin flush, the dye liquor will be “short-circuited” from the “exposed eye,” which will also have an impact on the flow of other bobbins.
Furthermore, the resistance to the dye liquid circulation is strongly correlated with the density of the loose tube. Due to the high density and resistance, the dye liquor’s circulatory flow is altered. The frequency of dye liquid circulation and the number of cycles in a certain amount of time are two examples of the characteristics that alter as a result. This results in different shades of dyed objects.
2、Pretreatment
The degree of impurity removal during pretreatment, the level of gross efficiency, the degree of whiteness, the pH after washing, and the hydrogen peroxide depuration following bleaching will all have an impact on the dye uptake rate and shade.
The measurement and weighing of other chemicals is typically given less attention by dye factories than the measurement and weighing of dye strength. The amount of caustic soda, soda ash, and hydrogen peroxide used is determined in accordance with the stated instructions rather than being analysed. The pretreatment impact will vary due to the infrequent titration of the dye solution, which will alter the shade and hue of the dyed materials.
3、Selection of dyes
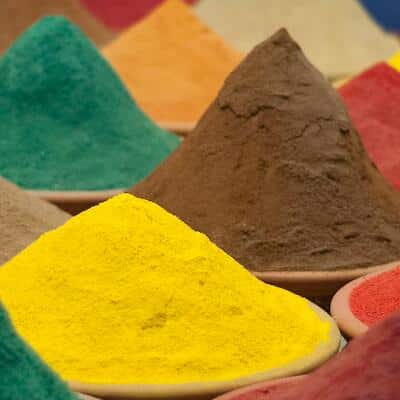
Reactive dyes, vat dyes, direct dyes, etc. are the most common types of dyes used on cotton yarn.
However, in some seasoned dyeing plants, reactive dyes are typically used for dyeing cotton yarn whereas disperse dyes and reactive dyes are used for dyeing blended polyester-cotton yarn. To ensure reproducibility, consider their compatibility, sensitivity, and quality stability while making your choice.
4、The rationality of dyeing process
Despite the selection of the appropriate dyes, the dyeing process design is illogical, and the cylinder difference will also happen. For instance, the design of the temperature, the heating rate, the holding rate, the holding time, the amount of additives, the science-based nature of the adding techniques, and the logic of the post-treatment process design. They will all have an impact on the variation in the amount of dye uptake, which will produce a color difference.
For instance, the pH of the dye solution has a significant impact on the fixation and hydrolysis of reactive dyes. The scientific feeding method involves keeping the pH level at a constant level (for instance, 11.5), which has a significant impact on the feeding method and feeding rate. When it is introduced all at once or alternately quickly and slowly, the pH level will change, resulting in distinct fixation and hydrolysis colors. There are thus several tones of light.
5、Operational factors
Operator and manager are unaware that their actions do not adhere to the standards of the process, and some are even incorrect. like:
- The pipette is at roughly 45 degrees when the proofreader looks at the scale of the pipette (should be vertical).
- The dyer is not a special person responsible for dyeing the same color, but multiple people operate.
- Weighers use the same spoon to pick up different dyes, wiping only with a dry rag.
- Each prescription’s dyes are assembled in a single container, weighed, and then put into a bucket.
The operator is careless. like:
- When filling the bobbins, the inadequate sealing between the bobbins is not addressed.
- The winding weight is not handled if it is greater than the standard.
- When the mixture was mixed, the material tank wasn’t meticulously cleaned.
- The auxiliary is not properly weighed.
- The operators acted independently because the management staff failed to develop proper and strict operating procedures.
6、Management issues
The entire production process is involved in dyeing repeatability, not only the dyeing step. This is a systematic project, which is also closely related to management. Such as the administration of grey yarn and semi-products, dye, measurements, technical, and laboratory management.
The same color number should be used with the same batch of greige yarn. You must repeat the sample if you want to replace it. For dyes made by different manufacturers, Even different batches of dyes from the same plant will have repeatability issues . The dyeing of package yarn is prone to poor reproducibility between production batches because of a lack of management attention.
7、Lab tracking of mass production
First off, rather than transferring the technique and recipe to mass production, the laboratory helps manufacturing by simulating mass production. in order to attain a high level of consistency in both lab and large production settings. The laboratory should take part in the completion when the color does not match in mass production and needs to be corrected. The laboratory needs to examine and validate the data generated by mass production (color and light differences between large and small samples). To minimize color retouching, determine the correlation between the swatch production for each dye.
In addition, it is necessary to achieve high reproducibility in large-scale production and laboratory. The first thing to do is to achieve laboratory-to-lab reproducibility, as well as large-scale production and large-scale production reproducibility. Otherwise, mass production and laboratory reproducibility will be poor.
Solutions
In the manufacture of yarn, inconsistent yarn dyeing is a common problem. I believe that the management should be improved in the following areas and work to assure the reproducility of yarn dyeing from the ground up, based on the yarn dyeing scenario in our plant and my partial understanding of the production operation:
Yarn dyeing machine selection
To provide the basic conditions of reproducibility on the equipment, the yarn dyeing machine that can guarantee the dyeing quality of the product and the capability of reducing the dyeing time should be chosen.
Winding
The density of the bobbin yarn should typically be managed between 0.35 and 0.40 in order to ensure coloring through, and the density after compression should be controlled between 0.41 and 0.46.
Dyes
- Be careful when selecting the dye type.
- Pay close attention to the dye batch inspection.
- Keep the dye room dry, clean, and well-ventilated.
- Make sure your dyes are moisture-proof.
Process parameters
The key to dyeing is the creation and control of process parameters.
A set of rational and scientific parameters must be used to support an effective dyeing procedure. We should be mindful of the manner and timing of feeding, similar to the amount of salt and alkali. To prevent the aggregation and precipitation of colours caused by insufficient salt dissolving and poor dyeing reproducibility, salt that has been prepared in advance might be utilized.
Proofing and Lofting
The laboratory samples should, to the greatest extent feasible, replicate the actual conditions of mass production, including cycle time, heating rate, salt and alkali addition, post-dyeing treatment, color matching light source, etc. As a result, a medium sample experiment is required before producing big samples. During mass production, laboratory staff collect track records as reference materials.
The craftsman should adapt the process when the large sample is put into production in accordance with the distinction between the small sample and the large sample, as well as the prior experience and the mastery of the dye performance. Thus, the method of mass production is achieved.
The manufacturing yarn and the sample should be identical. Both the pre- and post-treatment phases should follow the same pattern.In order to prevent changes in the concentration and intensity of the dye, the sample dye mother liquor should not be stored for an excessively extended period of time.
Operational factors
Operators should be aware of:
- Operation need to be uniform.
- Dye is used in science.
- Utilize less additives.
- Make use of precise measuring equipment.
Other factors
- Small samples should be made with water that is similar to that used in large-scale production, and soft water should be utilized wherever possible. To maintain a stable PH value for dyeing, soft water’s PH value should be kept at around 7.0.
- Improve the way that additives are inspected for quality.
- The lab should resample all raw cotton and blended cotton used in various batches before dyeing. If the shade changes, it needs to be quickly changed.
- The foundation of dyeing is pretreatment. If the pretreatment is poor, the foundation is weak, and the dyeing will have poor reproducibility.
These are all the causes of yarn dyeing reproducibility issues.
Comments are closed.
Trying to express gratitude for the fantastic lucidity in your writing will not be sufficient. I’ll snag your RSS feed right away to stay informed of any updates.
Your blog is a true testament to your dedication and hard work as a writer.
A blog that manages to be both informative and entertaining is a rare find, but this one accomplishes just that.