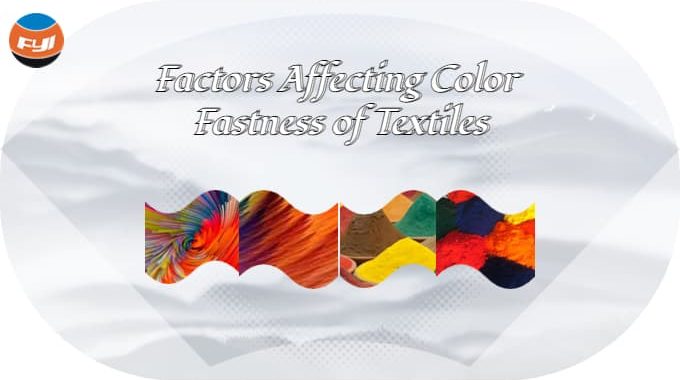
Factors Affecting Color Fastness of Textiles
The elements influencing textile color fastness are classified as internal and exterior. Internal variables are the stiffness of the dye-fiber combination, whereas external elements are the external forces applied by external sources or the ambient conditions given by the product during usage. Because external causes cannot be controlled, manufacturers should endeavor to improve the color fastness of their products.
Choice of dyestuff
The color fastness of a product is determined by the dyes. There is no way to obtain high-quality color fastness if the dyeing chemicals are not chosen correctly, regardless of how wonderful the auxiliaries and dyeing method are. Only after selecting the appropriate dye can we go to the following stage.
According to the characteristics of the fiber
Varied dyes have different combinations with fibers, and the toughness of the bindings varies as well. After determining the type of dye, then select a dye with good dyeing performance.
When dyeing wool cloth, for example, the same strong acid dye, China is not as good as other countries’ strong acid dye dyeing performance. Not only is the color bad, but so is the hardness of the combination. Or the same strong acid dye, and the combination fastness and vividness of different dyes and wool are also diverse. Color fastness of wool yarn colored with weak acid dyes, for example, is greater than that of strong acid dyes. And cotton or recycled cellulose fiber cloth may be dyed with either direct or reactive dyes. Silk textiles can be used in conjunction with mild acid dyes, reactive dyes, and individual direct dyes.
The color depth
Following the determination of the main categories of dyes, it is vital to select which dye to employ based on the color system and depth of the dyed color.
To begin, pick a dye that is similar to the desired color’s shade, and if there is any departure, use different dyes to alter the color.
Second, consider the color fastness index of the dye you’ve chosen. The dye’s color fastness is low, and the method can only increase the color fastness by half a level at best.
Third, check to determine whether the dye’s saturation can achieve the desired color depth. If you pick a dye with a very low dying rate, even if the requisite high-depth color may be attained temporarily after processing, the dye will not be stably attached and will flake off during usage or reprocessing.
The color fastness rating of the dye itself
The color fastness series of the dye is introduced in the introduction of each dye. When selecting dyes, follow the color fastness series specified by the product, and the color fastness of the dyes that match the color should be identical. The color fastness of the dye, for example, may only reach 2-3 or even 1-2 classes, and even the greatest auxiliaries and dyeing procedures cannot dye items with 4-5 degrees of color fastness.
Because the color fastness of the dye is mostly determined by the bonding force between the dye and the fiber, no amount of external force can make them connect securely. Even if it improves once the color is fixed, it cannot survive the harm caused by external causes such as washing and friction.
Dyeing speed
Different dyes have different dye absorption speeds, and the dye uptake speed of the same dye varies depending on the dyeing circumstances. As a result, while selecting dyes, the dyeing rate should be taken into account; otherwise, dyes will compete. That is, one of the dyes occupies the dyeing position of the fiber in advance, allowing other colors to simply dye the surface of the fiber and not make a solid bond with the fiber equally, causing it to be destroyed first in the subsequent process or in daily usage. Because of this, certain hues fade to an entirely different tint from the original. Therefore, when choosing a dye, it is necessary to choose a dye that has a similar dyeing rate to the fiber under the same conditions, which is also very beneficial to the next step of formulating the process.
Good compatibilities between dyes
Different dyes within the same dye family have varying degrees of compatibility. The higher the compatibility number, the better the capacity of dyes to match colors. The dyes that match the hue must be compatible with one another. For colors that are difficult to spell, it is recommended to utilize three main colors. The three fundamental colors are the most compatible among each dye kind, and they can also match the most full and exact colors. As a result, it is recommended to utilize the three fundamental colors to match certain unusual and difficult-to-dye hues, and avoid using additional dyes carelessly, which is prone to competition and dyeing.
Minimize the number of dyes required
When choosing dyes, you should first choose a dye with a shade similar to the desired color, and then use one or two dyes to supplement the shade that the main dye lacks, and you should choose a dye that belongs to the same color system. The color dyed in this way is pure, bright and clean, gorgeous and full.
Try not to use four or five dyes for coloring, because it is not easy to color, and it is not easy to operate a large number of dyeing. Moreover, although the color is matched, the dyed shade is not bright and full, and the dye cannot be fully combined with the fiber, resulting in poor color fastness.
Selection and use of additives
Choose the right adjuvant
The selection of auxiliaries is critical after deciding the kind of dye. In general, use auxiliaries that are as close to the dye as feasible. If it is a common dye that is used on a regular basis, it is vital to concentrate on determining the amount of auxiliaries and the technique of usage. Dyes are difficult to exhaust in dark hues, and additives can be applied in batches to enhance the exhaustion rate. It may also boost dye adsorption speed and play a function in color fixing.
Minimize the amount of retarder
The quantity of retarding chemical used to retard dyeing should be minimized as much as feasible, since it would have a stripping effect otherwise. On the one hand, it will lower the dye absorption rate, but it will also diminish the binding force between the dye and the fiber, reducing color fastness. The level dyeing effect may be created for the hue that is simple to dye flowers by changing the dye and heating speed.
Selection of color fixing agent
The application of a color fixing agent improves the color fastness of dyes by at least 0.5 to 1 grade. However, while selecting a fixing agent, the dye’s fastness should be examined as a whole, not simply specific elements. For example, when reactive dyes are treated with cationic low-molecular-weight or polyamine-type color-fixing agents, the fabric’s washing fastness is 4 to 5, but its light fastness decreases. We must rigorously regulate the amount of color fixing agent, color fixing temperature, and color fixing time while fixing the color.
Soaping and washing
When soaping and washing, it must be fully washed, and the washing temperature and time must be guaranteed, otherwise, the floating color on the surface of the fabric will fade during use.
Use of softener
A softener for treatment is required to give the product a plump and soft appearance. Softeners are classified as cationic, anionic, nonionic, or silicone. After the dyeing process, the softener is the final step. The subsequent interaction between the dye and the softener may impair color fastness, especially if the silicone softener is used after dyeing with acid dyes; portion of the dye may even be lost during softening, significantly lightening the color. As a result, while softening, the amount of softener should be exactly perfect; otherwise, it will not only feel sticky, but will also impair the color.
Dyeing process
The dyeing process is the most important link in the dyeing process. The dyeing duration, heating rate, and holding time must be decided while developing the process based on the dye and the product. For light colors, the heating speed should be moderate and the holding time should be short; for dark colors, the heating speed can be high but the holding time must be long enough for the dye and fiber to properly mix and play a part in color fixing.
In summary, numerous factors influence the color fastness of fabrics. For internal factors, all production processes are in place to ensure that the product has excellent color fastness indicators and meets the requirements of daily use and reprocessing; for external factors, all production processes are in place to ensure that the product meets the requirements of daily use and reprocessing. In terms of color fastness, we must consider the variables that might diminish color fastness, such as washing temperature, detergent and washing technique, friction strength, and exposure length, in accordance with the product’s usage requirements, so that the product can be utilized more effectively.
Very nice post and right to the point. Thank you.
We are happy now to see this post because of the you put good images, good choice of the words. You choose best topic and good information provide. Thanks a sharing nice article.
thank you for the info you have provided